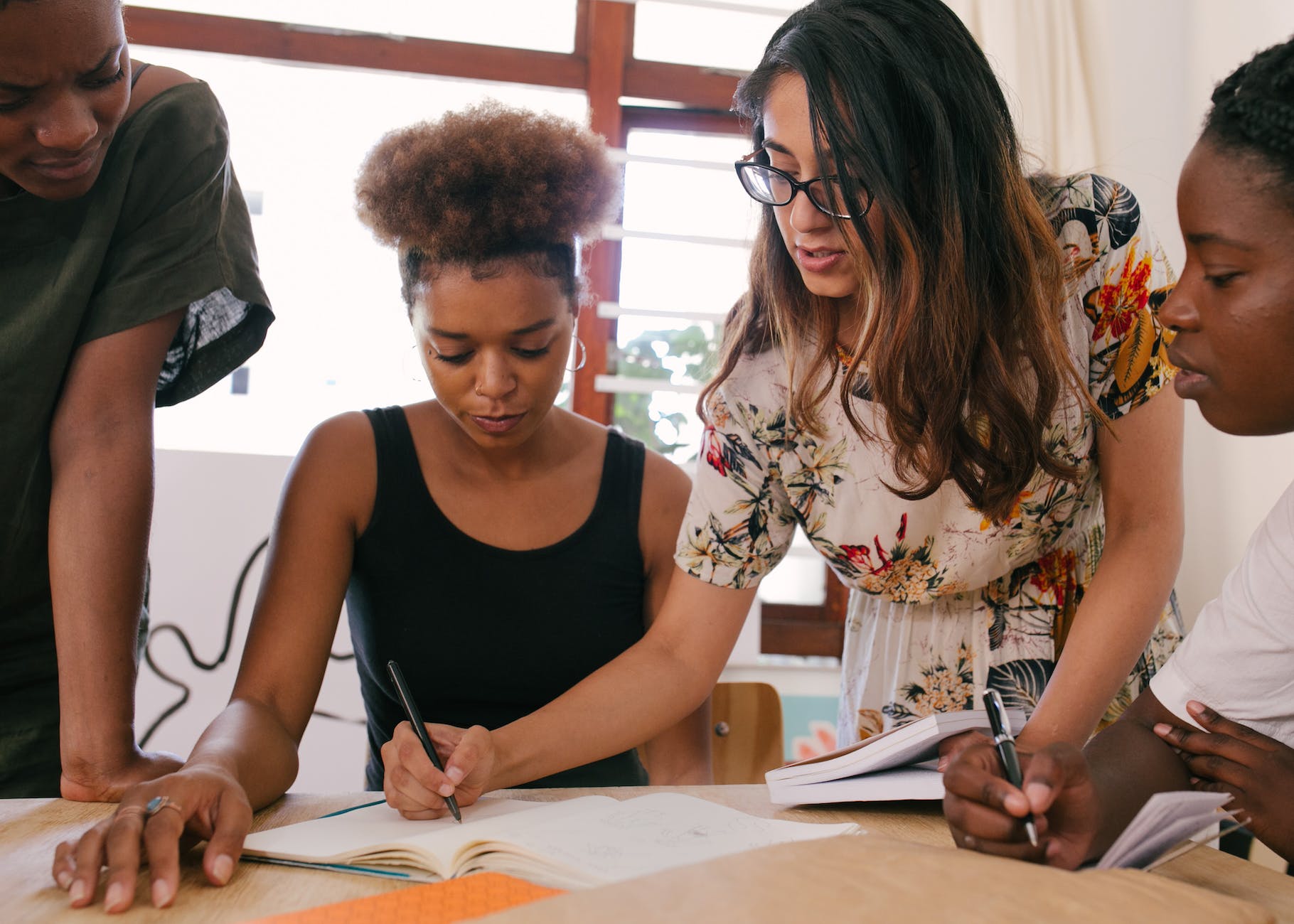
HAZOP Analysis
Industries that prioritize safety and efficiency often employ meticulous methods to evaluate potential risks. One such integral process is Hazard and Operability (HAZOP) analysis. This technique has become indispensable across various sectors, ensuring proactive identification and mitigation of hazards before they escalate into critical incidents.
Introduction to HAZOP Analysis
What is HAZOP?
HAZOP, an acronym for Hazard and Operability, is a structured and systematic approach used to identify potential hazards and operability issues within industrial processes. This analysis method aims to foresee deviations from the design intent that might lead to undesirable outcomes.
Purpose of HAZOP Analysis
The primary goal of HAZOP analysis is to systematically examine a system or process to identify potential deviations that may result in hazards or operational problems.
HAZOP (Hazard and Operability Study) analysis is a systematic method used in industries like chemical processing, oil refining, and other complex systems to identify potential hazards, risks, and operability issues.
During a HAZOP analysis, a team examines different elements of a system or process to identify deviations from the intended operations. This involves looking at various parameters like pressure, temperature, flow rate, and more to brainstorm potential deviations that could lead to hazards or operational problems.
The team uses guide words (such as 'no,' 'more,' 'less,' 'reverse,' etc.) to systematically explore how deviations in these parameters could occur. For each deviation, the team evaluates its potential consequences and determines appropriate actions or safeguards to mitigate the risks.
Ultimately, the goal of a HAZOP analysis is to proactively identify and address potential risks and operational issues to enhance safety, reliability, and efficiency within a system or process.
History and Evolution of HAZOP Analysis
Understanding the roots of HAZOP unveils its journey from conception to its current pivotal role in industrial safety.
Origins of HAZOP
HAZOP analysis was pioneered in the 1960s by Trevor Kletz, an eminent chemical engineer. It emerged as a response to the need for a more comprehensive and systematic approach to risk management.
Evolution in Industry Practices
Over the decades, HAZOP has evolved significantly, integrating technological advancements and diverse industry needs. This evolution has made it more adaptable and efficient in different operational settings.
Key Components of HAZOP Analysis
Nodes in HAZOP
HAZOP primarily focuses on identifying nodes within a system—specific points or elements susceptible to deviations from the intended design.
Parameters Considered
Various parameters, including temperature, pressure, flow rate, and human factors, are meticulously evaluated during HAZOP to comprehend potential deviations.
Methodology of Conducting HAZOP
Steps Involved
The process involves systematic steps, including selecting the team, defining the system, identifying deviations, and evaluating consequences, enabling a thorough analysis.
Tools Utilized
HAZOP analysis employs various tools like guidewords, deviation scenarios, and cause-consequence matrices, aiding in a comprehensive assessment.
Benefits of Implementing HAZOP
Safety Enhancement
The foremost advantage lies in enhancing safety measures by proactively identifying and mitigating potential hazards, preventing accidents.
Risk Mitigation
HAZOP aids in minimizing risks and operational disruptions, ensuring smoother industrial operations and reduced financial liabilities.
Challenges in Implementing HAZOP
Overcoming Barriers
Despite its effectiveness, HAZOP implementation faces challenges related to team dynamics, resource allocation, and time constraints, necessitating strategies to overcome these hurdles.
Addressing Complexity
In complex systems, conducting HAZOP can be intricate, demanding expertise and advanced analytical tools to ensure thorough assessments.
HAZOP in Various Industries
Applications in Oil & Gas
The oil and gas sector extensively employs HAZOP to assess risks in refining, drilling, and transportation, ensuring safety across the value chain.
HAZOP in Chemical Engineering
In chemical engineering, HAZOP is pivotal in identifying potential hazards in processes involving hazardous materials, preventing accidents and environmental damage.
Conclusion
HAZOP analysis stands as a stalwart in ensuring industrial safety and operational efficiency. Its systematic approach in identifying and mitigating risks has been instrumental across diverse sectors, safeguarding industries and preventing catastrophic incidents.
OSHA Hazard Identification Requirements
OSHA Hazard Identification Training Tool
Hazard Identification Methods in the Workplace
FAQs
1. What industries benefit from HAZOP analysis?
HAZOP analysis is beneficial across various sectors like oil & gas, chemical engineering, pharmaceuticals, and manufacturing.
2. How often should HAZOP analysis be conducted?
The frequency of HAZOP analysis depends on the complexity of the system/process but is usually conducted periodically or during significant modifications.
3. Can HAZOP prevent all accidents?
While HAZOP significantly reduces risks, it cannot guarantee the prevention of all accidents. It’s a proactive measure to minimize potential hazards.
4. Who typically conducts HAZOP analysis?
A multidisciplinary team consisting of engineers, safety professionals, and process experts conducts HAZOP analysis.
5. Is HAZOP a legal requirement in industries?
In many industries, HAZOP analysis is a regulatory and legal requirement to ensure compliance with safety standards and prevent accidents.