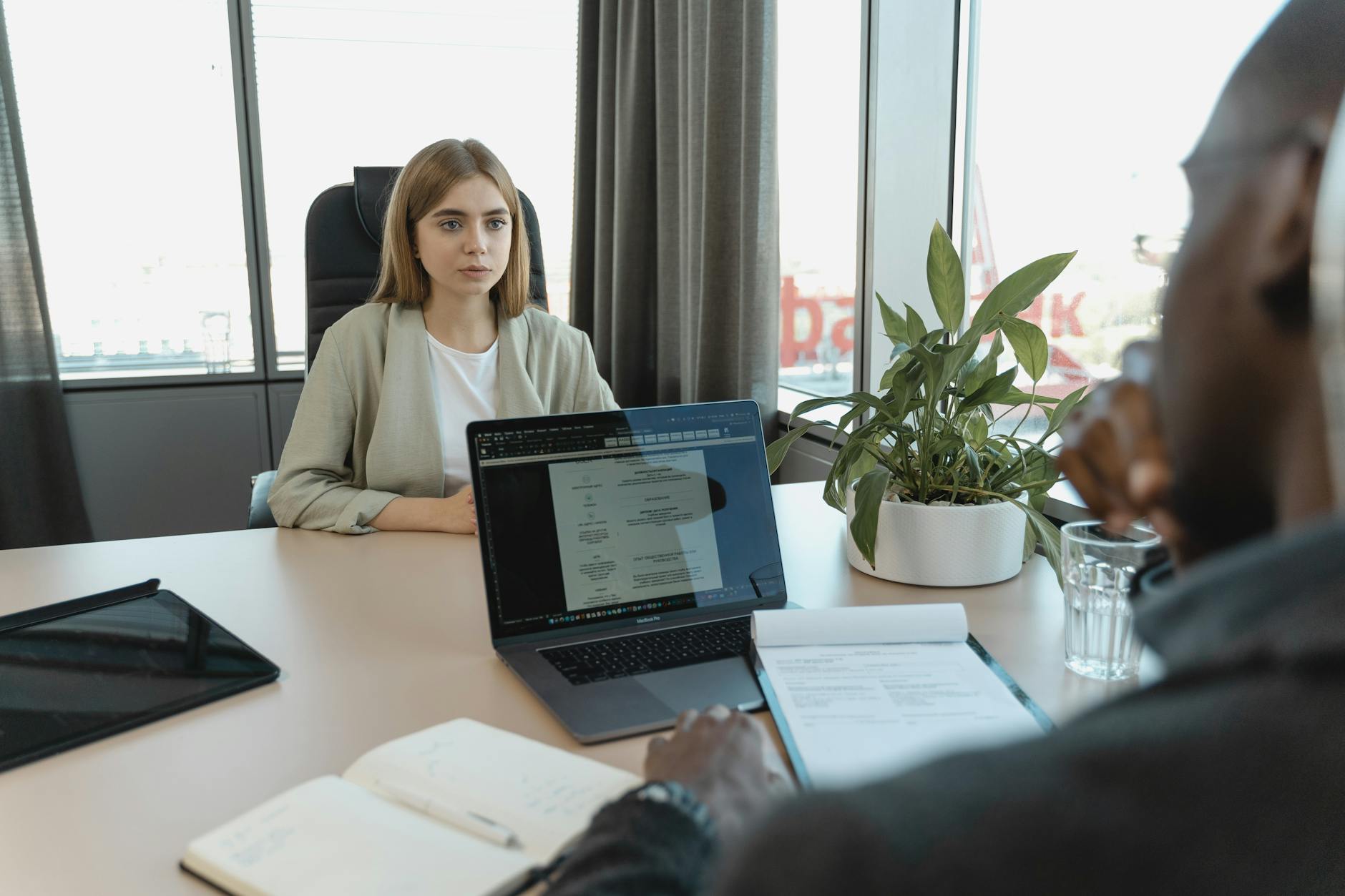
101 Safety Officer Interview Questions & Answers (2025 Edition)
Introduction
Preparing for a Safety Officer interview? Whether you’re an experienced professional or just starting your career in occupational health and safety (OHS), being ready for common and challenging interview questions is crucial. This guide provides 101 safety officer interview questions and answers to help you showcase your knowledge, skills, and problem-solving abilities.
From OSHA compliance to risk assessment and emergency response, these questions cover key areas employers evaluate. Use this resource to boost your confidence and stand out in your next interview.
General Safety Officer Interview Questions
1. What does a Safety Officer do?
A Safety Officer ensures workplace compliance with health and safety regulations, conducts risk assessments, implements safety policies, provides training, and investigates incidents to prevent future accidents.
2. Why did you choose a career in occupational health and safety?
(Example Answer) “I am passionate about protecting workers’ well-being and preventing workplace injuries. Safety is not just a job—it’s about saving lives and creating a culture of awareness.”
3. What are the key skills of a successful Safety Officer?
- Risk assessment & hazard identification
- Knowledge of OSHA/ISO standards
- Strong communication & training abilities
- Problem-solving & attention to detail
- Emergency response planning
4. How do you stay updated with safety regulations?
“I regularly review OSHA updates, attend industry seminars, participate in webinars, and follow safety organizations like NSC and ASSP.”
Technical Safety Interview Questions
5. Explain the hierarchy of controls for hazard mitigation.
The hierarchy includes:
- Elimination – Remove the hazard completely.
- Substitution – Replace with a safer alternative.
- Engineering Controls – Isolate workers from hazards (e.g., machine guards).
- Administrative Controls – Change work procedures (e.g., shift rotations).
- PPE – Personal protective equipment (last line of defense).
6. What is a Job Safety Analysis (JSA)?
A JSA breaks down job tasks to identify hazards and implement preventive measures before work begins.
7. How do you conduct a risk assessment?
- Identify hazards.
- Determine who may be harmed.
- Evaluate risks and implement controls.
- Record findings and review periodically.
8. What is the difference between a near miss and an accident?
- Near miss – An unplanned event with no injury or damage but potential for harm.
- Accident – An incident resulting in injury, illness, or property damage.
Behavioral & Situational Safety Questions
9. Describe a time you resolved a safety conflict between workers and management.
“A worker refused to wear PPE due to discomfort. I arranged a meeting, listened to concerns, and found an alternative PPE option that met safety standards while improving comfort.”
10. How would you handle an employee repeatedly violating safety protocols?
“I would first retrain the employee. If violations continue, I’d escalate with written warnings and, if necessary, disciplinary action—safety is non-negotiable.”
11. What steps would you take after a workplace injury?
- Provide immediate medical attention.
- Secure the scene.
- Report the incident per company policy.
- Investigate root causes.
- Implement corrective actions.
OSHA & Compliance Questions
12. What are OSHA’s recordkeeping requirements?
Employers must record work-related fatalities, injuries requiring medical treatment, lost time, or restricted work on OSHA Form 300.
13. When is a Lockout/Tagout (LOTO) procedure required?
LOTO is required when servicing or maintaining equipment where unexpected energization could cause injury.
14. What are the penalties for OSHA violations?
- Willful violations: Up to $161,323 per violation.
- Serious violations: Up to $16,131 per violation.
Workplace Hazard Identification & Control
15. How do you identify workplace hazards?
- Conduct regular inspections.
- Review incident reports.
- Engage employees in safety discussions.
- Use checklists and risk assessment tools.
16. What are common workplace hazards?
- Physical (slips, trips, falls)
- Chemical (toxic exposure)
- Biological (mold, viruses)
- Ergonomic (poor posture, repetitive strain)
- Psychosocial (stress, workplace violence)
17. How would you reduce ergonomic injuries in an office?
- Provide adjustable chairs & standing desks.
- Train employees on proper posture.
- Encourage micro-breaks & stretching.
- Ensure monitors are at eye level.
18. What’s the best way to control chemical hazards?
- Substitution (replace with safer chemicals).
- Ventilation (use fume hoods).
- PPE (gloves, respirators).
- Proper labeling & SDS (Safety Data Sheets) access.
Emergency Preparedness & Response
19. What should an emergency action plan include?
- Evacuation routes & assembly points.
- Emergency contacts (fire, medical, police).
- Roles & responsibilities.
- Procedures for fire, chemical spills, medical emergencies.
20. How often should fire drills be conducted?
At least once every 6 months (OSHA recommends).
21. What’s the first step in responding to a chemical spill?
- Alert personnel & evacuate if necessary.
- Contain the spill (use absorbents, barriers).
- Refer to SDS for cleanup procedures.
- Report & document the incident.
22. How do you ensure employees know emergency procedures?
- Regular training & drills.
- Post clear evacuation maps.
- Conduct safety briefings.
- Test emergency alarms periodically.
Safety Training & Communication
23. How do you make safety training engaging?
- Use real-life case studies.
- Interactive workshops (hands-on PPE demos).
- Gamification (quizzes, rewards).
- Encourage employee participation.
24. How would you train workers who speak different languages?
- Use multilingual training materials.
- Hire interpreters if needed.
- Visual aids (videos, diagrams).
- Hands-on demonstrations.
25. What’s the best way to promote a safety culture?
- Leadership commitment (management leads by example).
- Employee involvement (safety committees).
- Recognition programs (reward safe behavior).
- Open communication (reporting without fear).
Incident Investigation & Reporting
26. What’s the purpose of an incident investigation?
To identify root causes (not blame individuals) and prevent recurrence.
27. What tools do you use for incident investigations?
- 5 Whys (root cause analysis).
- Fishbone (Ishikawa) Diagram.
- Checklists & interviews.
28. How do you ensure accurate incident reporting?
- Train employees on reporting procedures.
- Make reporting easy (anonymous options).
- Investigate near misses.
- Document everything.
29. What’s the difference between immediate & root causes?
- Immediate cause – Direct trigger (e.g., wet floor caused slip).
- Root cause – Underlying failure (e.g., no warning signs, poor drainage).
OSHA & Regulatory Compliance
30. What are OSHA’s General Duty Clause requirements?
Employers must provide a workplace free from recognized hazards that could cause serious harm.
31. When is a permit required for confined space entry?
When the space has hazardous atmospheres, engulfment risks, or restricted entry/exit.
32. What are the key elements of a Hearing Conservation Program?
- Noise monitoring.
- Audiometric testing.
- Hearing protection (earplugs/muffs).
- Employee training.
33. What’s the maximum allowable noise exposure under OSHA?
90 dB for 8 hours (PEL). 85 dB requires hearing protection.
Behavioral & Situational Safety Questions
34. How would you handle a manager who ignores safety protocols?
- Present data (show risks & legal consequences).
- Escalate to higher management if needed.
- Offer solutions (cost-effective safety measures).
35. Describe a time you improved workplace safety.
“At my last job, I noticed frequent forklift near-misses. I implemented a traffic management system, reducing incidents by 60%.”
36. What would you do if an employee refuses to wear PPE?
- Explain risks & company policy.
- Provide alternative PPE if comfort is an issue.
- Enforce disciplinary action if non-compliance continues.
Advanced Safety Management Questions
37. What is a Safety Management System (SMS)?
A structured framework for managing safety risks, including policies, risk assessments, training, audits, and continuous improvement.
38. How do you measure safety performance?
- Lagging indicators (injury rates, lost days).
- Leading indicators (training completion, hazard reports).
39. What’s the role of AI in workplace safety?
- Predictive analytics (identifying risk patterns).
- Wearable tech (fatigue monitoring).
- Automated hazard detection (computer vision).
40. How do you ensure contractor safety compliance?
- Pre-qualification checks (safety records).
- Site-specific inductions.
- Regular audits & supervision.
OSHA & Regulatory Compliance
41. What is the purpose of a Hazard Communication Program (HazCom)?
To ensure employees understand chemical hazards through labeling, Safety Data Sheets (SDS), and training (OSHA’s Hazard Communication Standard 1910.1200).
42. What are the key elements of a Fall Protection Program?
- Guardrails & safety nets.
- Personal fall arrest systems (harnesses).
- Training on ladder & scaffold safety.
- Regular equipment inspections.
43. When is respiratory protection required?
When engineering controls (ventilation) can’t reduce airborne contaminants below Permissible Exposure Limits (PELs).
44. What’s the difference between PEL and TLV?
- PEL (OSHA) – Legal exposure limit.
- TLV (ACGIH) – Recommended guideline (often stricter).
45. How often should forklifts be inspected?
Daily (pre-operation checks) + formal inspections every 3 months.
Fire Safety & Prevention
46. What are the three elements of the fire triangle?
- Heat
- Fuel
- Oxygen
47. What’s the difference between a Class A and Class B fire extinguisher?
- Class A – Ordinary combustibles (wood, paper).
- Class B – Flammable liquids (gasoline, oil).
48. How often should fire extinguishers be inspected?
- Monthly (visual check).
- Annual (professional inspection).
- Every 12 years (hydrostatic testing).
49. What’s the PASS method for using a fire extinguisher?
- Pull the pin.
- Aim at the base of the fire.
- Squeeze the handle.
- Sweep side to side.
50. What are common causes of electrical fires?
- Faulty wiring.
- Overloaded circuits.
- Damaged extension cords.
Construction & Industrial Safety
51. What are the “Fatal Four” in construction?
- Falls
- Struck-by objects
- Electrocutions
- Caught-in/between
52. What’s the minimum safe distance from overhead power lines?
10 feet (OSHA 1926.1408) for equipment under 50kV.
53. How do you prevent trench collapses?
- Sloping or benching (angled walls).
- Shoring (supports).
- Shielding (trench boxes).
- Daily inspections.
54. What’s the maximum allowable scaffold platform gap?
1 inch (OSHA 1926.451(b)(1)).
55. What PPE is required for welding?
- Flame-resistant clothing.
- Welding helmet with shade lens.
- Leather gloves.
- Safety glasses under the helmet.
Environmental & Chemical Safety
56. What is an SPCC Plan?
Spill Prevention, Control, and Countermeasure Plan (EPA requirement for facilities storing oil).
57. What’s the difference between TWA and STEL?
- TWA (Time-Weighted Average) – Safe exposure over 8 hours.
- STEL (Short-Term Exposure Limit) – Max exposure for 15 mins.
58. How do you handle hazardous waste disposal?
- Follow EPA/RCRA regulations.
- Use licensed disposal contractors.
- Maintain waste manifests.
59. What’s the purpose of a HAZWOPER program?
To train workers handling hazardous waste operations & emergency response (OSHA 1910.120).
60. What are the 4 steps of spill response?
- Identify the substance (check SDS).
- Contain the spill (absorbents, barriers).
- Clean up (proper PPE & disposal).
- Report & document.
Behavioral & Situational Safety
61. How would you handle a worker who bypasses a machine guard?
- Stop work immediately.
- Explain the hazard (show injury examples).
- Retrain & monitor compliance.
62. Describe a time you prevented a serious accident.
“A worker was about to enter a confined space without testing. I stopped them, conducted air monitoring, and found oxygen deficiency—preventing a potential fatality.”
63. What would you do if you saw an unsafe condition but weren’t the Safety Officer?
- Report it immediately (supervisor/safety team).
- Warn nearby workers.
- Document it if unresolved.
64. How do you deal with complacency in safety?
- Rotate safety responsibilities.
- Share incident case studies.
- Introduce surprise drills.
65. What’s your approach to safety audits?
- Check compliance (OSHA, company policies).
- Interview workers for feedback.
- Prioritize corrective actions.
Advanced Safety Management
66. What is a Process Hazard Analysis (PHA)?
A systematic review of chemical/industrial processes to identify & mitigate risks (OSHA 1910.119).
67. How do you implement a Behavior-Based Safety (BBS) program?
- Observe & document safe/unsafe behaviors.
- Provide real-time feedback.
- Reward positive actions.
68. What’s the role of ergonomics in safety?
Reducing musculoskeletal disorders (MSDs) through workstation design, tools, and training.
69. How do you measure ROI on safety programs?
- Reduced injury costs (workers’ comp, downtime).
- Improved productivity.
- Lower insurance premiums.
70. What’s the difference between qualitative & quantitative risk assessment?
- Qualitative – Uses ratings (Low/Medium/High).
- Quantitative – Uses numerical data (probability x severity).
Workplace Safety Culture & Leadership
71. How would you improve safety culture in a resistant organization?
“I’d start with leadership buy-in by showing cost-benefit data. Then implement quick wins like visible safety metrics and recognition programs to build momentum.”
72. What’s your strategy for safety communication across multiple shifts?
- Digital dashboards with real-time updates
- Shift overlap meetings
- Multi-lingual safety bulletins
- “Safety接力” (relay) logbook between shifts
73. How do you handle safety suggestions from frontline workers?
“I maintain an anonymous suggestion system, acknowledge all input within 48 hours, and implement feasible ideas with public recognition.”
74. Describe your approach to safety committee management
“I structure committees with cross-functional reps, set clear KPIs (like hazard resolutions/month), and rotate leadership to maintain engagement.”
75. What metrics prove safety program effectiveness?
- Leading: Near-miss reports ↑, Training completion %
- Lagging: TRIR ↓, Severity rate ↓
- Cultural: Safety perception survey scores
Technical Safety Deep Dive
81. Explain ALARP principle in risk management
“As Low As Reasonably Practicable means reducing risks until cost of further reduction grossly outweighs benefit. We use cost-benefit analysis to determine this point.”
82. How would you conduct a dust explosion risk assessment?
- Identify combustible dusts (Kst testing)
- Evaluate ignition sources
- Check containment/accumulation areas
- Implement controls:
- Explosion venting
- Housekeeping program
- ATEX equipment
83. What’s your electrical arc flash protection strategy?
- NFPA 70E compliance
- Arc flash risk assessments
- Proper labeling
- HRC-rated PPE
- De-energization procedures
84. How do you validate LOTO procedures?
*”Through:
- Procedure audits
- Surprise equipment checks
- Employee demonstrations
- Energy tracing verification”*
85. What’s your confined space rescue plan?
- Tiered response:
- On-site trained team
- Local emergency services
- Specialized rescue contractor
- Quarterly mock drills
- Equipment checks (tripods, SCBA)
Emerging Safety Challenges
91. How are you addressing mental health in safety programs?
*”We’ve implemented:
- Psychological hazard assessments
- Mental health first aiders
- Stress-reduction job design
- Destigmatized reporting channels”*
92. What’s your WFH ergonomic safety approach?
- Virtual home office assessments
- Loaner equipment program
- “20-20-20” eye strain training
- MSD prevention chatbots
93. How do you manage contractor safety in gig economy work?
- Digital pre-qualification portals
- Micro-training modules
- Real-time compliance tracking apps
- Dynamic risk scoring algorithms
94. What’s your strategy for EV battery safety?
- Specialized storage compartments
- Thermal runaway detection
- Emergency response protocols
- Fire suppression system upgrades
95. How are you preparing for climate change safety impacts?
- Heat stress monitoring tech
- Flood resilience planning
- Air quality shelters
- Emergency supply caches
96. What’s your AI implementation roadmap for safety?
*”Phased approach:
- Predictive analytics for near-misses
- Computer vision for PPE detection
- Natural language processing for report analysis
- Autonomous hazard remediation”*
97. How do you balance productivity and safety pressures?
*”I use the Safety Maturity Curve model – proving that safety investments drive productivity through:
- Reduced disruption from incidents
- Improved workforce stability
- Enhanced operational reliability”*
98. What’s your innovation in safety training?
- VR hazard simulations
- Adaptive learning platforms
- Just-in-time microlearning
- Gamified competency assessments
99. How do you measure psychological safety?
- Regular pulse surveys
- 360-degree feedback
- Incident report tone analysis
- Retention/absenteeism metrics
100. What’s your plan for Gen Z safety engagement?
- TikTok-style safety shorts
- AR hazard spotting
- Safety influencer program
- Real-time feedback wearables
101. Where do you see workplace safety in 2030?
*”Integrated smart systems where:
- Wearables prevent fatigue incidents
- AI predicts equipment failures
- Digital twins simulate safety scenarios
- Robotics handle extreme hazards
But the human element remains central – technology enhances, never replaces, safety professionals’ judgment.”*
FAQs
How do I prepare for a Safety Officer interview?
- Research the company’s safety policies.
- Review OSHA/ISO standards.
- Practice situational questions.
- Bring examples of past safety improvements.
What certifications strengthen a Safety Officer’s resume?
- OSHA 30/510/511
- NEBOSH
- CSP (Certified Safety Professional)
- First Aid/CPR
What’s the biggest challenge Safety Officers face?
Balancing productivity and safety while ensuring compliance without disrupting operations.
Conclusion
Acing a Safety Officer interview requires technical knowledge, problem-solving skills, and strong communication. Use these 101 questions and answers to prepare effectively and demonstrate your expertise in workplace safety.
Stay confident, emphasize real-world examples, and show your commitment to preventing hazards—this will set you apart as a top candidate.
5 “What Would You Do?” Scenario Questions for Safety Officers
10 Must-Know Questions About Fall Protection Gear
Process Safety Management (PSM) Interview Questions & Answers
Root Cause Analysis (RCA) Interview Questions & Answers
How to Answer: ‘Why Should We Hire You as a Safety Officer?’ (7 Winning Responses)