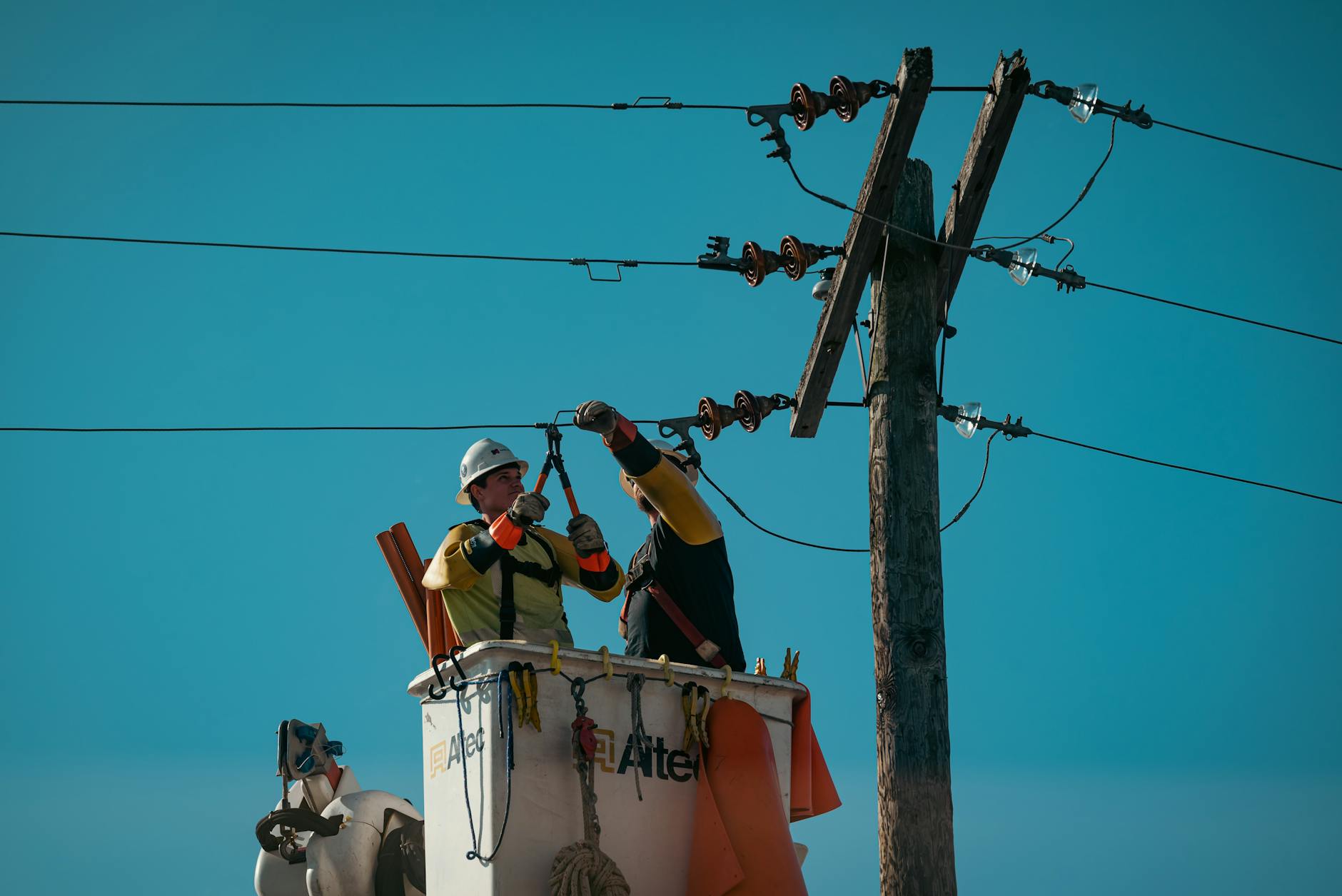
Electrical Safety Rules in Industry
In the fast-paced world of industry, where machinery hums, and technology drives progress, electrical safety is paramount. From large-scale manufacturing plants to small workshops, the risks associated with electricity are ever-present. Therefore, it is imperative to understand and implement strict electrical safety rules to ensure the well-being of workers and the smooth operation of industrial facilities.
Introduction to Electrical Safety
In the industrial setting, the significance of electrical safety cannot be overstated. Every year, numerous accidents occur due to electrical hazards, leading to injuries, fatalities, and costly damages to equipment. Hence, prioritizing electrical safety is not just a legal requirement but also a moral obligation towards workers’ welfare.
Understanding Electrical Hazards
Electricity, while indispensable, poses several hazards in the workplace. These hazards include electric shock, arc flash, and electrocution. Electric shock occurs when the body becomes part of the electrical circuit, resulting in injuries ranging from minor burns to cardiac arrest. Arc flash, on the other hand, is an explosive release of energy caused by a short circuit, capable of causing severe burns and even death. Electrocution refers to death caused by electric shock, highlighting the lethal potential of electrical hazards.
Types of Electrical Hazards
Electric Shock
Electric shock occurs when the body becomes part of the electrical circuit, resulting in injuries ranging from minor burns to cardiac arrest.
Arc Flash
Arc flash is an explosive release of energy caused by a short circuit, capable of causing severe burns and even death.
Electrocution
Electrocution refers to death caused by electric shock, highlighting the lethal potential of electrical hazards.
Essential Electrical Safety Rules
To mitigate the risks associated with electricity, strict adherence to electrical safety rules is imperative.
Proper Training and Qualifications
All personnel working with electrical equipment must receive comprehensive training and possess the necessary qualifications. This training should cover topics such as identifying electrical hazards, proper use of personal protective equipment (PPE), and emergency response procedures.
Personal Protective Equipment (PPE)
The use of appropriate PPE is essential to minimize the risk of electrical injuries. This may include insulated gloves, safety glasses, arc-rated clothing, and voltage-rated tools. PPE serves as a crucial line of defense against electric shock and arc flash incidents.
Equipment Inspection and Maintenance
Regular inspection and maintenance of electrical equipment are vital to ensure its safe operation. Any signs of wear and tear, loose connections, or damaged components should be addressed promptly to prevent potential hazards.
Lockout/Tagout Procedures
Lockout/tagout procedures are designed to control hazardous energy sources during maintenance or servicing activities. By isolating electrical sources and effectively communicating the status of equipment through lockout/tagout tags, the risk of accidental energization is minimized.
Safe Work Practices
Implementing safe work practices, such as de-energizing equipment before maintenance, avoiding overloading circuits, and using insulated tools, can significantly reduce the likelihood of electrical accidents.
Compliance with Regulations and Standards
Compliance with relevant regulations and standards is crucial to ensuring a safe working environment.
OSHA Regulations
The Occupational Safety and Health Administration (OSHA) sets forth regulations pertaining to electrical safety in the workplace. Employers must comply with OSHA standards, which include requirements for electrical installations, wiring methods, and safety practices.
NFPA 70E Standard
The National Fire Protection Association (NFPA) 70E standard provides guidelines for electrical safety in the workplace, focusing on hazard identification, risk assessment, and the implementation of safety measures. Adhering to NFPA 70E helps organizations mitigate electrical risks and safeguard workers’ well-being.
Creating a Culture of Safety
Fostering a culture of safety is essential to promote awareness and accountability among workers.
Importance of Communication
Effective communication regarding electrical hazards, safety procedures, and emergency protocols is key to ensuring that all personnel are well-informed and prepared to mitigate risks.
Regular Safety Audits and Inspections
Conducting regular safety audits and inspections helps identify potential hazards and ensure compliance with safety protocols. By proactively addressing safety concerns, organizations can prevent accidents and promote a safer work environment.
Responding to Electrical Emergencies
Despite preventive measures, electrical emergencies may still occur. Therefore, having robust emergency response plans in place is essential.
Emergency Response Plans
Emergency response plans should outline procedures for responding to electrical incidents, including evacuation protocols, medical assistance procedures, and methods for containing electrical hazards.
First Aid for Electrical Injuries
Providing prompt first aid for electrical injuries can make a crucial difference in outcomes. Training employees in basic first aid techniques for electrical burns, shock, and electrocution can help minimize the severity of injuries and improve recovery chances.
Conclusion
In conclusion, prioritizing electrical safety in the industrial sector is paramount to safeguarding workers’ well-being and preventing costly accidents. By adhering to essential safety rules, complying with regulations and standards, fostering a culture of safety, and being prepared to respond to emergencies, organizations can create a safer work environment and ensure continuity of operations.
Electrical Grounding: Unraveling the Importance and Essential Techniques
Electrical Cord Management: Safeguarding Against Overloading and Tripping Hazards
Electrical Cord Safety: Inspection and Replacement Guidelines
FAQs
1. How often should electrical equipment be inspected?
Regular inspections of electrical equipment should be conducted according to a predetermined schedule, typically based on manufacturer recommendations and industry standards.
2. What is lockout/tagout, and why is it important?
Lockout/tagout is a safety procedure used to isolate energy sources and prevent accidental startup of equipment during maintenance or servicing. It is important to prevent injuries caused by unexpected energization of machinery.
3. What are the consequences of non-compliance with electrical safety regulations?
Non-compliance with electrical safety regulations can lead to serious consequences, including injuries, fatalities, legal penalties, and damage to property and equipment.
4. How can employees contribute to promoting electrical safety in the workplace?
Employees can contribute to promoting electrical safety by following safety procedures, reporting hazards or malfunctions promptly, participating in safety training programs, and maintaining a vigilant attitude towards potential risks.
5. What should employers do in the event of an electrical emergency?
Employers should have clear emergency response plans in place and ensure that employees are trained in emergency procedures. In the event of an electrical emergency, prompt action should be taken to ensure the safety of personnel and minimize the risk of further harm.