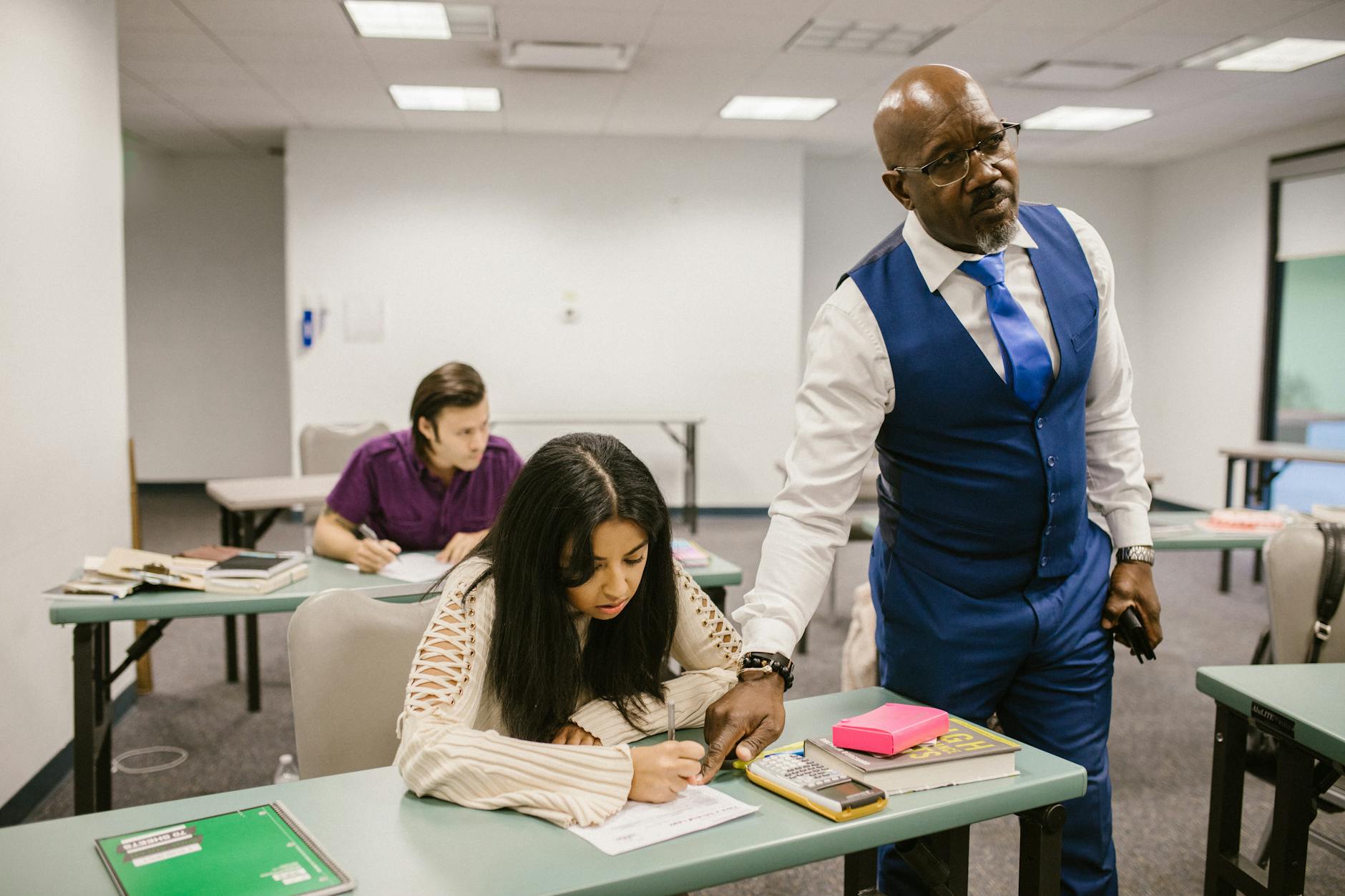
100 NEBOSH Exam Questions and Sample Answers
- Question: What are the key elements of a safety management system (SMS)? Answer: A safety management system typically includes elements such as policy and commitment, planning, implementation and operation, performance evaluation, and continual improvement.
- Question: Describe the hierarchy of controls used in occupational health and safety. Answer: The hierarchy of controls consists of elimination, substitution, engineering controls, administrative controls, and personal protective equipment (PPE). These controls are prioritized from most to least effective in minimizing hazards.
- Question: Explain the process of conducting a risk assessment in the workplace. Answer: A risk assessment involves identifying hazards, assessing the risks associated with those hazards, implementing control measures to mitigate risks, and reviewing and monitoring the effectiveness of those measures regularly.
- Question: What are the main responsibilities of a Safety Officer in a manufacturing plant? Answer: The responsibilities include conducting regular safety inspections, training employees on safety procedures, investigating incidents, maintaining safety records, and ensuring compliance with health and safety regulations.
- Question: What is the purpose of a Permit to Work system and when should it be used? Answer: A Permit to Work system is used to ensure that high-risk activities are carried out safely. It provides a formal written record of the precautions to be taken, the authorization to carry out work, and the completion of work. It should be used when conducting tasks such as hot work, electrical work, working in confined spaces, or working at heights.
- Question: Define and explain the concept of “near miss” in the workplace. Answer: A “near miss” is an event where an accident could have occurred but did not due to chance or quick intervention. Even though no injury or damage occurred, near misses should be reported and investigated to prevent future incidents by identifying potential hazards and addressing weaknesses in controls.
- Question: What are the main types of fire extinguishers and how should they be used? Answer: The main types of fire extinguishers include water, foam, dry powder, CO2, and wet chemical. Water extinguishers are used for Class A (solid) fires, foam for Class A and B (liquid) fires, dry powder for Class A, B, and C (gas) fires, CO2 for electrical and Class B fires, and wet chemical for Class F (cooking oils and fats) fires.
- Question: Describe the function of the Health and Safety Executive (HSE) in the UK. Answer: The HSE is the national regulatory body responsible for enforcing health and safety legislation in the UK. It provides guidance on safety standards, carries out inspections, investigates incidents, and ensures that workplaces comply with the legal requirements set out in the Health and Safety at Work Act.
- Question: What are the common causes of accidents in the workplace? Answer: Common causes of accidents include unsafe acts (such as improper use of equipment or failure to follow procedures), unsafe conditions (such as poorly maintained machinery or inadequate lighting), human error, lack of training, and poor management or supervision.
- Question: What is the importance of personal protective equipment (PPE) in the workplace? Answer: PPE is essential to protect workers from hazards that cannot be fully controlled by other means. It helps reduce the risk of injury or illness from hazards such as falling objects, exposure to chemicals, noise, or respiratory hazards. PPE should be used as a last resort, after other risk control measures have been implemented.
- Question: Explain the term “manual handling” and the risks associated with it. Answer: Manual handling refers to the physical effort of lifting, carrying, pushing, pulling, or lowering objects. Risks associated with manual handling include musculoskeletal injuries, strains, and sprains, especially when workers lift heavy objects incorrectly, overexert, or perform repetitive tasks without proper techniques.
- Question: What are the legal duties of employers under the Health and Safety at Work Act 1974 in the UK? Answer: Employers have a legal duty to ensure, as far as reasonably practicable, the health, safety, and welfare of their employees. This includes providing a safe working environment, adequate training, ensuring equipment is safe, conducting risk assessments, and taking appropriate action to control hazards.
- Question: Describe the steps involved in carrying out a fire risk assessment. Answer: The steps include identifying fire hazards, assessing the risks of fire occurring, evaluating the effectiveness of existing fire safety measures, recording findings and actions, implementing improvements, and reviewing the assessment periodically to ensure it remains current.
- Question: What is the difference between a hazard and a risk? Answer: A hazard is something that has the potential to cause harm, such as a chemical, machine, or process. A risk is the likelihood that the hazard will cause harm and the severity of that harm. While a hazard is inherent, a risk depends on the situation, environment, and controls in place.
- Question: What are the key principles of safe working at height? Answer: The key principles include eliminating the need for working at height where possible, using safe equipment such as scaffolding or ladders, ensuring proper training for workers, assessing the risks before work starts, and using fall protection equipment when required.
- Question: How can employers reduce the risks associated with noise exposure in the workplace? Answer: Employers can reduce noise risks by implementing engineering controls (e.g., using quieter machinery), administrative controls (e.g., rotating workers to limit exposure), providing hearing protection when necessary, and ensuring regular hearing checks for employees.
- Question: Explain the role of a Safety Officer in emergency response planning. Answer: A Safety Officer’s role in emergency response planning includes assessing potential emergency scenarios, creating emergency response procedures, training employees on emergency actions, conducting drills, ensuring the availability of emergency equipment, and coordinating with external emergency services.
- Question: What are the main types of workplace stress and their potential impact on employees? Answer: The main types of workplace stress include workload stress, interpersonal stress, role ambiguity, and work-life imbalance. Stress can lead to physical and mental health problems such as anxiety, depression, fatigue, and cardiovascular issues, as well as reduced productivity and increased absenteeism.
- Question: What is the purpose of a Safety Data Sheet (SDS) in the workplace? Answer: A Safety Data Sheet provides information on the properties of chemicals, the potential hazards, safe handling and storage procedures, emergency measures, and disposal guidelines. It helps workers understand the risks and take necessary precautions when handling hazardous substances.
- Question: Define “environmental impact assessment” (EIA) and its significance in the workplace. Answer: An Environmental Impact Assessment (EIA) is a process used to evaluate the potential environmental effects of a proposed project or activity before it begins. It is significant in identifying adverse effects, implementing mitigation measures, and ensuring compliance with environmental regulations to minimize harm to the environment.
- Question: What are the key principles of risk management in the workplace?
Answer: The key principles of risk management include identifying hazards, assessing the risks, implementing control measures, monitoring the effectiveness of controls, and reviewing and revising the risk management process regularly. The goal is to minimize risks and ensure a safe working environment.
- Question: Explain the concept of “safety culture” in an organization.
Answer: Safety culture refers to the shared attitudes, beliefs, values, and behaviors regarding safety within an organization. A positive safety culture encourages employees to prioritize safety, report hazards, and engage in safe practices, creating an environment where safety is integral to daily operations.
- Question: Describe the difference between a “dangerous occurrence” and a “reportable accident” under the Reporting of Injuries, Diseases and Dangerous Occurrences Regulations (RIDDOR).
Answer: A “dangerous occurrence” refers to an event that has the potential to cause harm, such as a major equipment failure, but does not necessarily result in injury or damage. A “reportable accident” refers to an event where a person has been injured or harmed and requires reporting under RIDDOR, such as a fatality or major injury.
- Question: What are the key elements of an emergency evacuation plan?
Answer: An emergency evacuation plan should include clear evacuation routes and assembly points, details of emergency exits, procedures for assisting vulnerable individuals, assigned responsibilities for employees and emergency services, regular drills, and communication methods for alerting everyone in the event of an emergency.
- Question: What is the purpose of a safety audit?
Answer: A safety audit is an assessment of an organization’s safety policies, procedures, and practices. It aims to identify hazards, evaluate risk controls, ensure compliance with safety regulations, and identify areas for improvement to prevent accidents and improve overall safety performance.
- Question: Explain the difference between direct and indirect costs of workplace accidents.
Answer: Direct costs are those immediately attributable to the accident, such as medical expenses, insurance claims, and compensation. Indirect costs include lost productivity, training new workers, damage to equipment, and reputational damage to the organization, which may not be immediately quantifiable but can be significant.
- Question: What are the health risks associated with exposure to asbestos in the workplace?
Answer: Exposure to asbestos can cause serious health issues such as lung cancer, mesothelioma, and asbestosis. The risk is higher when asbestos fibers are inhaled, leading to long-term respiratory problems. Workers exposed to asbestos must be properly trained, and controls should be in place to minimize exposure.
- Question: What steps should be taken to control the risks associated with working in confined spaces?
Answer: Steps include conducting a risk assessment, implementing a permit-to-work system, ensuring proper ventilation, providing personal protective equipment (PPE), ensuring there is a trained rescue team, and monitoring atmospheric conditions (e.g., oxygen levels, toxic gases) inside the confined space.
- Question: What are the main components of a health and safety policy?
Answer: A health and safety policy typically includes the organization’s commitment to health and safety, objectives for improving safety, the responsibilities of managers and employees, procedures for reporting and investigating incidents, and methods for evaluating and improving safety performance.
- Question: Explain the concept of “zero harm” and its significance in a safety management system.
Answer: “Zero harm” is a safety goal that aims for no injuries, fatalities, or harm to people, the environment, or assets. It signifies an organization’s commitment to achieving the highest standards of safety and protecting workers, with the ultimate goal of creating a culture where safety is embedded in every aspect of the workplace.
- Question: What is the purpose of a risk control hierarchy, and how is it applied in practice?
Answer: The purpose of the risk control hierarchy is to provide a structured approach to managing risks. It prioritizes control measures, with elimination of the hazard being the most effective method, followed by substitution, engineering controls, administrative controls, and finally PPE. In practice, hazards should first be eliminated or substituted, with PPE used as the last line of defense.
- Question: What are the main types of workplace hazards, and how can they be controlled?
Answer: The main types of workplace hazards include physical (e.g., noise, machinery), chemical (e.g., fumes, dust), biological (e.g., bacteria, viruses), ergonomic (e.g., repetitive strain), and psychosocial (e.g., stress, bullying). They can be controlled by eliminating or substituting hazardous processes, using engineering controls, providing PPE, and implementing safe work practices.
- Question: Describe the role of the Health and Safety Committee within an organization.
Answer: The Health and Safety Committee is a group of employees and management representatives responsible for promoting safety, discussing health and safety issues, conducting risk assessments, reviewing incidents, and recommending improvements. The committee plays a crucial role in fostering collaboration and improving the organization’s safety culture.
- Question: What is meant by the term “slips, trips, and falls,” and how can these hazards be minimized in the workplace?
Answer: Slips, trips, and falls refer to incidents where individuals lose their balance due to uneven surfaces, wet floors, cluttered walkways, or poor lighting. To minimize these hazards, employers should maintain clean, dry floors, provide proper lighting, ensure clear walkways, and train employees to be aware of potential risks.
- Question: What are the main principles of good manual handling techniques?
Answer: Good manual handling techniques include assessing the load before lifting, maintaining a stable stance, using the legs (not the back) to lift, keeping the load close to the body, avoiding twisting movements, and seeking assistance or using lifting equipment when necessary.
- Question: What is the significance of “toolbox talks” in a safety management system?
Answer: Toolbox talks are short, informal safety meetings where workers are briefed on specific safety issues, risks, or procedures. They help raise awareness, reinforce safe practices, and provide an opportunity for employees to ask questions or discuss concerns. Regular toolbox talks contribute to improving safety communication in the workplace.
- Question: What are the potential hazards of working with electricity, and how can they be controlled?
Answer: Potential hazards include electric shock, electrocution, burns, and fires. They can be controlled by ensuring proper insulation of electrical wiring, using circuit breakers, grounding electrical systems, providing PPE (e.g., rubber gloves, insulated tools), and ensuring that only qualified personnel perform electrical work.
- Question: What are the benefits of conducting a thorough accident investigation?
Answer: A thorough accident investigation helps identify the root cause of the incident, prevents similar accidents from occurring in the future, improves safety procedures, and ensures compliance with legal and regulatory requirements. It also provides valuable data for risk assessments and safety training programs.
- Question: How should workplace safety information be communicated to employees?
Answer: Safety information should be communicated clearly through signage, safety manuals, training sessions, meetings, and digital platforms. The communication should be easily understood by all employees, considering language barriers, literacy levels, and the use of visual aids for complex concepts.
- Question: What are the main responsibilities of employees in maintaining workplace safety?
Answer: Employees are responsible for following safety procedures, using equipment properly, reporting hazards and incidents, participating in training, wearing required PPE, and cooperating with management in creating a safe working environment. They also have a duty to ensure their own safety and the safety of others around them.
- Question: What is the role of safety signage in workplace safety?
Answer: Safety signage plays a vital role in alerting workers to potential hazards, guiding them on safe practices, and providing instructions in emergency situations. It helps prevent accidents by increasing awareness of risks, such as fire exits, hazardous materials, and protective equipment requirements.
- Question: What are the key factors that influence the effectiveness of a safety training program?
Answer: The effectiveness of a safety training program depends on factors such as clear objectives, relevance to the workplace, engagement and participation from employees, practical application, skilled trainers, regular updates, and a system for evaluating the program’s success and areas for improvement.
- Question: Explain the concept of “due diligence” in the context of workplace health and safety.
Answer: Due diligence refers to the legal obligation of employers to take all reasonable steps to prevent accidents and ensure the health and safety of workers. This includes conducting risk assessments, providing training, implementing safety measures, and ensuring that safety practices are followed at all times.
- Question: What is the purpose of conducting regular health surveillance in the workplace?
Answer: Health surveillance is used to monitor the health of employees who may be exposed to hazardous substances or working conditions, such as chemicals or repetitive physical strain. It helps identify early signs of occupational diseases or injuries, ensuring that preventive actions are taken to protect workers’ health.
- Question: What are the key features of a good safety leadership program?
Answer: A good safety leadership program focuses on creating a positive safety culture by training leaders to model safe behavior, make safety a priority in decision-making, engage workers in safety programs, hold everyone accountable for safety, and continuously improve safety standards through feedback and innovation.
- Question: Explain the concept of “safety by design” in engineering.
Answer: Safety by design is the principle of incorporating safety features into the design and engineering of equipment, processes, and systems from the outset, rather than relying on safety measures implemented afterward. This approach aims to eliminate or reduce hazards before they can cause harm, ensuring safer working conditions.
- Question: What is the importance of risk communication in the workplace?
Answer: Risk communication involves sharing information about hazards, risks, and safety practices with employees in a clear, understandable way. Effective communication helps workers recognize dangers, understand safety protocols, and make informed decisions, ultimately reducing the likelihood of accidents and improving overall safety.
- Question: What are the most common causes of workplace stress, and how can they be managed?
Answer: Common causes of workplace stress include high workloads, long hours, job insecurity, poor work-life balance, lack of control, and interpersonal conflicts. To manage stress, employers can provide support through employee assistance programs, promote a healthy work-life balance, improve workplace conditions, and encourage open communication.
- Question: What is the purpose of a Lockout/Tagout (LOTO) system, and when should it be used?
Answer: A Lockout/Tagout system is used to control hazardous energy during maintenance or repair activities to prevent accidental start-up of machinery or equipment. It involves locking or tagging equipment to ensure it cannot be operated until maintenance is completed. It should be used whenever machinery is being serviced or when there is a risk of unintended operation.
- Question: How can ergonomics be applied to reduce musculoskeletal disorders in the workplace?
Answer: Ergonomics can be applied by designing workstations, tools, and tasks that fit the capabilities and limitations of workers. This includes adjusting chair heights, workstation layouts, and equipment placement, encouraging regular breaks, providing lifting aids, and promoting proper posture to reduce strain on muscles and joints.
- Question: Describe the main features of a Health and Safety Management System (HSMS).
Answer: A Health and Safety Management System includes policies and procedures to ensure the health, safety, and well-being of employees. Key features include risk assessments, incident reporting systems, employee training, monitoring and auditing safety performance, management commitment, and continual improvement processes.
- Question: What is the purpose of a “safety moment” in meetings, and how can it contribute to a safer work environment?
Answer: A “safety moment” is a brief discussion at the beginning of meetings focused on a safety topic, hazard, or best practice. It reinforces safety awareness, encourages employees to think about potential risks, and fosters a safety culture by making safety a regular part of the workday.
- Question: What should be included in an accident investigation report?
Answer: An accident investigation report should include a description of the incident, the date, time, and location, the persons involved, the sequence of events leading up to the accident, the causes (direct and indirect), any immediate corrective actions taken, and recommendations for preventing similar accidents in the future.
- Question: What is the role of a safety supervisor in maintaining a safe work environment?
Answer: A safety supervisor ensures that safety protocols are being followed, conducts regular safety inspections, provides safety training to workers, investigates incidents, enforces safety rules, monitors workplace hazards, and works with management to implement improvements to safety standards.
- Question: What are the primary risks associated with working with hazardous chemicals, and how can they be controlled?
Answer: Primary risks associated with hazardous chemicals include inhalation of toxic fumes, skin exposure, and fires or explosions. These risks can be controlled by proper labeling and storage, using appropriate PPE (e.g., gloves, masks), providing ventilation, conducting regular safety training, and following safe handling procedures.
- Question: What is the difference between a “fatal accident” and a “major injury,” and how should they be reported?
Answer: A “fatal accident” results in the death of a person, while a “major injury” causes serious harm such as fractures, amputations, or loss of consciousness. Both must be reported to the relevant regulatory body (e.g., HSE in the UK) immediately, and an investigation should be conducted to identify the root causes and prevent recurrence.
- Question: What are the benefits of involving employees in the risk assessment process?
Answer: Involving employees in the risk assessment process helps identify potential hazards that might be overlooked, ensures the practical implementation of controls, increases worker buy-in and compliance with safety measures, and fosters a sense of ownership in the safety program.
- Question: What is meant by “safety-critical equipment,” and why is it important to maintain it?
Answer: Safety-critical equipment refers to machinery, tools, or systems that are essential to ensuring the safety of workers and preventing accidents. It is crucial to maintain such equipment through regular inspections, servicing, and testing to ensure it functions properly and does not pose a risk to health and safety.
- Question: What are the key considerations when developing a business continuity plan?
Answer: Key considerations include identifying critical business functions, assessing potential risks to these functions (such as natural disasters or equipment failures), developing strategies to maintain operations during disruptions, ensuring communication protocols, and regularly reviewing and updating the plan to reflect changes in the organization.
- Question: What is the role of the safety representative in a workplace safety committee?
Answer: A safety representative advocates for workers’ safety concerns, helps identify and assess hazards, participates in safety audits, assists in developing safety policies, and acts as a liaison between employees and management. They ensure that worker perspectives are considered in the development of safety measures.
- Question: What is the significance of a risk assessment in preventing workplace accidents?
Answer: A risk assessment is a systematic process used to identify hazards, assess the associated risks, and determine appropriate control measures to minimize or eliminate those risks. Conducting risk assessments helps prevent accidents by ensuring that hazards are recognized and adequately controlled before they can cause harm.
- Question: What are the key differences between qualitative and quantitative risk assessments?
Answer: Qualitative risk assessments focus on identifying hazards and assessing risks based on subjective factors such as expert judgment, experience, and observations. Quantitative risk assessments use numerical data and statistical methods to calculate the likelihood and potential impact of risks, providing a more objective and data-driven approach.
- Question: How should chemical spills be managed in the workplace?
Answer: Chemical spills should be managed by following the workplace’s emergency response procedures, which typically include alerting relevant personnel, containing the spill using appropriate materials (e.g., absorbents), ensuring proper ventilation, disposing of waste according to regulations, and reporting the incident to authorities if necessary.
- Question: What is the importance of involving top management in health and safety initiatives?
Answer: Involvement of top management is crucial in demonstrating commitment to health and safety, allocating sufficient resources, setting a safety-first culture, and ensuring compliance with legal requirements. Management’s support ensures the effectiveness of safety programs and encourages employee participation and accountability.
- Question: What are the key stages of an effective incident investigation?
Answer: The key stages include:
- Initial response: Securing the scene and providing medical assistance if needed.
- Fact-finding: Collecting evidence, interviewing witnesses, and recording details.
- Analysis: Identifying the root causes of the incident.
- Corrective actions: Implementing measures to prevent recurrence.
- Reporting and follow-up: Documenting findings, sharing lessons learned, and ensuring that improvements are implemented.
- Question: How can employers minimize the risks associated with repetitive strain injuries (RSI)?
Answer: Employers can minimize RSI risks by designing ergonomically-friendly workstations, promoting proper posture, encouraging regular breaks and stretching, rotating tasks to avoid repetitive movements, and providing workers with suitable tools and equipment to reduce strain on muscles and joints.
- Question: What are the key elements of a safe working procedure for working with hazardous substances?
Answer: A safe working procedure for working with hazardous substances should include:
- Identification of the hazardous substance and associated risks.
- Control measures (e.g., ventilation, PPE).
- Safe handling, storage, and disposal instructions.
- Emergency procedures for spills or exposures.
- Employee training and awareness of the risks.
- Question: What are the benefits of conducting regular safety inspections in the workplace?
Answer: Regular safety inspections help identify hazards before they lead to accidents, ensure that safety equipment is functioning properly, verify compliance with safety regulations, and provide opportunities to reinforce safe work practices. Inspections also demonstrate management’s commitment to maintaining a safe work environment.
- Question: Explain the term “safety culture” and its importance in achieving workplace safety goals.
Answer: Safety culture refers to the shared values, attitudes, and behaviors toward safety within an organization. A strong safety culture fosters employee involvement, encourages proactive hazard identification, and ensures that safety is prioritized in all aspects of the workplace. It plays a key role in reducing accidents and achieving long-term safety goals.
- Question: What are the primary components of a fire safety management plan?
Answer: A fire safety management plan should include:
- Risk assessment and identification of fire hazards.
- Fire prevention strategies and control measures.
- Emergency evacuation procedures and assembly points.
- Fire detection and suppression systems.
- Employee training and fire drills.
- Regular maintenance and inspection of fire safety equipment.
- Question: What is the role of personal protective equipment (PPE) in controlling workplace hazards?
Answer: PPE serves as a last line of defense in protecting workers from hazards when other control measures (e.g., elimination, substitution, or engineering controls) cannot fully mitigate risks. It includes items like gloves, helmets, eye protection, and respiratory protection, and should be used in conjunction with other safety measures to minimize exposure to hazards.
- Question: How should workplace accidents be reported and investigated to prevent future occurrences?
Answer: Accidents should be reported immediately to supervisors or safety officers. Investigations should be conducted promptly to determine the root causes, and findings should be documented. Corrective actions should be implemented to address the causes, and the lessons learned should be shared to improve safety practices and prevent recurrence.
- Question: What are the potential risks associated with working at height, and how can they be mitigated?
Answer: Risks associated with working at height include falls, falling objects, and structural instability. To mitigate these risks, employers should ensure that workers use fall protection systems (e.g., harnesses), secure tools and materials to prevent falling, provide safe access (e.g., ladders or scaffolding), and offer training on working safely at height.
- Question: What is the role of the safety officer in emergency preparedness and response?
Answer: The safety officer’s role includes developing and implementing emergency response plans, ensuring proper training for employees, conducting emergency drills, maintaining emergency equipment, coordinating with external emergency services, and ensuring that employees know their roles and responsibilities in case of an emergency.
- Question: What are the principles of the “hierarchy of controls” in managing workplace hazards?
Answer: The hierarchy of controls is a system for managing hazards in order of effectiveness:
- Elimination: Removing the hazard entirely.
- Substitution: Replacing the hazard with something less dangerous.
- Engineering controls: Modifying equipment or processes to reduce exposure to hazards.
- Administrative controls: Changing work practices or procedures to minimize risk.
- PPE: Providing personal protective equipment as a last resort.
- Question: How can safety training be made more effective for employees?
Answer: To make safety training more effective, it should be tailored to the specific risks and tasks of the workplace, incorporate hands-on practical exercises, engage employees through interactive methods, provide refresher courses, and ensure that training is relevant and up to date with current safety standards and regulations.
- Question: What is the significance of monitoring and reviewing safety performance in the workplace?
Answer: Monitoring and reviewing safety performance helps identify areas for improvement, measure the effectiveness of safety controls, ensure compliance with regulations, and track progress towards safety goals. It enables organizations to make data-driven decisions, identify trends, and implement corrective actions to continuously improve safety.
- Question: What are the key principles of safe manual handling?
Answer: Key principles of safe manual handling include assessing the load before lifting, maintaining a stable stance with feet shoulder-width apart, using the legs (not the back) to lift, keeping the load close to the body, avoiding twisting motions, and using lifting aids or seeking assistance when necessary.
- Question: How can workplace stress be reduced and managed effectively?
Answer: Workplace stress can be reduced by addressing causes such as excessive workload, lack of control, and interpersonal conflicts. Employers should promote work-life balance, provide resources for stress management (e.g., counseling services), encourage open communication, and create a supportive work environment.
- Question: What should be included in a health and safety induction for new employees?
Answer: A health and safety induction should include an introduction to the company’s safety policies, identification of key hazards in the workplace, emergency procedures (e.g., fire evacuation), use of PPE, accident reporting procedures, and the responsibilities of employees to maintain a safe work environment.
- Question: What is a safety audit, and why is it important in the workplace?
Answer: A safety audit is a systematic evaluation of an organization’s safety policies, procedures, and practices. It is conducted to assess compliance with safety regulations, identify hazards, and determine the effectiveness of safety controls. Audits are essential for identifying weaknesses, improving safety measures, and ensuring continuous improvement in workplace safety.
- Question: What are the potential health risks associated with exposure to noise in the workplace, and how can they be controlled?
Answer: Exposure to high levels of noise can lead to hearing loss, tinnitus, and increased stress. To control noise risks, employers can implement engineering controls such as soundproofing equipment, provide hearing protection (e.g., earplugs or earmuffs), maintain equipment to minimize noise, and reduce exposure time by rotating workers in noisy environments.
- Question: How can companies ensure that their contractors adhere to the same health and safety standards as their employees?
Answer: Companies can ensure contractors adhere to safety standards by providing them with the same safety training and guidelines as employees, requiring them to sign safety agreements, regularly monitoring their performance, conducting safety audits, and holding them accountable for adhering to the organization’s health and safety protocols.
- Question: What are the key considerations when developing an effective emergency evacuation plan?
Answer: Key considerations include:
- Clearly marked escape routes and exits.
- A designated assembly point.
- Adequate staff training and familiarization with the evacuation plan.
- Special provisions for disabled workers.
- Regular drills and practice evacuations.
- Communication systems for emergencies (e.g., alarms, public address systems).
- Question: What is the difference between a “hazard” and a “risk” in health and safety terminology?
Answer: A “hazard” refers to something that has the potential to cause harm (e.g., chemicals, machinery, or working at height). A “risk” refers to the likelihood of that harm occurring and the severity of its consequences. Risk is the combination of the probability of a hazardous event and the impact it could have.
- Question: What is the role of safety signs and labels in chemical safety?
Answer: Safety signs and labels play an essential role in identifying hazardous chemicals, their associated risks, and the precautions needed. They provide important information on handling, storage, and emergency measures, including first aid and firefighting instructions. Clear labeling helps prevent accidents and ensures proper handling and emergency response.
- Question: What is “zero harm,” and how can it be achieved in a workplace?
Answer: “Zero harm” refers to the goal of having no accidents, injuries, or harm to employees, the environment, or the community. Achieving zero harm requires a strong safety culture, proactive hazard identification, effective training, employee engagement, robust safety policies, and continuous monitoring and improvement of safety practices.
- Question: What are the different types of fire extinguishers, and what types of fires are they used for?
Answer: The different types of fire extinguishers and their uses include:
- Water extinguishers: For Class A fires (solid materials like wood and paper).
- Foam extinguishers: For Class A and Class B fires (flammable liquids).
- CO2 extinguishers: For Class B and electrical fires.
- Dry powder extinguishers: For Class A, B, C, and electrical fires.
- Wet chemical extinguishers: For Class F fires (cooking oils and fats).
- Question: What are the main legal duties of employers under the Health and Safety at Work Act (HSWA)?
Answer: The main legal duties of employers under the HSWA include:
- Providing a safe and healthy work environment.
- Ensuring that risks are controlled through risk assessments and safe working practices.
- Providing appropriate training and supervision to employees.
- Ensuring that safe equipment and materials are provided.
- Reporting and investigating accidents and incidents.
- Question: What are the common symptoms of heat stress, and what actions should be taken to prevent it?
Answer: Symptoms of heat stress include heavy sweating, dizziness, nausea, headache, confusion, and fainting. To prevent heat stress, employers should provide adequate hydration, shade, and rest breaks for workers, use cooling equipment, implement work-rest cycles, and ensure workers wear appropriate clothing to manage heat.
- Question: How should a workplace safety policy be developed and implemented?
Answer: A workplace safety policy should be developed by:
- Identifying workplace hazards and assessing associated risks.
- Setting clear safety goals and objectives.
- Defining roles and responsibilities for safety management.
- Outlining specific procedures for handling hazards and emergencies.
- Communicating the policy to all employees.
- Regularly reviewing and updating the policy to ensure continuous improvement.
- Question: How can an organization promote a positive safety culture among its employees?
Answer: An organization can promote a positive safety culture by:
- Leading by example with commitment from top management.
- Encouraging open communication about safety issues.
- Involving employees in safety decision-making.
- Providing regular safety training and awareness programs.
- Recognizing and rewarding safe behaviors and contributions to safety.
- Encouraging reporting of near-misses and unsafe conditions.
- Question: What are the essential elements of a safe system of work?
Answer: The essential elements of a safe system of work include:
- Clear procedures and instructions for performing tasks safely.
- Risk assessments to identify potential hazards.
- Appropriate control measures to mitigate risks.
- Training and supervision to ensure workers understand the procedures.
- Regular monitoring and review of the system to ensure its effectiveness.
- Question: What is the purpose of conducting a hazard analysis in the workplace?
Answer: The purpose of conducting a hazard analysis is to identify potential hazards, assess the risks they present, and determine appropriate control measures. It helps to prevent accidents and injuries by addressing hazards before they can cause harm, ensuring a safer working environment.
- Question: What should be included in a workplace’s first-aid kit?
Answer: A workplace’s first-aid kit should include:
- Bandages, gauze pads, and adhesive tape.
- Antiseptic wipes or solutions.
- Scissors and tweezers.
- Sterile dressings and cold packs.
- Disposable gloves.
- A first-aid manual and emergency contact information.
- Pain relievers and any specific medical supplies required for employees.
- Question: What is the significance of having a crisis management plan in place?
Answer: A crisis management plan outlines the procedures for managing emergencies, such as natural disasters, accidents, or major incidents. Its significance lies in ensuring a quick, coordinated response to minimize harm, protect employees, and restore normal operations as quickly as possible.
- Question: How can an organization effectively manage contractors to ensure workplace safety?
Answer: To effectively manage contractors, an organization should:
- Provide them with a clear induction on safety policies and procedures.
- Ensure they are adequately trained and equipped for the tasks.
- Regularly monitor and audit their safety practices.
- Hold them accountable for following safety protocols.
- Maintain open communication to address safety concerns promptly.
- Question: What are the key challenges in implementing a workplace health and safety program?
Answer: Key challenges include:
- Resistance to change or a lack of buy-in from employees or management.
- Insufficient resources or budget for safety initiatives.
- Difficulty in maintaining ongoing employee engagement and compliance.
- Identifying and mitigating all potential hazards in complex work environments.
- Keeping up with changing regulations and industry standards.
- Question: What is the role of safety committees in improving workplace health and safety?
Answer: Safety committees play a crucial role in improving health and safety by facilitating communication between management and employees, identifying hazards, recommending safety improvements, conducting safety audits, and ensuring that health and safety policies are followed and regularly updated.
- Question: How can workplace accidents be prevented through employee involvement?
Answer: Workplace accidents can be prevented through employee involvement by engaging workers in hazard identification, involving them in the risk assessment process, encouraging them to report near-misses and unsafe conditions, and fostering a culture where employees take responsibility for their own and their colleagues’ safety.
NEBOSH Idip Exam Questions and Sample Answers
A great lesson and an eye opening.
With this NEBOCH can be easily pass.