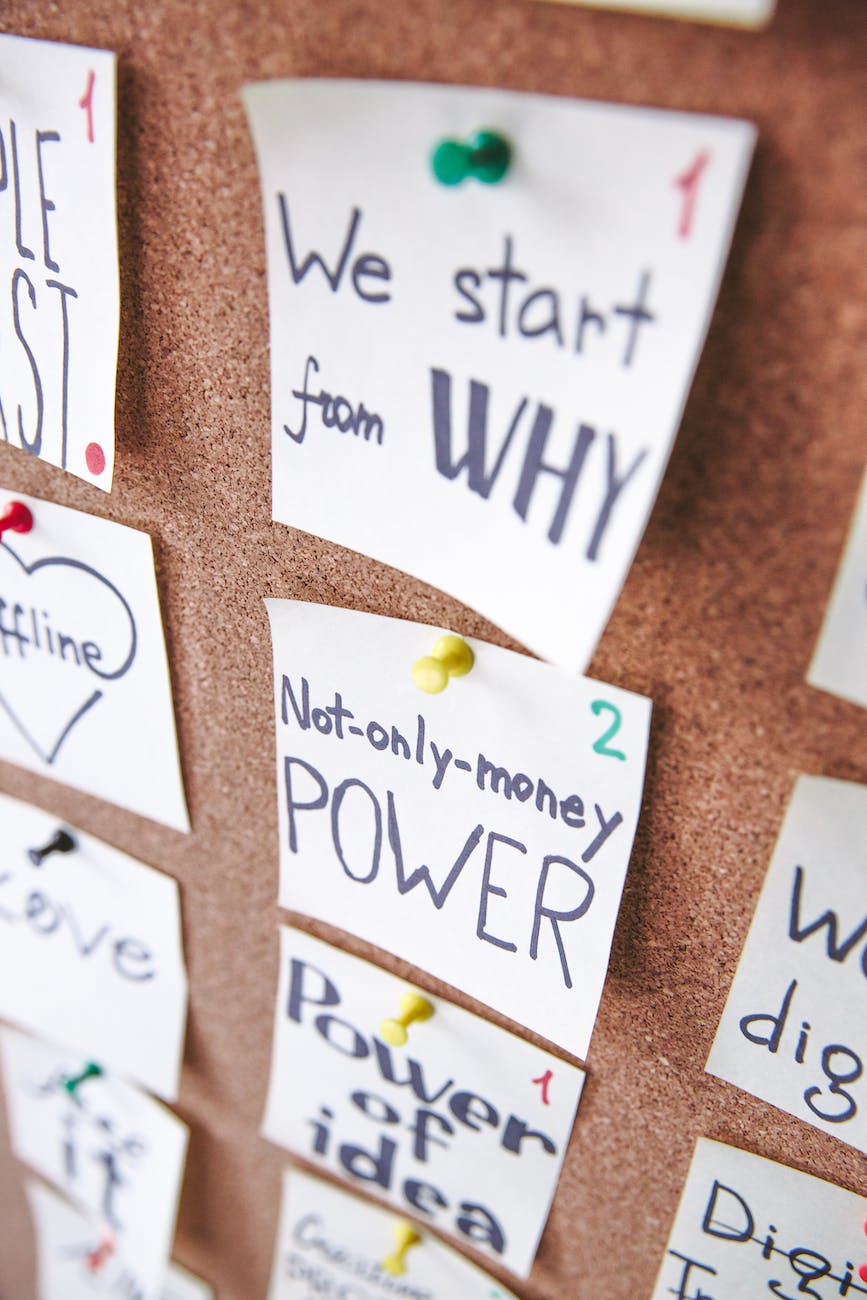
5 Why Analysis: Accident Investigation Method
Accidents are unfortunate events that can lead to injuries, property damage, and sometimes even fatalities. Understanding the root causes of accidents is essential to prevent their recurrence. One effective method for investigating accidents and uncovering the underlying causes is the “5 Why Analysis.” This article delves into the intricacies of the 5 Why Analysis as a powerful accident investigation technique.
Introduction
Accidents are disruptive events that can cause harm and disrupt the normal course of life or business operations. Investigating accidents thoroughly is crucial to avoid their recurrence and improve overall safety. The 5 Why Analysis is a structured approach that helps organizations delve deep into the causes of accidents, allowing them to address the root issues and prevent similar incidents in the future.
What is the 5 Why Analysis?
The 5 Why Analysis is a problem-solving technique aimed at identifying the root cause of an issue by repeatedly asking the question “Why?” Each successive answer leads to a deeper understanding of the problem until a foundational cause is uncovered. By addressing this root cause, organizations can implement effective preventive measures.
Origins of the 5 Why Analysis
Developed by Sakichi Toyoda, the founder of Toyota Industries, the 5 Why Analysis is a fundamental component of the Toyota Production System. Originally used in the manufacturing industry, this technique was later embraced across various sectors due to its effectiveness in uncovering underlying problems.
Applying the 5 Why Analysis
The 5 Why Analysis can be applied to various scenarios, including accidents. By investigating the chain of events leading to an accident and repeatedly asking “Why?” at each stage, investigators can move beyond the immediate causes and uncover systemic issues.
Imagine a scenario: a delivery truck gets involved in an accident. Instead of attributing the incident to mere chance, the 5 Why Analysis prompts a journey of inquiry. Why did the truck crash? The brakes malfunctioned. Why did the brakes malfunction? Lack of regular maintenance. Why wasn’t maintenance conducted? The maintenance schedule was not clearly defined. By consistently asking “Why?” at each stage, the analysis cuts through apparent causes and uncovers the intricacies beneath.
The Step-by-Step Process
Step 1: Ask the First “Why”
Begin by asking why the accident occurred. This will lead to an immediate cause. For example, if the accident involved a machine malfunction, the first “Why?” could reveal a lack of maintenance.
Step 2: Repeat the Questioning
For each answer obtained, ask “Why?” again. This process is repeated iteratively to dig deeper into the causes. Continuing the example, if inadequate maintenance was the answer, ask why maintenance was neglected.
Step 3: Identify the Root Cause
After several iterations, a root cause emerges. This cause, once addressed, can prevent similar accidents. In our example, the root cause might be a lack of standardized maintenance procedures.
Benefits of the 5 Why Analysis
- Thorough Understanding: The technique uncovers hidden factors that contribute to accidents.
- Cost-Effective: It doesn’t require advanced tools, making it accessible and affordable.
- Preventive Approach: By addressing root causes, it prevents future incidents.
- Continuous Improvement: Organizations can learn and enhance processes.
Limitations to Consider
- Surface-Level Answers: Superficial answers may hinder reaching the true root cause.
- Subjective Interpretation: Different investigators might derive different causes from the same analysis.
- Complex Situations: Some accidents have multifaceted causes that might not be fully addressed by this method alone.
Real-world Examples
Example 1: Manufacturing Industry An accident involving an employee’s hand getting caught in a machine. The initial “Why?” might reveal that the worker removed a safety guard.
Example 2: Healthcare Setting A patient fall in a hospital. Asking “Why?” could lead to discovering inadequate staff training as the root cause.
Comparing the 5 Why Analysis with Other Methods
Compared to single-cause investigation methods, the 5 Why Analysis delves deeper. It uncovers both direct and indirect causes, offering a more holistic view.
Industries that Benefit from the 5 Why Analysis
While popular in manufacturing, the method benefits any industry prone to accidents. Healthcare, aviation, construction, and transportation all find value in its application.
Training for Effective Implementation
Conducting effective 5 Why Analyses requires training. Understanding the method and refining questioning skills are crucial for accurate results.
Key Takeaways
The 5 Why Analysis is a powerful tool for accident investigation. By asking “Why?” iteratively, organizations can uncover root causes and implement preventive measures, fostering safer environments.
FAQs about 5 Why Analysis
Q1: What’s the core objective of the 5 Why Analysis? A1: The primary goal of the 5 Why Analysis is to uncover the root cause of a problem or issue. By repeatedly asking “Why?” and delving deeper into the layers of causation, this method aims to reveal the underlying factors that contribute to the occurrence of the problem.
Q2: Is the 5 Why Analysis exclusive to manufacturing? A2: No, the 5 Why Analysis is not exclusive to manufacturing. While it originated in the manufacturing sector, its applicability spans across various industries and domains. It is an adaptable problem-solving technique that can be used to investigate issues in healthcare, aviation, IT, construction, and more.
Q3: Can it be used proactively? A3: Yes, the 5 Why Analysis can be used proactively. While it is often employed to investigate and address problems after they occur, it can also be applied preemptively. By using the 5 Why Analysis to explore potential scenarios and their underlying causes, organizations can take preventive measures to avoid problems before they arise.
Q4: How long does an analysis typically take? A4: The duration of a 5 Why Analysis can vary depending on the complexity of the issue being investigated and the depth of analysis required. Simple problems might be resolved within a short timeframe, while more intricate issues could take longer. The focus should be on achieving a thorough understanding of the root cause rather than rushing the analysis.
Q5: Is expertise necessary for effective implementation? A5: While formal expertise is not a strict requirement, familiarity with the 5 Why Analysis methodology and the ability to ask insightful questions are essential for effective implementation. Training and practice can enhance one’s proficiency in conducting thorough and accurate analyses, leading to more valuable insights and solutions.
Difference between Accident and Incident in the workplace
Root Cause Analysis: Accident Investigation Method
Important ‘5Es’ for Accident Prevention
When More Accidents Happen at Workplace
How we can do Accident Investigation in Safety field
Conclusion
Accident prevention is a shared responsibility. The 5 Why Analysis equips organizations with a systematic approach to uncover hidden causes, facilitating the prevention of future accidents. Implementing this method not only enhances safety but also leads to continuous improvement. Remember, a safer future starts with a thorough understanding of the past.