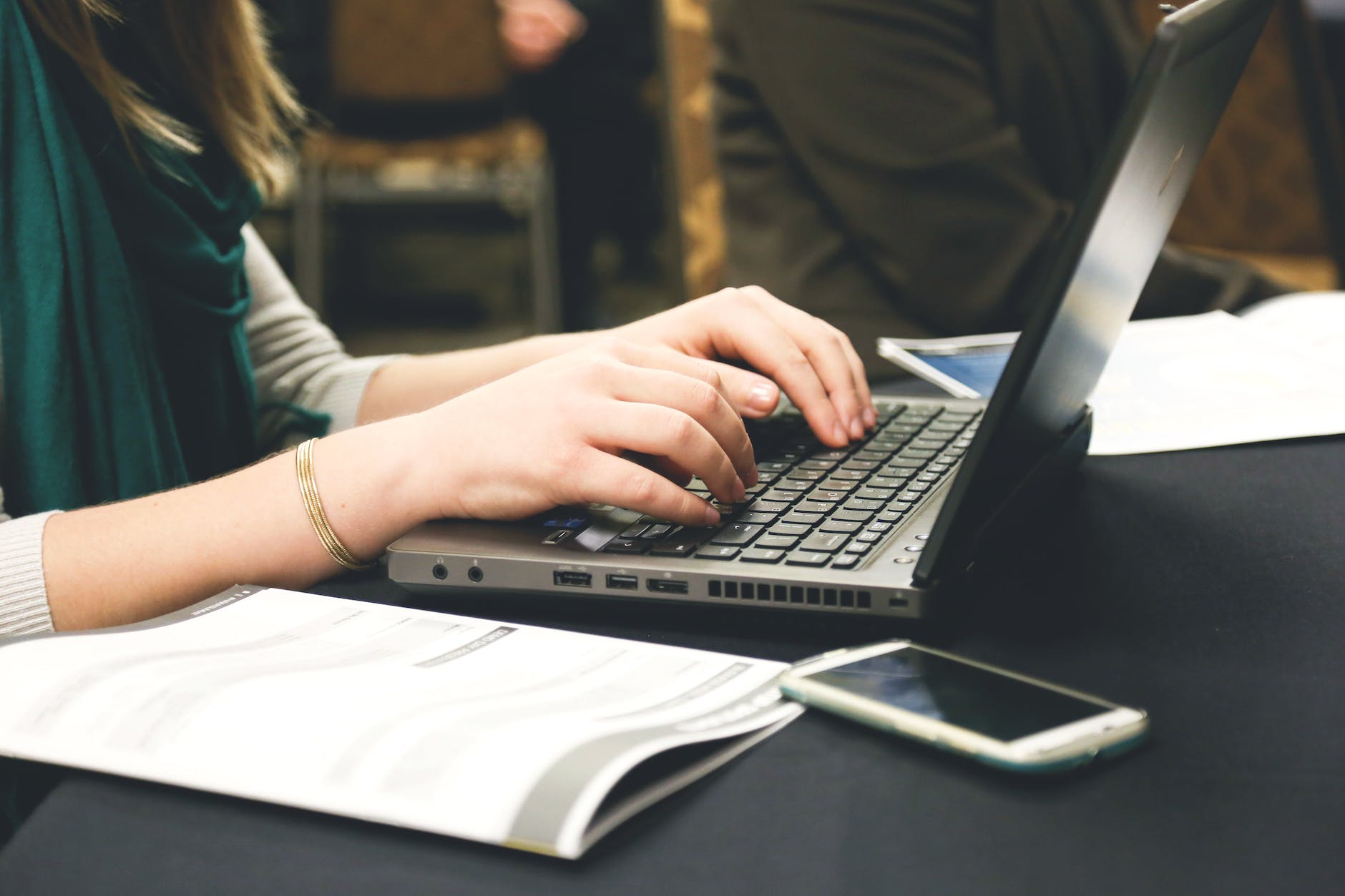
OSHA Vertical Lifeline Requirements
Introduction to OSHA Vertical Lifeline Requirements
When it comes to workplace safety, adhering to the regulations set by the Occupational Safety and Health Administration (OSHA) is paramount. Among various safety measures, the OSHA vertical lifeline requirements stand as a crucial aspect in ensuring the safety of workers who are exposed to fall hazards while working at heights.
Understanding OSHA Standards
Importance of Fall Protection
Falls are a leading cause of fatalities in the workplace, making fall protection a priority for OSHA. The emphasis on protecting workers from fall hazards underscores the significance of complying with OSHA standards, especially concerning vertical lifeline requirements.
Overview of OSHA Vertical Lifeline Requirements
OSHA’s guidelines for vertical lifelines encompass a comprehensive set of regulations that dictate the specifications, installation, inspection, and training necessary for a secure and effective lifeline system.
The Occupational Safety and Health Administration (OSHA) has specific requirements for vertical lifelines used in fall protection systems. Here are some key points:
- Material: Vertical lifelines should be made from synthetic fibers, steel, or other materials that meet OSHA’s strength requirements.
- Strength: Lifelines must be able to support at least 5,000 pounds (22.2 kilonewtons) per worker attached, or meet the criteria specified by OSHA standards.
- Anchorage: Lifelines should be securely attached to an anchorage point that can withstand the required loads.
- Connectors: OSHA requires the use of proper connectors, such as snaphooks or carabiners, which should be self-closing and self-locking to prevent accidental disengagement.
- Inspection and Maintenance: Regular inspection of lifelines for wear, tear, or damage is essential. Damaged lifelines should be immediately removed from service and replaced.
- Training: Proper training in the correct use, inspection, and maintenance of vertical lifelines is crucial for workers using fall protection systems.
Remember, these are general guidelines, and it's important to refer to the specific OSHA regulations (29 CFR 1910.66, 29 CFR 1910.140, or 29 CFR 1926.502) that apply to your particular industry or situation for more detailed and up-to-date information.
Components of a Vertical Lifeline System
Main Elements of a Vertical Lifeline
A typical vertical lifeline system consists of crucial components like the lifeline itself, anchorages, connectors, and harnesses. Each component plays a vital role in ensuring the safety and security of workers at height.
Materials and Construction Specifications
OSHA mandates specific requirements for the materials used and the construction of lifelines, emphasizing durability, strength, and compatibility with various environments and conditions.
Installation and Inspection Guidelines
Proper Installation Procedures
Installing a vertical lifeline demands meticulous attention to detail and adherence to OSHA guidelines. Proper installation ensures the structural integrity and reliability of the lifeline system.
Regular Inspection Protocols
Routine inspections are imperative to identify wear, tear, or damage to any component of the lifeline system. These inspections help prevent accidents by ensuring that the system remains in optimal condition.
Training and Compliance for Vertical Lifelines
Training Requirements for Workers
Workers must undergo comprehensive training to understand the proper usage of vertical lifelines, including how to don harnesses, connect to lifelines, and navigate safely while using this equipment.
Ensuring OSHA Compliance
Compliance with OSHA standards involves not only the installation of lifelines but also keeping records of inspections, training sessions, and any modifications made to the lifeline system.
Common Challenges and Solutions
Addressing Common Issues
Challenges such as improper installation, inadequate training, or neglecting inspections can compromise the effectiveness of vertical lifeline systems. Identifying and rectifying these issues is critical.
Best Practices for Resolving Challenges
Implementing best practices, such as regular training sessions, thorough inspections, and prompt repairs or replacements, can mitigate potential challenges and ensure the longevity of the lifeline system.
Advantages of Complying with OSHA Vertical Lifeline Requirements
Safety Benefits
Adhering to OSHA vertical lifeline requirements significantly reduces the risk of falls, thereby safeguarding the well-being and lives of workers.
Legal and Financial Advantages
Compliance with OSHA standards not only prevents costly penalties but also fosters a positive work environment, promoting productivity and employee morale.
Conclusion
OSHA vertical lifeline requirements are instrumental in safeguarding workers and minimizing fall-related risks. Prioritizing compliance and adopting best practices not only ensures safety but also contributes to a conducive and secure work environment.
Fall Protection Plan Requirements
Work at Height Toolbox Talk Meeting
How to Make JSA for Work at Height Activity
How to Make HIRA on Work At Height?
FAQs
- Are vertical lifelines mandatory for all industries? Vertical lifelines might not be mandatory for all industries, but OSHA mandates their use in workplaces where fall hazards exist.
- How often should vertical lifeline inspections be conducted? OSHA recommends regular inspections, typically before each use, and periodic detailed inspections at least annually.
- Can any material be used for constructing lifelines? Lifelines must meet OSHA specifications for strength, durability, and compatibility with the work environment; hence, not all materials are suitable.
- What happens if a workplace fails to comply with OSHA lifeline requirements? Non-compliance can lead to hefty fines, legal implications, and, more importantly, increased risk of accidents and injuries to workers.
- Do workers need specific certifications to use vertical lifelines? While certifications might not be mandatory, workers should undergo comprehensive training to ensure proper usage and safety.