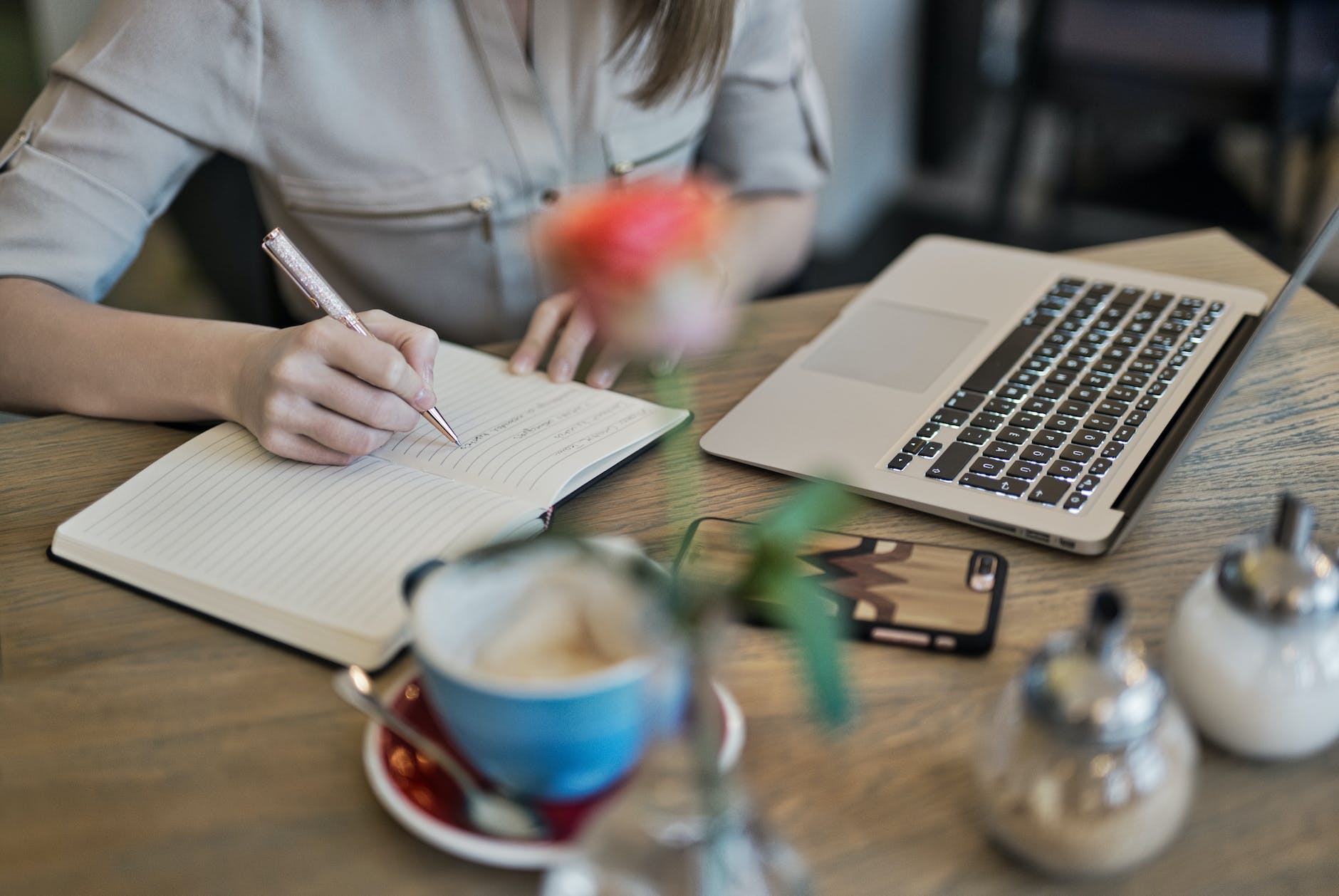
OSHA Standards: A Guide to Health and Safety Compliance
OSHA Standards : In today’s rapidly evolving work environment, ensuring the health and safety of employees is paramount. The Occupational Safety and Health Administration (OSHA) plays a pivotal role in setting standards and guidelines that organizations must follow to maintain a safe workplace. In this comprehensive guide, we will delve into OSHA standards, their significance, and how your business can comply with them.
Understanding OSHA
1.1 What is OSHA?
OSHA, or the Occupational Safety and Health Administration, is a federal agency established to ensure safe and healthy working conditions for American workers. It was created under the Occupational Safety and Health Act of 1970, signed into law by President Richard Nixon. OSHA’s primary goal is to set and enforce standards that protect employees from workplace hazards.
1.2 OSHA’s Mission and Goals
The mission of OSHA is to “assure safe and healthy working conditions for working men and women by setting and enforcing standards and by providing training, outreach, education, and assistance.” OSHA strives to fulfill this mission through various means, including inspections, consultations, and outreach programs.
1.3 The Importance of OSHA Standards
OSHA standards are crucial because they help prevent workplace accidents, injuries, and illnesses. They provide guidelines that employers must follow to maintain a safe working environment. Compliance with OSHA standards not only protects employees but also benefits businesses by reducing the risk of lawsuits, fines, and reputational damage.
OSHA Standards Explained
2.1 General Industry Standards
OSHA’s general industry standards cover a wide range of workplace safety topics, including hazard communication, personal protective equipment, and machine guarding. These standards apply to most industries and serve as a foundation for workplace safety.
2.2 Construction Standards
Construction sites pose unique risks, and OSHA has established specific standards for this industry. These standards address issues such as fall protection, scaffolding safety, and excavation safety to protect construction workers.
2.3 Maritime Standards
Maritime workers face distinct hazards, and OSHA has developed standards tailored to their needs. These standards encompass shipyard employment, marine terminals, and longshoring, ensuring the safety of workers in maritime industries.
2.4 Agriculture Standards
Agriculture presents its own set of challenges in terms of workplace safety. OSHA’s agriculture standards cover topics like grain handling, pesticide safety, and farm equipment safety, safeguarding those who work in this vital sector.
Stay tuned for the continuation of this article, where we’ll explore the benefits of compliance with OSHA standards and delve deeper into the steps required for achieving OSHA compliance.
Benefits of Compliance
3.1 Employee Well-being
Complying with OSHA standards ensures that your employees have a safe and healthy workplace. This not only reduces the risk of accidents but also promotes employee morale and productivity. When workers feel secure in their environment, they are more engaged and motivated to perform their best.
3.2 Legal and Financial Benefits
Maintaining OSHA compliance can save your business from legal troubles and financial burdens. Non-compliance can result in hefty fines, legal actions, and damaged reputation. By adhering to OSHA standards, you demonstrate your commitment to safety and avoid costly consequences.
3.3 Reputation Enhancement
A reputation for safety can be a significant asset in attracting customers and talent. Businesses known for prioritizing employee well-being and complying with OSHA standards often enjoy a competitive advantage. A strong safety culture can be a selling point for both clients and prospective employees.
Compliance Requirements
4.1 Identifying Applicable Standards
To achieve OSHA compliance, businesses must identify which OSHA standards apply to their industry and operations. This can be a complex task, as there are numerous standards, each with its own set of requirements. Seeking expert guidance or using OSHA’s consultation services can simplify this process.
4.2 Developing a Safety Program
Creating a comprehensive safety program is essential for compliance. This program should outline safety policies, procedures, and responsibilities. It should also include measures for hazard identification, prevention, and response. Regular safety training is a critical component of this program.
4.3 Employee Training
Ensuring that employees are well-trained in safety practices is a fundamental aspect of OSHA compliance. Training should be ongoing and cover topics relevant to the workplace. This empowers employees to identify and address potential hazards.
4.4 Record Keeping
OSHA requires businesses to maintain records of workplace injuries and illnesses. Accurate record-keeping helps track safety trends, assess the effectiveness of safety measures, and demonstrate compliance during inspections.
Common OSHA Violations
5.1 Falls and Trips
Falls and trips are among the most common workplace accidents. OSHA standards related to fall protection and walking-working surfaces aim to prevent these incidents. Proper use of guardrails, handrails, and personal protective equipment is crucial.
5.2 Hazardous Chemicals
Many industries involve the use of hazardous chemicals. OSHA’s Hazard Communication Standard (HCS) mandates proper labeling, training, and documentation to protect workers from chemical hazards.
5.3 Machinery Safety
Working with machinery poses inherent risks. OSHA standards require machinery guarding, lockout/tagout procedures, and employee training to minimize the risk of injuries.
5.4 Electrical Hazards
Electricity can be deadly if not handled safely. OSHA standards for electrical safety cover wiring, equipment, and safe work practices to prevent electrical accidents.
Continue reading to discover the steps your organization can take to achieve OSHA compliance and the resources available to assist you in this journey.
Steps to Achieve OSHA Compliance
6.1 Conducting Safety Audits
Regular safety audits are essential to identify potential hazards and compliance gaps. These audits involve thorough inspections of the workplace, equipment, and safety procedures. Addressing issues promptly is crucial to maintaining a safe environment.
6.2 Addressing Violations
If OSHA violations are identified during an audit or inspection, prompt corrective action is necessary. This may include fixing hazards, providing additional training, and updating safety policies. Timely resolution demonstrates a commitment to compliance.
6.3 Continuous Improvement
Achieving and maintaining OSHA compliance is an ongoing process. Businesses should continuously review and enhance their safety programs to adapt to evolving risks and regulations. Employee feedback and involvement can be valuable in this regard.
Resources and Assistance
7.1 OSHA Consultation Services
OSHA offers free consultation services to help businesses identify hazards, improve safety programs, and achieve compliance. These services are confidential and can be a valuable resource for small businesses.
7.2 Training Programs
OSHA provides training programs and materials to educate employers and employees on safety best practices. These programs cover a wide range of industries and topics, ensuring that businesses have access to relevant training.
7.3 Whistleblower Protections
Employees who report safety concerns or violations are protected by OSHA’s whistleblower provisions. Encouraging employees to report hazards and addressing their concerns promptly fosters a culture of safety.
International Perspectives on Safety Standards
8.1 Comparing OSHA to International Agencies
While OSHA sets standards for the United States, other countries have their own occupational safety agencies. Understanding international safety standards can be valuable for businesses with global operations.
8.2 Global Health and Safety Trends
Monitoring global health and safety trends can help businesses stay ahead of emerging risks. Innovations in safety technology and practices may influence future OSHA standards.
Future Trends in OSHA Standards
9.1 Technological Advancements
Advancements in technology, such as the use of wearable devices and AI-driven safety systems, are likely to shape future OSHA standards. Businesses should stay informed about these developments.
9.2 Industry-Specific Regulations
Certain industries may see the introduction of more specialized OSHA standards to address unique risks. Staying aware of industry-specific regulations is crucial for compliance.
9.3 Pandemic Preparedness
The COVID-19 pandemic has highlighted the importance of pandemic preparedness in the workplace. OSHA may develop additional guidelines for managing health crises in the future.
Challenges and Controversies
10.1 Balancing Regulation and Business Interests
Balancing the need for workplace safety with business interests and economic considerations can be challenging. OSHA often faces debates over the stringency of its regulations.
10.2 OSHA Enforcement Challenges
Enforcing OSHA standards across all industries and workplaces is a monumental task. Limited resources and the sheer number of businesses make enforcement a complex endeavor.
10.3 Public Perception and Trust
Public perception of OSHA and trust in its effectiveness can impact compliance. Building trust through transparency and clear communication is essential for OSHA’s success.
Tips for Small Businesses
12.1 Navigating Compliance as a Small Business Owner
Small businesses often face distinct challenges in achieving OSHA compliance. This section offers guidance tailored to the needs of small business owners.
12.2 Leveraging OSHA Resources
OSHA provides resources specifically designed to assist small businesses in their compliance efforts. Learn how to make the most of these resources.
12.3 Building a Culture of Safety
Creating a culture of safety within your small business is essential. Discover practical steps to instill a safety mindset among your employees.
The Role of Employees
13.1 Reporting Unsafe Conditions
Empowering employees to report unsafe conditions is vital for early hazard identification and prevention. Learn how to encourage open communication.
13.2 Employee Training and Empowerment
Investing in employee training and providing them with the knowledge and tools to stay safe is a key responsibility of employers.
13.3 Encouraging a Safety Mindset
Fostering a safety mindset among employees ensures that safety remains a top priority in day-to-day operations.
Staying Updated
14.1 OSHA Updates and Amendments
Stay informed about changes to OSHA standards and regulations. Regularly checking for updates is crucial for maintaining compliance.
14.2 Industry News and Trends
Monitoring industry news and safety trends helps businesses anticipate changes and adapt their safety programs accordingly.
14.3 Professional Organizations
Joining professional safety organizations can provide valuable networking opportunities and access to industry expertise.
OSHA Requirements for Employers
Occupational Safety and Health Regulations in the USA
Which is Better: NEBOSH, IOSH, or OSHA?
OSHA 30-Hour Construction Certification
A Comprehensive Guide to OSHA Standards
Conclusion
In conclusion, OSHA standards are the cornerstone of workplace safety in the United States. Complying with these standards not only protects your employees but also offers legal, financial, and reputational benefits for your business. By understanding OSHA’s requirements, developing comprehensive safety programs, and staying proactive in addressing hazards, your organization can maintain a safe and thriving work environment.
It really helped when you mentioned the importance of training your employees. One of my uncles is starting a construction firm and wants to make sure there are no accidents during his project’s duration. I’ll email your tips about OSHA’s training tools to my uncle while he finds heavy machines and professional operators.
Good!