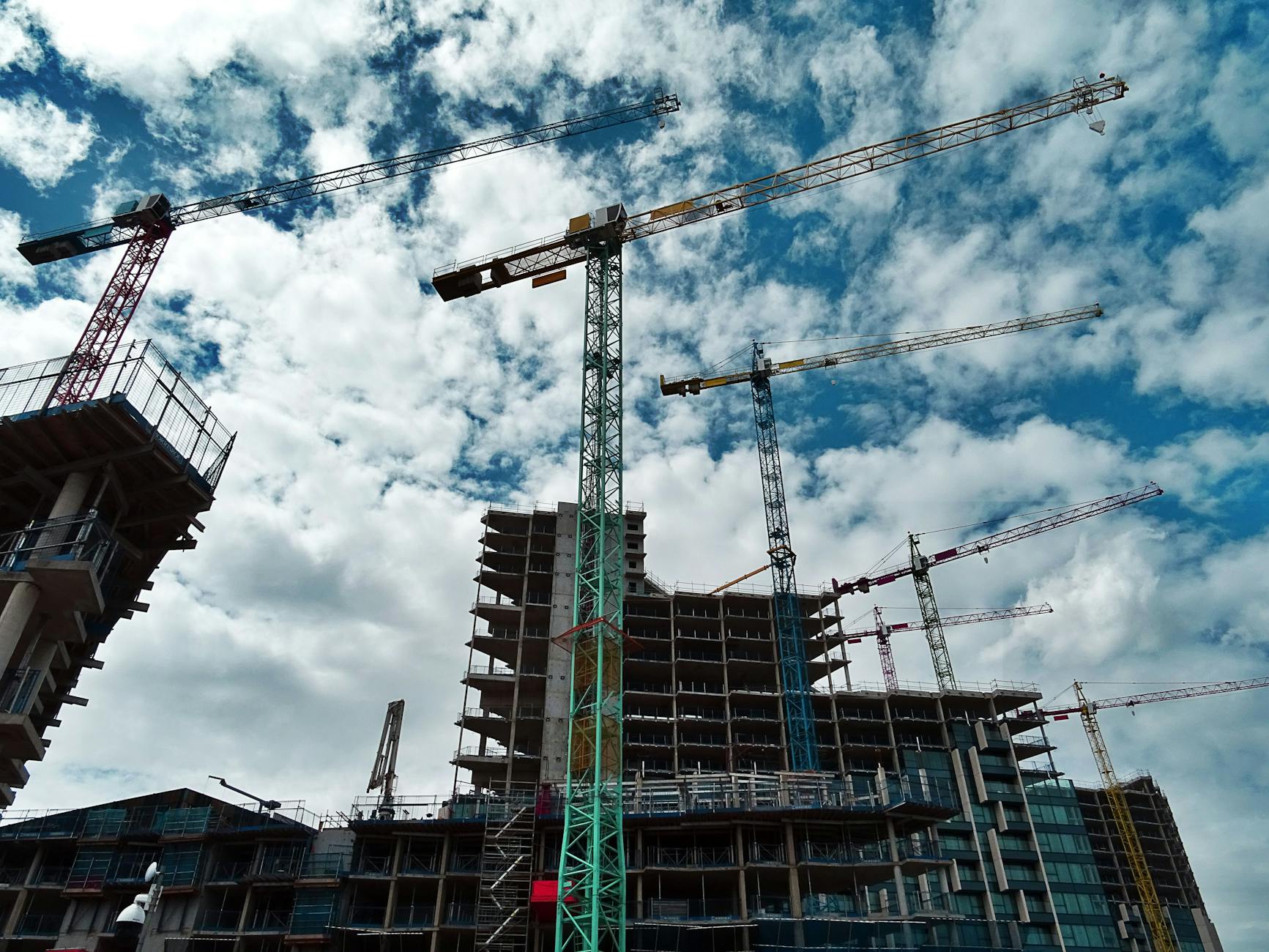
How Many Earthing Required for Tower Crane
Introduction
Ever wondered why tower cranes are a common sight on construction sites but rarely face electrical mishaps? One word: earthing. This crucial safety mechanism ensures that these towering machines operate smoothly and safely, protecting both workers and equipment. So, how many earthing systems are required for a tower crane? Let’s break it down.
What Is Earthing?
Earthing is a protective measure in electrical systems that connects the metallic parts of equipment to the ground. This prevents electrical shocks, safeguards equipment, and ensures that any fault current is safely discharged into the earth. Think of it as the grounding of an airplane during refueling—absolutely necessary to avoid sparks and accidents.
Importance of Earthing for Tower Cranes
Tower cranes are massive structures that rely heavily on electrical systems for operation. Without proper earthing, these machines are at risk of electrical faults, which could lead to dangerous sparks or even fires. Proper earthing:
- Protects workers from electric shocks.
- Prevents damage to the crane’s electrical components.
- Ensures consistent operation even in adverse weather conditions.
Tower Crane Electrical Components
A typical tower crane includes:
- Electrical motors
- Control panels
- Lighting systems
Each of these components is a potential source of electrical hazards, making a robust earthing system essential.
Factors Determining Earthing Requirements
The number of earthing points needed depends on:
- Crane Height: Taller cranes require additional points to manage electrical discharge effectively.
- Electrical Load: High-powered cranes need more robust earthing systems.
- Environmental Conditions: Corrosive environments or high-moisture areas may require specialized materials or extra points.
Standard Earthing Practices for Tower Cranes
Industry standards often recommend:
- At least two separate earthing points for redundancy.
- Proper placement near the crane’s base for effective fault current dissipation.
Number of Earthing Points for Tower Cranes
Typically, two to four earthing points are standard. These include:
- One for the main crane structure.
- One for the electrical panel.
- Additional points for high-capacity or specialized cranes.
Calculation of Earthing Needs
The calculation involves:
- Assessing Soil Resistance: High-resistance soils may require deeper or multiple electrodes.
- Determining Fault Current: Larger currents need more robust systems.
- Compliance with Standards: Refer to local regulations for specific guidelines.
Materials Used for Tower Crane Earthing
Common materials include:
- Copper: Durable and highly conductive.
- Galvanized Steel: Cost-effective but less durable in corrosive environments.
- Aluminum: Lightweight but prone to oxidation.
Installation of Earthing Systems
Proper installation involves:
- Burying electrodes deep into the ground.
- Connecting all metallic parts securely to the earthing system.
- Ensuring good soil contact for low resistance.
Regular Inspection and Maintenance
Periodic checks are vital to:
- Identify corrosion or wear.
- Ensure connections remain intact.
- Maintain low resistance levels.
Legal and Compliance Requirements
Each country has its own safety codes, such as IEC standards or OSHA regulations. Non-compliance can lead to hefty fines or operational shutdowns.
Common Challenges in Earthing Tower Cranes
- Corrosive Environments: Require specialized coatings.
- High Soil Resistance: May need deeper electrodes or chemical enhancement.
Case Study: Tower Crane Earthing
In a recent project, a construction company installed a 150-meter tower crane in a coastal area. By using copper electrodes and implementing four earthing points, they achieved compliance and operational safety, avoiding downtime despite the challenging environment.
The number of earthing (grounding) points required for a tower crane depends on several factors, including local regulations, the design of the crane, and site-specific conditions. Here are some general guidelines:
General Requirements for Earthing Tower Cranes:
- Main Earthing Point:
- At least one main earthing connection is required for the crane base. This ensures the crane is properly grounded and safe from electrical faults.
- Supplementary Earthing:
- Additional earthing points may be required for:
- Rotating parts of the crane to prevent electrical buildup due to friction or static.
- Control panels and electrical equipment associated with the crane.
- Additional earthing points may be required for:
- Local Standards and Regulations:
- Check local codes, such as IEC 60204, BS 7430, or national safety standards. They often specify the number of earthing points based on soil resistivity and crane size.
- Site Conditions:
- If the site has high soil resistivity, multiple earthing rods or a connected earthing grid may be required.
- If the crane operates near high-voltage lines or electrical substations, additional earthing may be necessary for protection.
- Testing and Verification:
- Ensure the earthing resistance is less than 1 ohm (or as required by local standards).
- Perform regular inspections and testing to maintain earthing integrity.
It’s essential to consult a licensed electrical engineer or safety expert to determine specific requirements for your project.
Conclusion
Earthing isn’t just a technical requirement; it’s the backbone of safety for tower cranes. Ensuring proper installation and maintenance safeguards lives and equipment, making it a non-negotiable part of crane operation.
Tower Crane Dismantling Safety Procedure
FAQs
1. How does earthing prevent accidents?
By directing fault currents into the ground, it prevents electrical shocks and fires.
2. Can tower cranes operate without earthing?
No, it’s a safety violation and increases the risk of fatal accidents.
3. What materials are best for earthing?
Copper is the most recommended due to its durability and conductivity.
4. How often should the earthing system be inspected?
Ideally, inspections should be conducted every six months.
5. What happens if earthing fails?
Electrical faults can lead to shocks, equipment damage, and even fatal accidents.