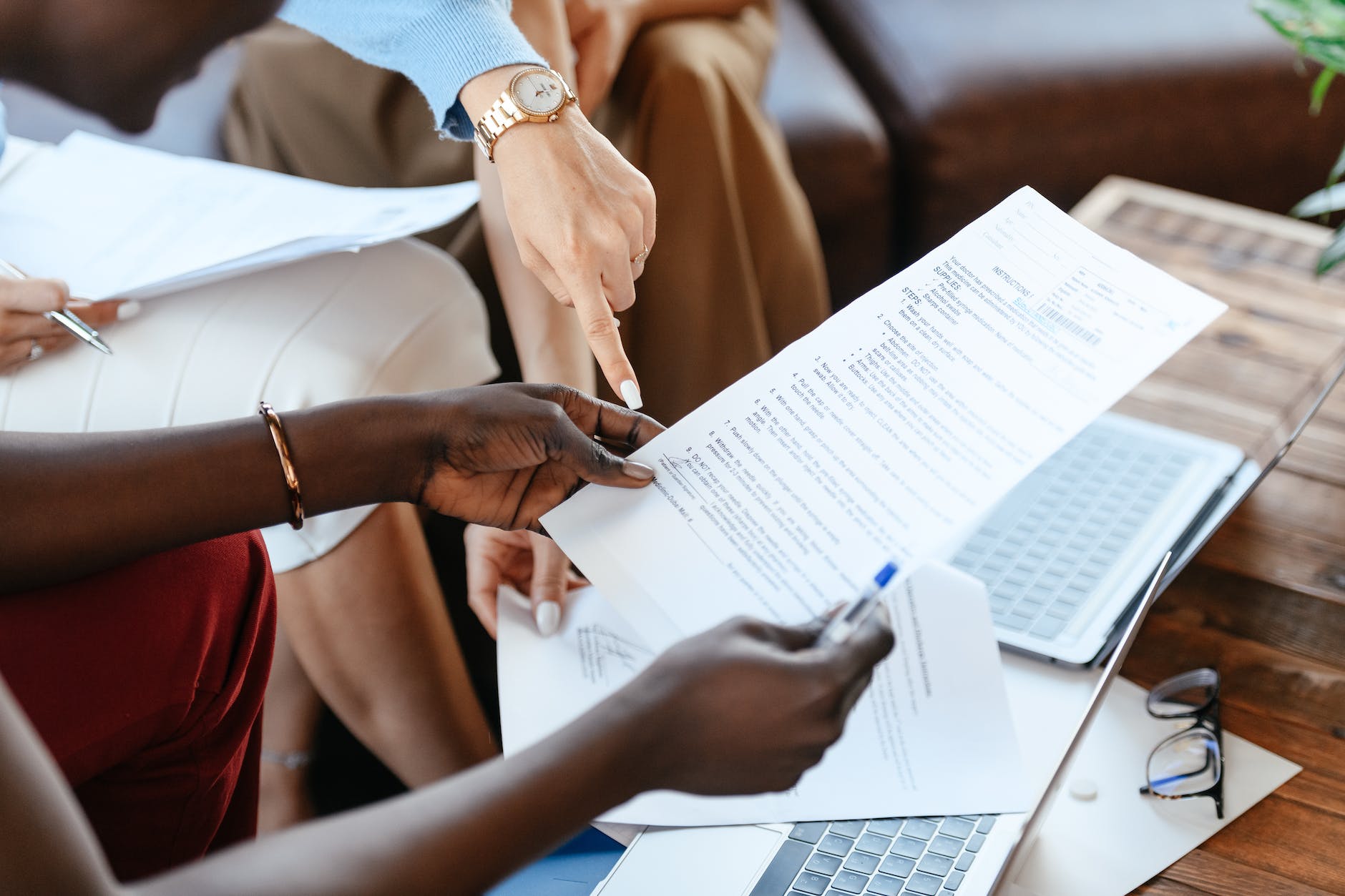
Job Hazard Analysis and Six Sigma: Enhancing Workplace Safety and Efficiency
Introduction
Job Hazard Analysis and Six Sigma: In the modern business landscape, ensuring both employee safety and operational efficiency is paramount. Job hazard analysis (JHA) and Six Sigma are two crucial methodologies that, when combined, can significantly enhance workplace safety and efficiency. This article delves into the principles and practices of JHA and Six Sigma, explaining how their synergy can lead to a safer, more productive work environment.
The Significance of Job Hazard Analysis (JHA)
Understanding Job Hazard Analysis
JHA, or Job Safety Analysis (JSA), is a proactive approach to identifying and mitigating workplace hazards. It involves a systematic evaluation of job tasks to pinpoint potential dangers, thereby allowing organizations to take preventive measures.
Benefits of JHA
- Improved Safety: By identifying hazards and implementing preventive measures, JHA reduces the risk of accidents and injuries.
- Regulatory Compliance: Many regulatory bodies mandate JHA as a part of safety protocols.
- Employee Involvement: JHA encourages employees to actively participate in maintaining a safe work environment.
The Power of Six Sigma
What is Six Sigma?
Six Sigma is a data-driven approach to process improvement that aims to reduce defects and variations in a process. It relies on the DMAIC (Define, Measure, Analyze, Improve, Control) methodology to optimize operations.
Benefits of Six Sigma
- Enhanced Efficiency: Six Sigma helps eliminate process inefficiencies, leading to cost savings and improved productivity.
- Customer Satisfaction: Improved processes result in better products and services, satisfying customers.
- Data-Driven Decision-Making: Six Sigma’s reliance on data ensures informed and effective decision-making.
The Synergy: JHA and Six Sigma
By integrating JHA and Six Sigma, organizations can create a powerful safety and efficiency framework. Here’s how they complement each other:
Identification of Hazards
JHA identifies workplace hazards, which is crucial for initiating Six Sigma projects aimed at improving safety and efficiency.
Data-Driven Safety
Six Sigma uses data to pinpoint process weaknesses, leading to data-backed decisions on safety enhancements.
Continuous Improvement
Both JHA and Six Sigma advocate for continuous improvement, ensuring that workplace safety and efficiency remain priorities.
Employee Involvement
JHA fosters employee involvement in identifying hazards, which can be extended to Six Sigma projects, creating a culture of participation.
Implementing JHA and Six Sigma
Steps to Implement JHA
- Select the Job: Identify the specific job or process that needs a hazard analysis.
- Break Down the Job: Divide the job into its fundamental steps.
- Identify Hazards: Determine potential hazards in each step.
- Develop Preventive Measures: Create strategies to eliminate or mitigate these hazards.
- Review and Communicate: Ensure that employees understand the safety measures and provide necessary training.
Steps to Implement Six Sigma
- Define: Clearly state the problem or goal.
- Measure: Collect relevant data to quantify the problem.
- Analyze: Investigate the data to identify the root causes.
- Improve: Implement solutions to address the root causes.
- Control: Establish mechanisms to maintain the improvements over time.
Case Studies
To better understand the practical application of JHA and Six Sigma, let’s explore a couple of real-world examples:
Case Study 1: Manufacturing Industry
In a manufacturing plant, combining JHA with Six Sigma led to a significant reduction in accidents and defects. By analyzing work processes and eliminating potential hazards, the organization increased safety while improving product quality.
Case Study 2: Healthcare Sector
A hospital integrated JHA into its Six Sigma initiatives. The result was a safer and more efficient patient care system. Identifying potential hazards in medical procedures improved patient safety, while process optimization reduced wait times and resource wastage.
Conclusion
In today’s competitive business world, workplace safety and operational efficiency are non-negotiable. Job Hazard Analysis (JHA) and Six Sigma offer effective tools to achieve these goals. By implementing JHA to identify hazards and Six Sigma to improve processes, organizations can create a safer and more productive work environment.
Hazard Analysis and Critical Control Point (HACCP)
How to Make JSA for Electrical Activity
How To Make JSA for Excavation Activity
How To Make JSA for Confined Space Activity
FAQs
- What is the primary goal of Six Sigma? Six Sigma aims to reduce defects and variations in processes, leading to enhanced efficiency and quality.
- How does JHA contribute to employee involvement? JHA encourages employees to actively participate in identifying workplace hazards, fostering a culture of safety.
- Can small businesses benefit from JHA and Six Sigma? Yes, small businesses can adapt these methodologies to enhance safety and efficiency on a smaller scale.
- Are there any industries where JHA and Six Sigma are not applicable? JHA and Six Sigma principles can be adapted to suit various industries, making them versatile tools for improvement.
- How long does it typically take to see significant improvements through JHA and Six Sigma? The timeline for improvements varies depending on the organization, but positive results are usually noticeable within a few months of implementation.
By integrating Job Hazard Analysis (JHA) and Six Sigma, organizations can create a safety-first culture while enhancing operational efficiency. This dynamic duo empowers businesses to thrive in a world that demands both safety and productivity.