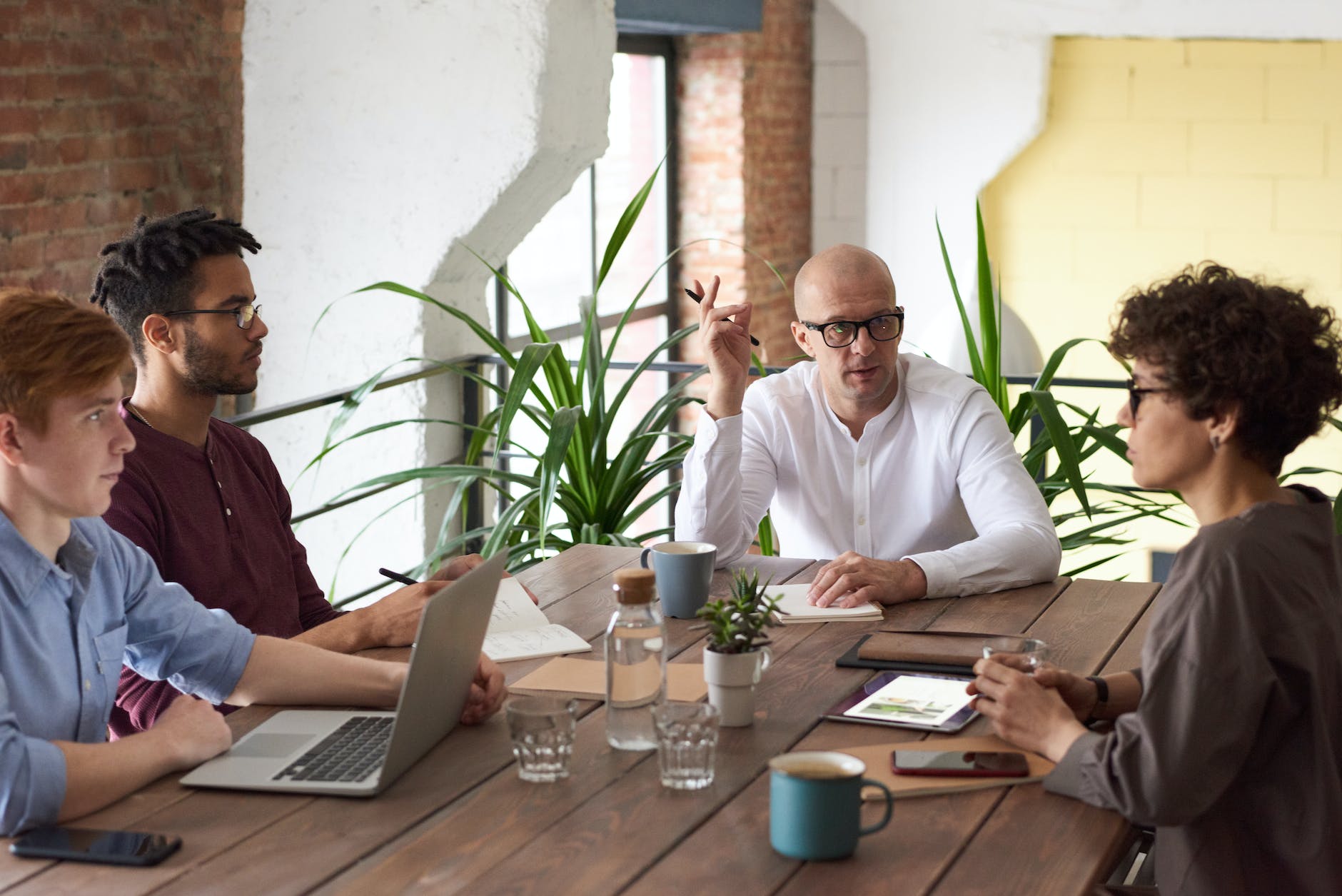
Emergency Planning for Factories
Factories, being bustling hubs of productivity, must prioritize safety. An integral aspect of ensuring a secure work environment involves formulating an efficient emergency plan tailored to factory-specific needs.
Introduction to Emergency Planning for Factories
Importance of Emergency Plans
Safety stands as the paramount concern in any industrial setting. Factories, with their complex machinery and diverse operations, face a myriad of potential risks. An emergency plan serves as the backbone to mitigate these risks efficiently.
Legal Requirements for Factory Emergency Plans
Regulatory bodies mandate factories to have comprehensive emergency plans in place. Compliance isn’t just a legal obligation; it ensures the safeguarding of employees, assets, and the surrounding community.
Elements of an Effective Emergency Plan
Risk Assessment and Identification
The cornerstone of any emergency plan is a thorough assessment of potential hazards. Identifying risks specific to the factory environment enables proactive measures to prevent disasters.
Emergency Response Team Formation
Designating and training a team responsible for emergency response is critical. These individuals should be well-versed in protocols, equipped to handle crises, and capable of guiding others during emergencies.
Communication Protocols
Establishing clear communication channels is pivotal. From alarms and alerts to evacuation procedures, effective communication ensures a swift and organized response in times of crisis.
Training and Drills
Regular training sessions and simulated drills are imperative. Familiarizing employees with emergency procedures cultivates preparedness and minimizes panic during real emergencies.
Key Components of a Factory Emergency Plan
Evacuation Procedures
Clearly defined evacuation routes and assembly points are fundamental. Regular drills validate these routes and ensure everyone knows how to evacuate safely.
Fire Safety Measures
Fire poses a significant risk in factories. Implementing fire safety protocols, including fire extinguisher placement and fire-resistant materials, is indispensable.
First Aid and Medical Facilities
Adequate first aid stations and access to medical facilities are vital components. Prompt medical attention can mitigate the severity of injuries during emergencies.
Equipment Maintenance and Inspection
Regular maintenance and inspection of machinery and safety equipment are non-negotiable. Ensuring everything is in top-notch condition reduces the likelihood of accidents.
Continuity Plans
Planning for business continuity post-emergency is essential. Having strategies to resume operations swiftly minimizes downtime and ensures minimal impact on productivity.
Implementing and Testing the Emergency Plan
Regular Evaluation and Updates
An emergency plan is a dynamic document. Regular evaluation and updates, considering new risks or operational changes, keep the plan effective.
Conducting Mock Drills
Practicing emergency procedures through drills is indispensable. It not only reinforces protocols but also highlights areas needing improvement.
When creating an emergency plan for a factory, consider the following steps:
- Risk Assessment: Identify potential hazards specific to the factory environment, such as machinery malfunctions, chemical spills, fires, or natural disasters.
- Emergency Response Team: Designate and train a team responsible for emergency response. Ensure they understand their roles and have the necessary skills and equipment.
- Emergency Procedures: Develop clear, step-by-step procedures for different types of emergencies. Include evacuation routes, assembly points, and protocols for shutting down machinery or utilities.
- Communication Plan: Establish communication protocols for alerting employees about emergencies. Use alarms, intercoms, or other communication tools to ensure everyone is informed.
- Employee Training: Conduct regular training sessions to educate employees about emergency procedures. Practice drills to familiarize everyone with evacuation routes and safety protocols.
- First Aid and Medical Assistance: Ensure first aid kits are readily available and that designated personnel are trained in first aid. Establish protocols for contacting medical services in case of injuries.
- Fire Safety: Implement fire safety measures such as fire extinguishers, smoke detectors, and sprinkler systems. Conduct fire drills to ensure everyone knows how to respond in case of a fire.
- Evacuation Plan: Create a clear evacuation plan with multiple exit routes. Ensure exits are clearly marked and accessible. Establish a meeting point for employees outside the factory.
- Equipment Maintenance: Regularly inspect and maintain equipment to minimize the risk of malfunctions that could lead to emergencies.
- Review and Update: Periodically review and update the emergency plan to account for changes in the factory layout, new equipment, or updated safety regulations.
Remember, each factory is unique, so tailor the emergency plan to the specific risks and layout of your facility. Regular training, practice drills, and maintaining an open line of communication are key to ensuring the plan's effectiveness in an actual emergency.
Conclusion
Crafting an effective emergency plan for factories is a multifaceted process. It requires meticulous planning, continuous assessment, and a dedicated team effort. Prioritizing safety through comprehensive planning ensures a secure environment for all.
HSE LEGAL Compliance Documents PPT | Download PPT
FAQs
- How often should emergency drills be conducted in a factory setting? Conducting drills at least twice a year is advisable, but the frequency might vary based on specific factory risks and regulations.
- Can a factory emergency plan be standardized across different industries? While certain elements might overlap, each industry has unique risks, making customization crucial for an effective plan.
- Who should be part of the emergency response team in a factory? The team typically includes individuals from various departments, adequately trained to handle emergencies.
- How frequently should emergency plans be updated? Emergency plans should be reviewed at least annually and updated whenever there are operational changes or new risks identified.
- What role does employee training play in emergency preparedness? Employee training ensures everyone understands their roles and procedures during emergencies, enhancing overall preparedness.