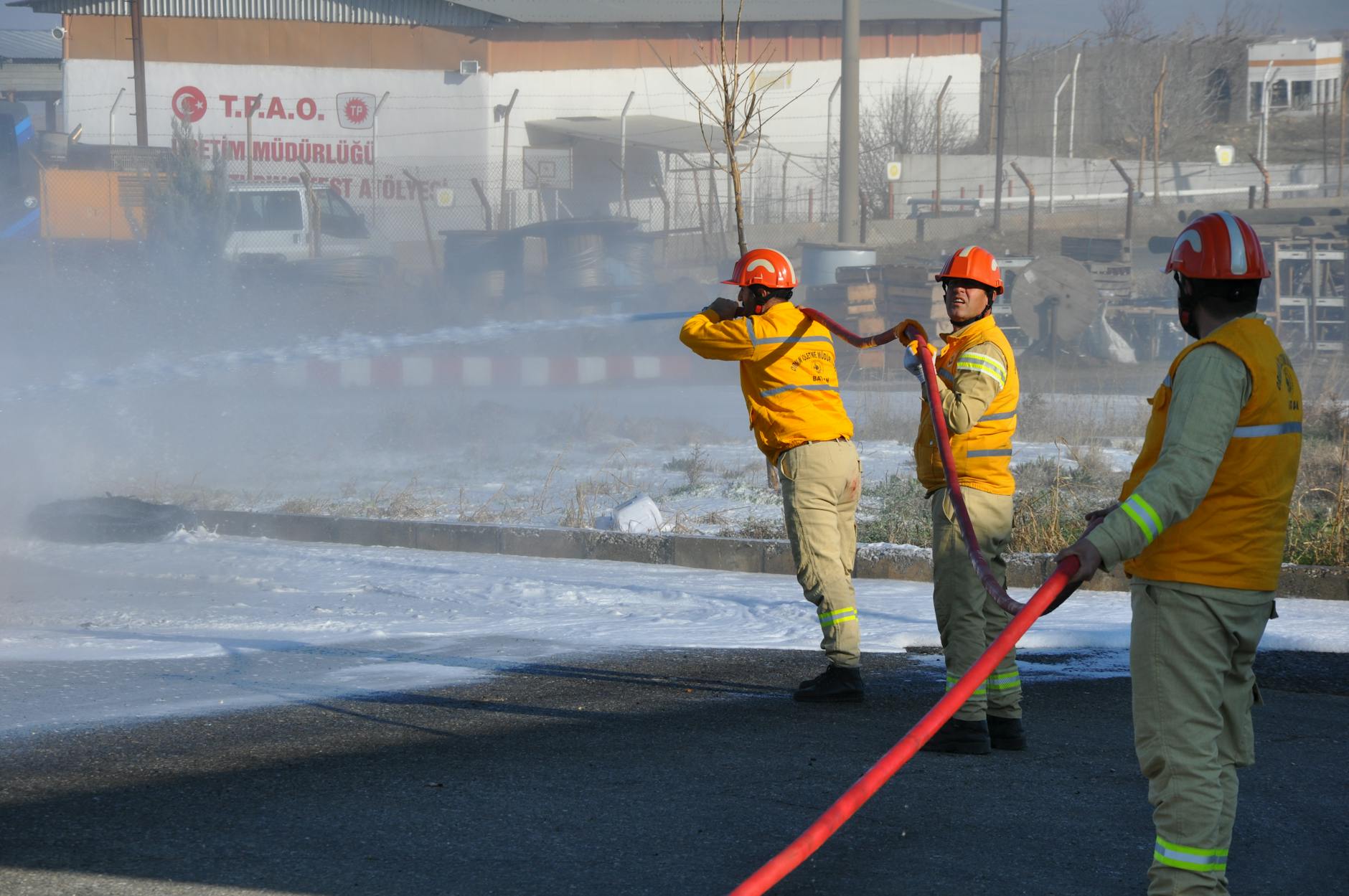
Onsite Emergency Plan under Factories Act, 1948
Introduction
Factories are the backbone of industrial development, but they are not without risks. Emergencies such as fires, chemical spills, or equipment failures can lead to catastrophic consequences. That’s where the Factories Act, 1948, comes into play. Designed to ensure worker safety, this legislation mandates the implementation of an onsite emergency plan.
But what exactly is an onsite emergency plan? And why is it so crucial? Let’s dive in.
Legal Framework
The Factories Act, 1948, establishes a robust framework for safeguarding workers. Section 41B specifically requires factories handling hazardous processes to prepare and implement emergency plans. Management must outline detailed strategies for handling crises, thereby ensuring compliance with this critical law.
What Is an Onsite Emergency Plan?
An onsite emergency plan is a detailed blueprint designed to respond to potential emergencies within a factory. It identifies hazards, mitigates risks, and ensures a swift and efficient response to emergencies.
Key Elements of an Onsite Emergency Plan
- Risk Identification: Pinpoint potential hazards.
- Response Strategies: Detail specific actions for emergencies.
- Coordination: Ensure collaboration among staff, authorities, and emergency services.
Types of Emergencies Covered
Factories face a wide range of potential emergencies. The most common include:
- Fire and Explosions: Often due to electrical faults or flammable materials.
- Chemical Leaks and Spills: Hazardous chemicals can pose significant risks.
- Natural Disasters: Earthquakes, floods, and storms.
- Industrial Accidents: Equipment malfunctions and human errors.
Steps in Preparing an Onsite Emergency Plan
1. Risk Assessment and Hazard Identification
Every emergency plan starts with a thorough risk analysis. Factories must evaluate all potential threats and their impact.
2. Formation of an Emergency Response Team
This team includes trained personnel responsible for coordinating and executing the emergency plan.
3. Developing Response Procedures
From evacuation protocols to medical aid, detailed steps must be outlined for every scenario.
4. Communication Protocols
Clear communication channels must be established to ensure timely information sharing during emergencies.
Components of an Onsite Emergency Plan
Emergency Response Procedures
Detailed actions for various scenarios, including fire drills and first-aid responses.
Evacuation Plans
Routes, assembly points, and procedures for safe evacuations.
Resource Allocation
Stocking essentials like firefighting equipment, medical supplies, and safety gear.
Training and Drills
Regular training sessions ensure everyone knows their role during an emergency.
Role of Safety Officers in Emergency Planning
Safety officers play a pivotal role in emergency preparedness. They oversee risk assessments, develop response strategies, and act as liaisons with local authorities.
Emergency Control Room
An emergency control room serves as the nerve center during a crisis. Equipped with communication devices, floor plans, and emergency kits, this room enables efficient management of emergencies.
Training and Awareness Programs
Drills and training sessions are not optional; they are a necessity. Workers must be familiar with emergency protocols to ensure a swift response.
Legal Penalties for Non-Compliance
Failure to comply with the Factories Act can lead to severe consequences, including fines, imprisonment, and factory closure. Case studies highlight the importance of adhering to these regulations.
Importance of Community Involvement
Factories must collaborate with local communities to enhance preparedness. Mutual aid agreements and community training sessions can make a significant difference during emergencies.
Challenges in Implementing Onsite Emergency Plans
- Lack of Awareness: Many factories overlook the importance of emergency plans.
- Resource Constraints: Smaller factories often struggle with limited budgets.
- Resistance to Change: Employees may resist new protocols.
Best Practices for Effective Emergency Planning
- Learn from successful implementations.
- Regularly update and improve emergency plans.
- Involve employees at every stage.
Benefits of Onsite Emergency Plans
- Protects workers and assets.
- Builds trust with employees and the community.
- Enhances compliance and reduces legal risks.
The Factories Act, 1948 is a significant piece of legislation in India that aims to regulate the working conditions in factories and ensure the safety, health, and welfare of workers. Under the Act, an Onsite Emergency Plan (OEP) is an essential requirement for factories, especially those involved in hazardous operations or dealing with dangerous substances. Here’s an outline of the key points related to the Onsite Emergency Plan under the Factories Act, 1948:
1. Purpose of the Onsite Emergency Plan (OEP)
The purpose of the OEP is to ensure that workers and management are prepared to handle emergency situations like fire, explosions, chemical spills, accidents, or natural disasters. The plan helps in minimizing injuries, damage, and loss of life, ensuring a safe working environment.
2. Key Components of the Onsite Emergency Plan
- Identification of Potential Hazards: The plan must first identify all potential risks and hazards that could lead to emergencies, such as the use of hazardous chemicals, equipment malfunctions, and structural failures.
- Roles and Responsibilities: Clear designation of roles and responsibilities among employees, supervisors, and emergency response teams. This includes training of key personnel in emergency procedures and evacuation plans.
- Communication Procedures: Methods of alerting employees to an emergency (e.g., alarm systems, communication channels), including internal and external communication (with local authorities, hospitals, etc.).
- Evacuation Plans: Well-defined evacuation routes and assembly points. Drills should be conducted regularly to ensure employees know how to evacuate safely.
- First-Aid and Medical Assistance: The plan should include arrangements for providing immediate medical treatment and first aid, as well as emergency medical services.
- Fire Safety Measures: Plans for handling fires, including fire extinguishers, water systems, fire alarms, and fire-fighting training for employees.
- Emergency Equipment: Availability of emergency equipment like fire extinguishers, safety showers, eye wash stations, and protective clothing.
3. Training and Awareness
- Employee Training: All employees must be regularly trained on the emergency procedures, including how to evacuate, operate fire safety equipment, and report hazards.
- Mock Drills: The Act mandates that factories conduct mock drills regularly to ensure the preparedness of the workforce.
4. Maintenance of Emergency Resources
- Safety Equipment: Regular maintenance and inspection of safety equipment and emergency supplies are crucial. These include fire alarms, emergency exits, medical supplies, and firefighting gear.
- Update and Review: The emergency plan must be reviewed periodically to address new risks, changes in factory operations, or regulatory updates.
5. Emergency Response Team
Factories are required to set up an emergency response team with trained members capable of addressing any situation swiftly. The team should consist of first-aiders, fire safety officers, and trained emergency response personnel.
6. Regulatory Compliance
The Factories Act, 1948 mandates compliance with safety provisions and emergency preparedness. Non-compliance can lead to penalties or the closure of the factory.
7. Local Authority Involvement
Factories must coordinate with local authorities, such as fire departments, hospitals, and police, to ensure an effective emergency response. This includes sharing emergency plans with them and working with them during drills.
In summary, the Onsite Emergency Plan under the Factories Act, 1948 plays a critical role in ensuring the safety of workers and minimizing the impact of emergencies. It is vital for factory management to not only develop a comprehensive plan but also to conduct regular drills, maintain safety equipment, and provide continuous training to employees.
Conclusion
Emergencies are unpredictable, but preparedness isn’t. An onsite emergency plan is not just a legal requirement—it’s a lifesaving necessity. Factories must prioritize safety, ensuring that every worker returns home safely at the end of the day.
Off-Site Emergency Plan | Free Download
ON-SITE EMERGENCY PLAN | Free Download
Top 10 Essential Safety Documents Every Company Needs
List of Health and Safety Legislation
FAQs
1. What is the main purpose of an onsite emergency plan?
To ensure the safety of workers and minimize damage during emergencies.
2. Who is responsible for preparing an onsite emergency plan in a factory?
The factory management and safety officers.
3. How often should emergency drills be conducted?
At least once every six months.
4. What role does the community play in onsite emergency plans?
They provide mutual aid and can assist in large-scale emergencies.
5. What are the penalties for non-compliance with the Factories Act, 1948?
Penalties include fines, imprisonment, and even factory closure.