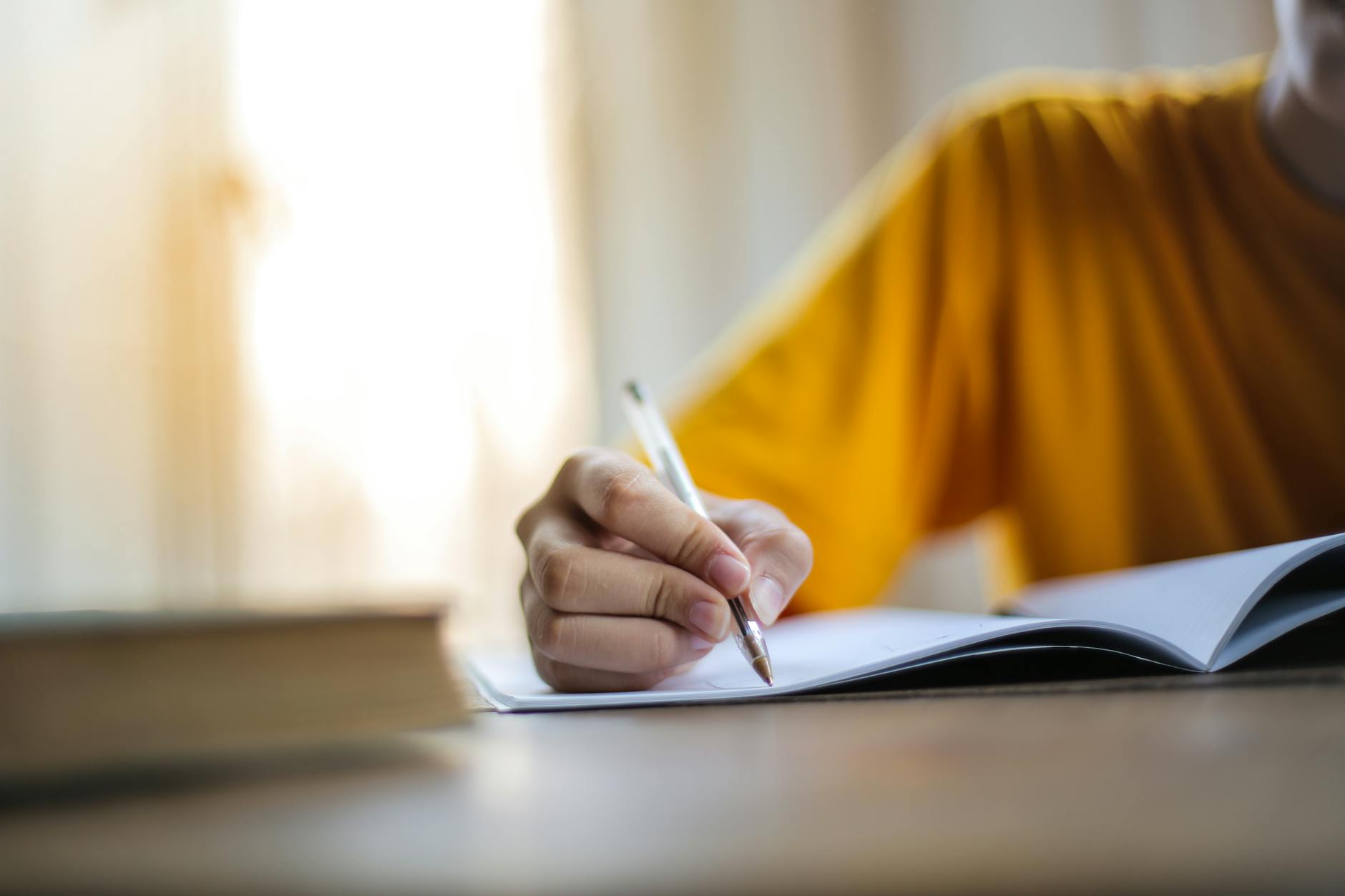
All About Job Safety Analysis (JSA)
Introduction
Workplace safety is a top priority in any industry. One of the most effective ways to ensure a safe working environment is by conducting a Job Safety Analysis (JSA). But what exactly is JSA, and why is it so important? This article will cover everything you need to know about JSA, from its definition and purpose to how to effectively implement it in your workplace.
Understanding Job Safety Analysis (JSA)
Definition and Purpose
A Job Safety Analysis (JSA) is a systematic process that helps identify potential hazards associated with specific job tasks and provides solutions to mitigate those risks. The primary goal of JSA is to reduce workplace accidents and injuries by analyzing each step of a job and implementing preventive measures.
Key Elements of JSA
- Task Identification: Choosing a job to analyze.
- Hazard Recognition: Identifying potential hazards in each step.
- Risk Assessment: Evaluating the severity of hazards.
- Control Measures: Developing ways to eliminate or reduce risks.
Who is Responsible for JSA?
- Safety Officers
- Supervisors and Managers
- Employees Performing the Job
- Health and Safety Committees
Objectives of JSA
The primary objectives of Job Safety Analysis are:
- To identify potential hazards in a job task.
- To determine the safest way to perform the job.
- To ensure compliance with occupational safety regulations.
- To enhance employee awareness of workplace hazards.
- To reduce workplace incidents and injuries.
Steps to Conduct Job Safety Analysis
Step 1: Select the Job to Be Analyzed
Choose a job with a high risk of injury or one that has resulted in previous accidents.
Step 2: Break the Job into Sequential Steps
List each action required to complete the job in order.
Step 3: Identify Potential Hazards
Analyze each step for risks such as falls, exposure to harmful substances, or ergonomic strains.
Step 4: Develop Preventive Measures
Determine ways to control or eliminate the hazards identified.
Step 5: Implement and Review the JSA
Put safety measures into practice and continuously review and update the JSA.
Common Workplace Hazards Identified in JSA
- Physical Hazards: Slips, trips, falls, and machine-related injuries.
- Chemical Hazards: Exposure to toxic substances or fumes.
- Biological Hazards: Risks from bacteria, viruses, and other biohazards.
- Ergonomic Hazards: Poor workstation design leading to strain injuries.
- Psychological Hazards: Stress, fatigue, and workplace violence.
Benefits of Job Safety Analysis
Conducting a JSA provides numerous benefits, including:
- Enhanced Workplace Safety: Helps prevent accidents and injuries by identifying hazards before they occur.
- Regulatory Compliance: Ensures adherence to occupational safety standards such as OSHA regulations.
- Improved Employee Training: Acts as a valuable tool for training new employees and reinforcing safety procedures.
- Increased Productivity: Reduces downtime caused by accidents and creates a more efficient work environment.
- Lower Insurance Costs: Fewer workplace incidents can lead to reduced workers’ compensation claims and lower insurance premiums.
JSA vs. Risk Assessment
While both JSA and risk assessment aim to improve workplace safety, they differ in scope:
- JSA focuses on analyzing individual job tasks and their associated hazards.
- Risk Assessment is a broader evaluation of workplace hazards, covering multiple jobs, processes, and overall safety policies.
Industries That Benefit Most from JSA
- Construction: High-risk tasks like working at heights.
- Manufacturing: Operating heavy machinery.
- Oil and Gas: Handling hazardous materials.
- Healthcare: Preventing exposure to infectious diseases.
- Transportation: Managing road safety risks.
Common Challenges in Implementing JSA
Despite its benefits, organizations may face challenges in implementing JSA effectively, such as:
- Lack of Employee Participation: Encouraging workers to actively participate in JSA discussions is crucial for success.
- Inconsistent Documentation: Regularly updating JSA records ensures accuracy and relevance.
- Time Constraints: Conducting a thorough JSA requires time and effort, which some organizations may struggle to allocate.
- Resistance to Change: Employees and management may resist adopting new safety procedures.
Best Practices for an Effective JSA
- Involve workers in the process.
- Regularly review and update JSA reports.
- Make JSA a part of daily operations.
- Use digital tools to streamline documentation.
Common Mistakes to Avoid in JSA
- Skipping steps in the analysis process.
- Not updating JSAs after changes in the workplace.
- Ignoring input from employees performing the job.
Job Safety Analysis (JSA) for Excavation Work in Construction
Project Name: [Your Project Name]
Location: [Job Site Location]
Date: [Date]
Prepared by: [Name/Designation]
Reviewed by: [Supervisor’s Name]
Job Description:
Excavation work for foundation construction.
Job Steps, Potential Hazards, and Control Measures:
Job Steps | Potential Hazards | Control Measures |
---|---|---|
1. Site Preparation | Uneven ground, trip hazards, underground utilities | Conduct site survey, mark hazards, use barricades and warning signs |
2. Marking and Layout | Struck by moving vehicles, inaccurate markings | Use high-visibility vests, communicate with machinery operators |
3. Excavation Work | Cave-ins, falling loads, exposure to hazardous gases | Use protective trenching methods (shoring, sloping), gas detection tests, PPE (helmets, gloves) |
4. Material Handling | Lifting injuries, falling debris | Use mechanical lifting aids, proper lifting techniques, PPE (safety boots, gloves) |
5. Worker Access and Egress | Slips, trips, falls | Provide ladders or ramps, maintain clear pathways |
6. Backfilling and Compaction | Equipment accidents, dust inhalation | Operate machinery safely, use dust control measures |
7. Cleanup and Site Restoration | Sharp objects, improper waste disposal | Ensure proper disposal of debris, use gloves and safety shoes |
PPE Required:
- Safety helmet
- Safety boots
- High-visibility vest
- Gloves
- Eye protection
- Dust mask (if necessary)
Emergency Procedures:
- Stop work immediately if an unsafe condition arises.
- Report incidents to the supervisor.
- Provide first aid if necessary and call emergency services.
- Evacuate workers if needed.
Personnel Responsibilities:
- Site Supervisor: Ensure compliance with safety protocols.
- Workers: Follow safe work practices and use PPE.
- Safety Officer: Conduct inspections and provide safety guidance.
Approval:
[Supervisor’s Signature]
[Date]
This JSA serves as a guideline to ensure safe excavation operations at the construction site. All workers must review and adhere to these safety measures before commencing work.
Conclusion
Job Safety Analysis (JSA) is a critical tool for preventing workplace accidents and ensuring the safety of employees. By following a structured approach, identifying hazards, and implementing preventive measures, businesses can create a safer working environment for everyone. Regularly updating and integrating JSA into daily operations will further enhance workplace safety and compliance.
Risk Assessment Hierarchy of Control
7 Hierarchy of Controls with Examples
HSE Risk Assessment Techniques
Hazard Identification and Risk Assessment Matrix
5 Hierarchy of Control with Examples
FAQs
1. What is the main purpose of a Job Safety Analysis?
JSA aims to identify potential hazards in job tasks and develop preventive measures to reduce the risk of workplace injuries.
2. How often should a JSA be reviewed?
It should be reviewed regularly, especially when there are changes in job tasks, equipment, or safety regulations.
3. Who is responsible for conducting a JSA?
Supervisors, safety officers, and employees involved in the task should collaboratively conduct JSAs.
4. Can JSA improve workplace safety culture?
Yes, implementing JSA promotes proactive hazard identification and enhances overall safety awareness.
5. What tools can help streamline JSA documentation?
Digital tools like safety management software can help document, track, and update JSA reports efficiently.
Very informative and important notes
Thank You