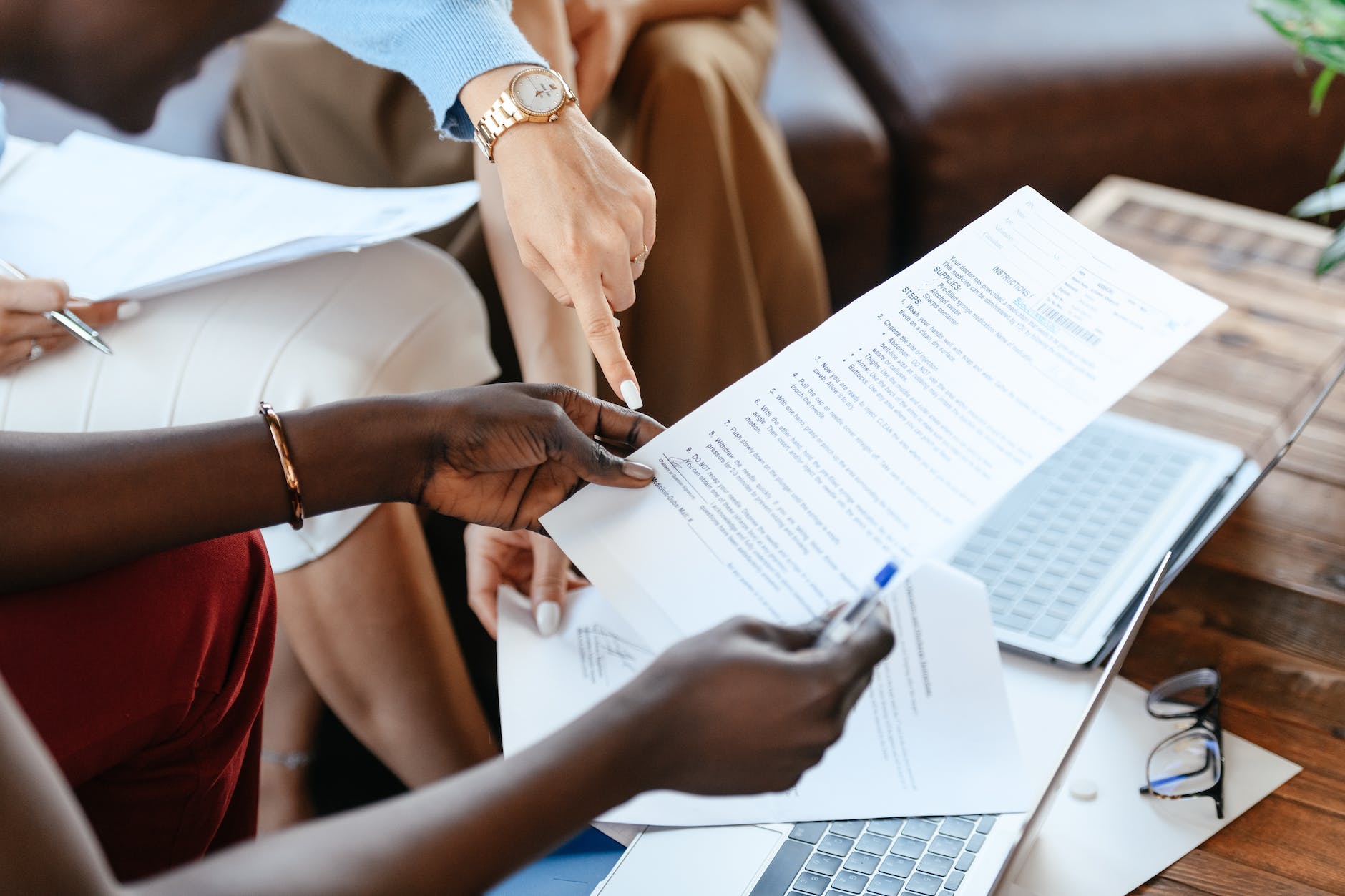
HAZOP Steps
Introduction
When it comes to ensuring safety and preventing hazards in industries, HAZOP (Hazard and Operability Study) plays a pivotal role. Understanding the steps involved in HAZOP is crucial for mitigating risks effectively.
Understanding HAZOP
Process Overview
HAZOP is a systematic method used to identify potential hazards and operability issues in industrial processes.
Importance of HAZOP
Benefits
Discover the significance of conducting HAZOP studies and how they contribute to safety and efficiency in industries.
HAZOP Steps
Understanding the step-by-step process involved in HAZOP is essential for its successful execution.
Preparation
Before initiating the study, adequate preparation and planning are necessary to streamline the process.
Team Formation
Assembling a multidisciplinary team is key to gaining diverse perspectives and expertise in analyzing potential hazards.
Guidewords Selection
Selecting appropriate guidewords helps in systematically exploring deviations from the norm in the process.
Deviation Identification
Identifying deviations from intended operations forms the core of the HAZOP study.
Consequence Analysis
Assessing the potential consequences of identified deviations aids in understanding their impact on safety and operations.
Action Planning
Developing actionable strategies to mitigate identified risks and enhance process safety is imperative.
Hazard and Operability Study (HAZOP) is a structured method used to identify potential hazards and operability issues in a process plant, system, or operation. The HAZOP process typically involves the following steps:
- Selecting the Study Team: Assemble a team of experts representing various disciplines such as engineering, operations, safety, and maintenance.
- Defining the Scope: Clearly define the boundaries and objectives of the study, including the system or process to be analyzed.
- Identifying Nodes: Break down the system or process into smaller sections or nodes that can be systematically reviewed.
- Selecting Guide Words: Guide words (such as ‘no,’ ‘more,’ ‘less,’ ‘reverse,’ etc.) are applied to each node to prompt the team to brainstorm deviations from the intended operating conditions.
- Brainstorming and Analysis: For each guide word applied to a node, the team systematically considers potential deviations, their causes, and the potential consequences.
- Recording Deviations: Document all identified deviations, their potential causes, and consequences. This documentation is crucial for further analysis and mitigation.
- Risk Assessment: Evaluate the identified deviations to assess their potential severity, likelihood, and risk levels.
- Developing Recommendations: Propose practical recommendations to mitigate or eliminate identified hazards and improve operability. These recommendations should be feasible and effective.
- Report and Follow-Up: Compile the findings and recommendations into a comprehensive report. Ensure that follow-up actions are assigned to responsible individuals or teams to address the identified issues.
- Review and Update: Periodically review and update the HAZOP study to incorporate changes in the system, process, or regulations to maintain safety and operability.
These steps help systematically analyze a system or process to identify potential hazards and operational issues, enabling the implementation of measures to enhance safety and efficiency.
Tips for Effective HAZOP
Collaboration
Encouraging collaboration among team members fosters comprehensive hazard identification and analysis.
Clear Communication
Effective communication ensures shared understanding and facilitates smoother HAZOP sessions.
Documentation
Thorough documentation of findings and recommendations is crucial for future reference and implementation.
Conclusion
In conclusion, mastering the HAZOP steps is fundamental to proactively addressing potential hazards and ensuring operational safety in industrial settings.
OSHA Hazard Identification Requirements
OSHA Hazard Identification Training Tool
Hazard Identification Methods in the Workplace
FAQs
HAZOP Frequency
Q: How often should HAZOP studies be conducted in industries? A: The frequency varies based on industry standards and the complexity of processes, typically ranging from every few years to annually.
Industries Using HAZOP
Q: Which industries commonly utilize HAZOP studies? A: HAZOP finds application across diverse sectors such as chemical, pharmaceutical, oil & gas, and manufacturing.
HAZOP vs. Other Methods
Q: How does HAZOP differ from other hazard identification techniques? A: Unlike some methods that focus on specific aspects, HAZOP is comprehensive, analyzing deviations comprehensively in processes.
Challenges of HAZOP
Q: What are the main challenges faced during HAZOP studies? A: Challenges include ensuring thoroughness, managing diverse inputs, and implementing identified recommendations.
Safety Measures
Q: What safety measures result from a successful HAZOP study? A: Implementing HAZOP recommendations enhances safety protocols, reducing the likelihood of accidents and ensuring a safer working environment.