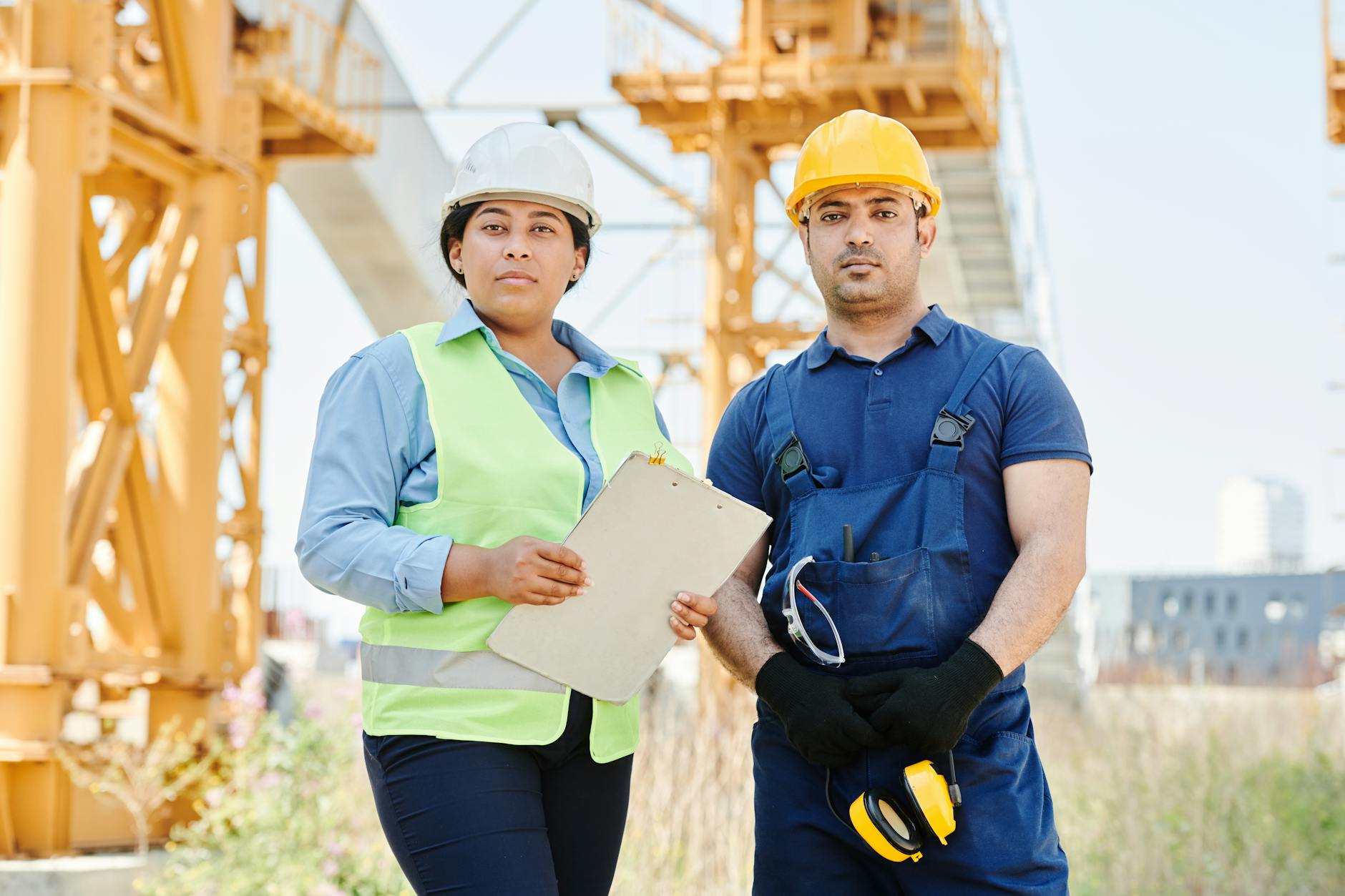
Crane Safety Requirements
Crane operations are integral to construction and industrial projects, lifting heavy materials and performing tasks that are impossible by manual labor alone. However, cranes also pose significant safety risks, both to the operators and the workers on the ground. To minimize these risks and ensure safe operations, specific crane safety requirements must be followed. Here’s a comprehensive look at the essential safety measures for crane operation:
1. Operator Certification and Training
Requirement:
Operators must be certified and undergo proper training before operating cranes. Certification ensures that the operator understands how to safely control the crane, handle various loads, and respond to emergency situations.
Why It’s Important:
Properly trained operators are less likely to make errors that could lead to accidents. Training includes understanding the crane’s limits, load capacities, proper rigging procedures, and emergency protocols.
2. Regular Inspections and Maintenance
Requirement:
Cranes should undergo regular inspections, both pre-operation and scheduled maintenance checks. This includes inspecting critical components like cables, brakes, gears, and the hydraulic system.
Why It’s Important:
Routine maintenance and inspections help identify any wear and tear, structural damage, or faulty systems before they cause malfunctions during operation. This significantly reduces the likelihood of accidents due to mechanical failures.
3. Load Limitations
Requirement:
Cranes should only lift loads within their rated capacity, which must be clearly marked on the crane. Operators need to be aware of these limitations and avoid overloading the crane.
Why It’s Important:
Overloading can cause the crane to become unstable, increasing the risk of tipping or structural failure. Following load capacity guidelines is crucial to maintaining the crane’s stability and safety.
4. Proper Rigging
Requirement:
The load must be securely attached to the crane using the correct rigging methods and equipment. The rigging should include slings, chains, ropes, or hoists that are rated for the weight and type of load.
Why It’s Important:
Improper rigging can lead to dropped loads, which can cause injuries or property damage. Using the right rigging ensures the load is lifted and transported safely without accidents.
5. Crane Setup and Stability
Requirement:
The crane must be set up on a stable, level surface. This includes ensuring the ground is firm enough to support the crane’s weight and preventing it from tipping during operation.
Why It’s Important:
A crane set up on unstable ground may shift, collapse, or tip over, especially when lifting heavy loads or working at high heights. Stabilizing the crane with outriggers or counterweights is essential for safe operations.
6. Weather Considerations
Requirement:
Crane operations should be halted during adverse weather conditions, such as high winds, lightning, or severe rain. Wind speeds, in particular, are crucial to monitor, as they can affect the crane’s stability and control.
Why It’s Important:
High winds can destabilize the crane, causing it to sway or lose control over the load. Strong gusts can also cause the crane to become unbalanced or tip over, leading to accidents.
7. Safe Work Zones
Requirement:
Establish a designated safety zone around the crane’s operation area, where unauthorized personnel are restricted. This zone should be clearly marked and should include the area under the crane’s lifting path.
Why It’s Important:
Keeping personnel out of the danger zone helps reduce the risk of injury from falling loads, swinging arms, or crane malfunctions. Proper signage and barriers are necessary to maintain safety.
8. Clear Communication
Requirement:
Effective communication between the crane operator, ground crew, and other workers on the site is essential. Radios, hand signals, or other communication tools should be used to ensure everyone understands the crane’s movements.
Why It’s Important:
Miscommunication can lead to accidents, especially when the crane operator cannot see the entire work zone. Clear and constant communication helps avoid collisions and other mishaps.
9. Overload Protection
Requirement:
Cranes should be equipped with overload protection devices, such as load moment indicators, which prevent lifting loads beyond the crane’s rated capacity.
Why It’s Important:
Overloading can cause the crane to tip over or fail mechanically. Load moment indicators warn the operator when the crane is reaching unsafe limits, preventing potentially disastrous situations.
10. Anti-Collision Devices
Requirement:
When working in areas with multiple cranes or other equipment, anti-collision devices must be used. These systems detect nearby objects and prevent cranes from colliding with each other or with obstacles.
Why It’s Important:
Accidents can occur when cranes swing into each other or stationary objects. Anti-collision devices help ensure that the crane operates safely in crowded work environments, preventing costly and dangerous crashes.
11. Emergency Shutdown Procedures
Requirement:
Operators must be trained in emergency shutdown procedures, and the crane should be equipped with an emergency stop button or mechanism. In case of a malfunction or unsafe situation, operators need to know how to quickly and safely shut down the crane.
Why It’s Important:
Emergency shutdowns help prevent accidents and minimize damage during an emergency. Quick responses in crisis situations can save lives and reduce injury risks.
12. Lighting and Visibility
Requirement:
Cranes should be equipped with proper lighting to ensure the operator has good visibility, especially during nighttime operations. The work area must also be adequately lit for safety.
Why It’s Important:
Operating a crane without sufficient lighting can lead to poor visibility, increasing the likelihood of accidents, especially when lifting or moving heavy materials. Adequate lighting ensures that the operator can see the crane’s movements and any potential obstacles.
13. Crane Signage and Warnings
Requirement:
Cranes should have visible warning signs, load charts, and other important safety information clearly displayed. This includes load capacity limits, hazard warnings, and maintenance schedules.
Why It’s Important:
Clear signage helps operators and workers understand the crane’s operational limits, identify risks, and stay aware of necessary precautions.
14. Personal Protective Equipment (PPE)
Requirement:
All workers involved in crane operations, including operators and ground crew, must wear appropriate personal protective equipment (PPE). This includes hard hats, gloves, safety boots, high-visibility vests, and hearing protection.
Why It’s Important:
PPE protects workers from injuries that may occur due to falling materials, crane malfunctions, or accidents on-site. Ensuring all personnel are equipped with the proper gear is an essential part of crane safety.
15. Compliance with Local Regulations
Requirement:
Crane operations must comply with local and national safety regulations, such as OSHA standards, ANSI standards, and other relevant guidelines.
Why It’s Important:
Adhering to safety regulations ensures that cranes are operated in accordance with legal requirements and industry best practices, which helps avoid fines, injuries, and project delays.
Conclusion
Crane safety is a vital part of any construction or industrial project. By following these safety requirements — from operator training to regular inspections, load limitations, and proper maintenance — the risk of accidents and injuries can be significantly reduced. Ultimately, maintaining a safe crane operation is not just a legal obligation but a moral one to ensure the safety and well-being of everyone on the job site.
Tower Crane Dismantling Safety Procedure
Tower Crane Hazards and Control Measures
Mobile Equipment Safety: Prioritizing Operator Training and Maintenance Practices
Crane and Hoist Safety: Operator Training and Load Handling