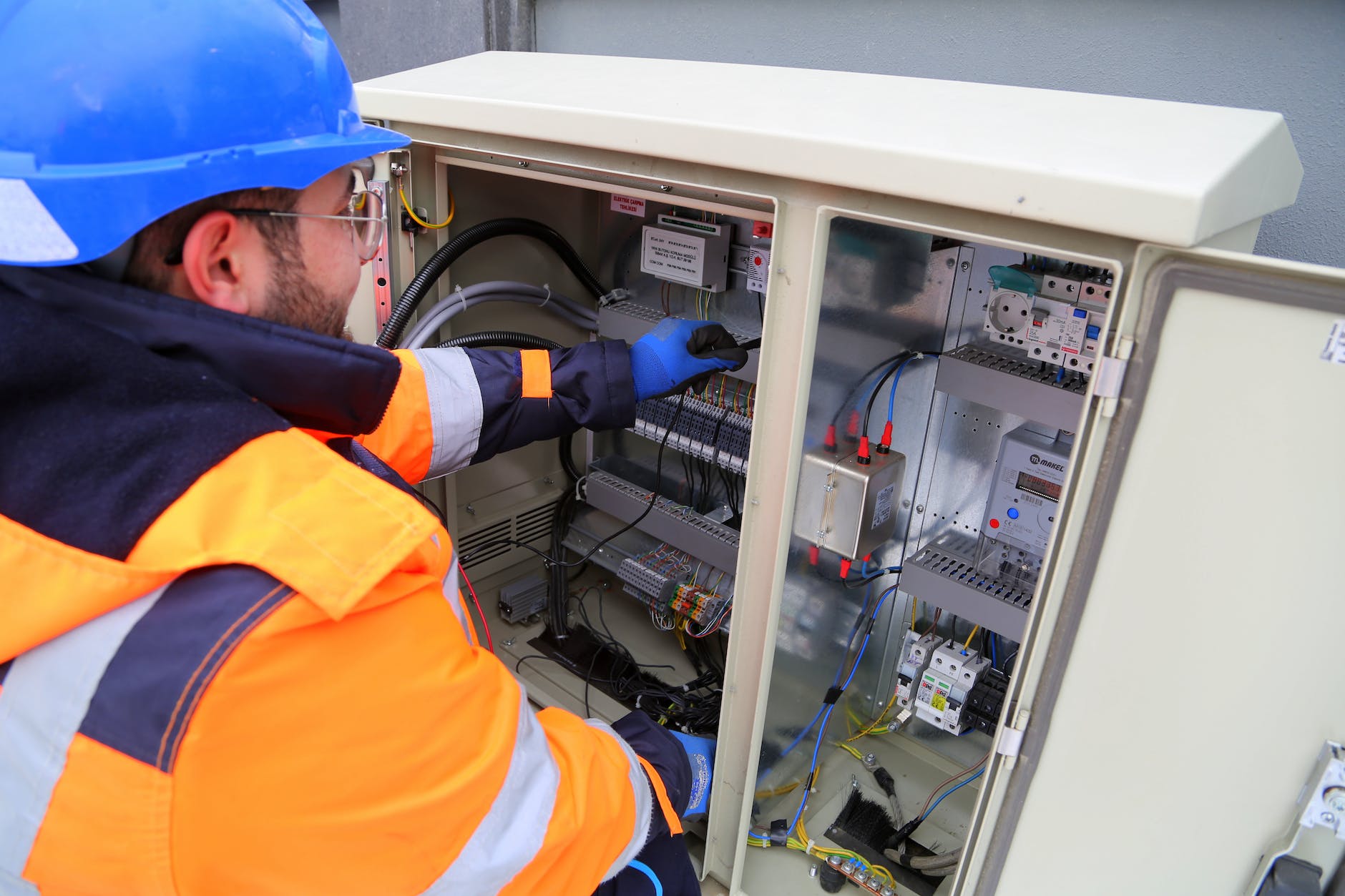
Equipment-specific LOTO: Ensuring Safety and Compliance
Equipment-specific LOTO : In the world of industrial work environments, safety is paramount. One crucial aspect of maintaining safety in these settings is the proper implementation of Lockout-Tagout (LOTO) procedures. LOTO is a systematic method employed to safeguard workers from hazardous energy sources while servicing or maintaining equipment. This article delves into the concept of equipment-specific LOTO, highlighting its significance, process, and benefits.
Introduction: Understanding Equipment-specific LOTO
In industrial settings, various machines and equipment are powered by energy sources that can pose potential risks to workers during maintenance or repair. Equipment-specific Lockout-Tagout (LOTO) is a targeted safety procedure designed to mitigate these risks. By isolating energy sources, implementing lockout devices, and tagging equipment, workers are safeguarded from unexpected energization while performing essential tasks.
The Importance of LOTO in Industrial Safety
LOTO procedures are pivotal in preventing accidents caused by the unexpected release of energy. These accidents can lead to severe injuries, amputations, and even fatalities. The implementation of equipment-specific LOTO not only protects workers’ well-being but also aids companies in complying with regulations and avoiding legal penalties.
The Basics of Equipment-specific LOTO
Identifying Hazardous Energy Sources
Before initiating any maintenance task, it’s crucial to identify all potential energy sources associated with the equipment. These sources might include electrical, mechanical, hydraulic, pneumatic, and thermal energy. By identifying these sources, workers can determine the necessary steps to isolate and control them effectively.
Isolating and Locking Out Equipment
Once the energy sources are identified, the next step involves isolating the equipment from these sources. This is achieved by shutting down the equipment and locking out its energy isolation points using lockout devices. These devices prevent the accidental or unauthorized activation of the equipment.
Implementing Equipment-specific LOTO: Step-by-Step Guide
Step 1: Preparation and Notification
Before starting any maintenance activity, a comprehensive plan should be outlined. All affected personnel must be notified about the impending LOTO procedure. Clear communication ensures that everyone is aware of the ongoing maintenance work.
Step 2: Equipment Shutdown
The equipment must be shut down following the manufacturer’s guidelines. This ensures a safe starting point for the LOTO procedure. If the equipment has multiple energy sources, each one should be deactivated accordingly.
Step 3: Isolating Energy Sources
After shutdown, the hazardous energy sources must be isolated using appropriate methods. This might involve closing valves, disconnecting power sources, or blocking energy transmission points.
Step 4: Applying Lockout Devices
Lockout devices, such as padlocks and hasps, are placed on energy isolation points to prevent their reactivation. These devices serve as a visible indicator that maintenance work is ongoing and that the equipment should not be operated.
Step 5: Verification and Testing
Before any maintenance work begins, a thorough inspection is necessary. Test the equipment’s controls and switches to ensure they are effectively locked out. Only after successful verification should maintenance activities commence.
Advantages of Equipment-specific LOTO
Enhanced Worker Safety
Equipment-specific LOTO minimizes the risk of accidents, protecting workers from unexpected releases of energy. This contributes to a safer work environment and reduces the likelihood of injuries.
Legal Compliance and Avoidance of Penalties
Regulatory authorities mandate LOTO procedures in many industries. Adhering to these regulations not only ensures legal compliance but also helps companies avoid hefty fines and legal repercussions.
Prevention of Accidents and Injuries
By following equipment-specific LOTO protocols, companies can prevent accidents that might lead to injuries or fatalities. This fosters a culture of safety and well-being among employees.
Challenges and Best Practices
Training and Education
Proper training and education are vital for the successful implementation of LOTO procedures. Workers should be well-informed about the risks, procedures, and proper usage of lockout devices.
Maintaining LOTO Procedures
LOTO procedures should be regularly reviewed and updated to accommodate changes in equipment or processes. Periodic assessments ensure that the procedures remain effective and relevant.
Evolution of LOTO Technologies
Advanced Lockout Systems
Modern LOTO systems have evolved to incorporate advanced technologies. Smart lockout devices, remote control systems, and digital protocols enhance the efficiency and convenience of LOTO procedures.
Integration with Digital Systems
Some industries are integrating LOTO procedures with digital management systems. This integration streamlines documentation, verification, and reporting, making the entire process more organized and accessible.
Case Studies: Successful Implementation of Equipment-specific LOTO
Company A: Reducing Downtime and Enhancing Safety
By implementing equipment-specific LOTO, Company A reduced downtime by ensuring smoother maintenance processes. This led to increased productivity and a notable decrease in accidents.
Company B: Streamlining LOTO Procedures with Technology
Company B embraced digital LOTO management, resulting in streamlined procedures and improved compliance tracking. The incorporation of technology simplified the process for both workers and supervisors.
Conclusion
Equipment-specific Lockout-Tagout (LOTO) procedures are a cornerstone of industrial safety. By isolating hazardous energy sources and implementing lockout devices, companies prioritize worker well-being and legal compliance. Embracing evolving technologies and adhering to best practices ensures that LOTO procedures continue to be effective in preventing accidents and injuries.
FAQs
- What is the primary objective of equipment-specific LOTO? The primary objective of equipment-specific LOTO is to protect workers from hazardous energy sources during maintenance by isolating and locking out equipment.
- Are there any industries exempt from LOTO regulations? While regulations might vary, most industries with potentially hazardous energy sources are required to implement LOTO procedures to ensure worker safety.
- How often should LOTO procedures be reviewed and updated? LOTO procedures should be reviewed periodically, especially when equipment or processes change. Regular updates ensure the procedures remain effective and up-to-date.
- What role does employee training play in LOTO implementation? Proper employee training is crucial for LOTO implementation. Workers need to understand the risks, procedures, and proper usage of lockout devices to maintain a safe working environment.
- Can LOTO procedures be applied to non-industrial settings? Yes, LOTO procedures can be adapted to non-industrial settings where hazardous energy sources are present. Implementing LOTO ensures safety during maintenance and servicing activities.