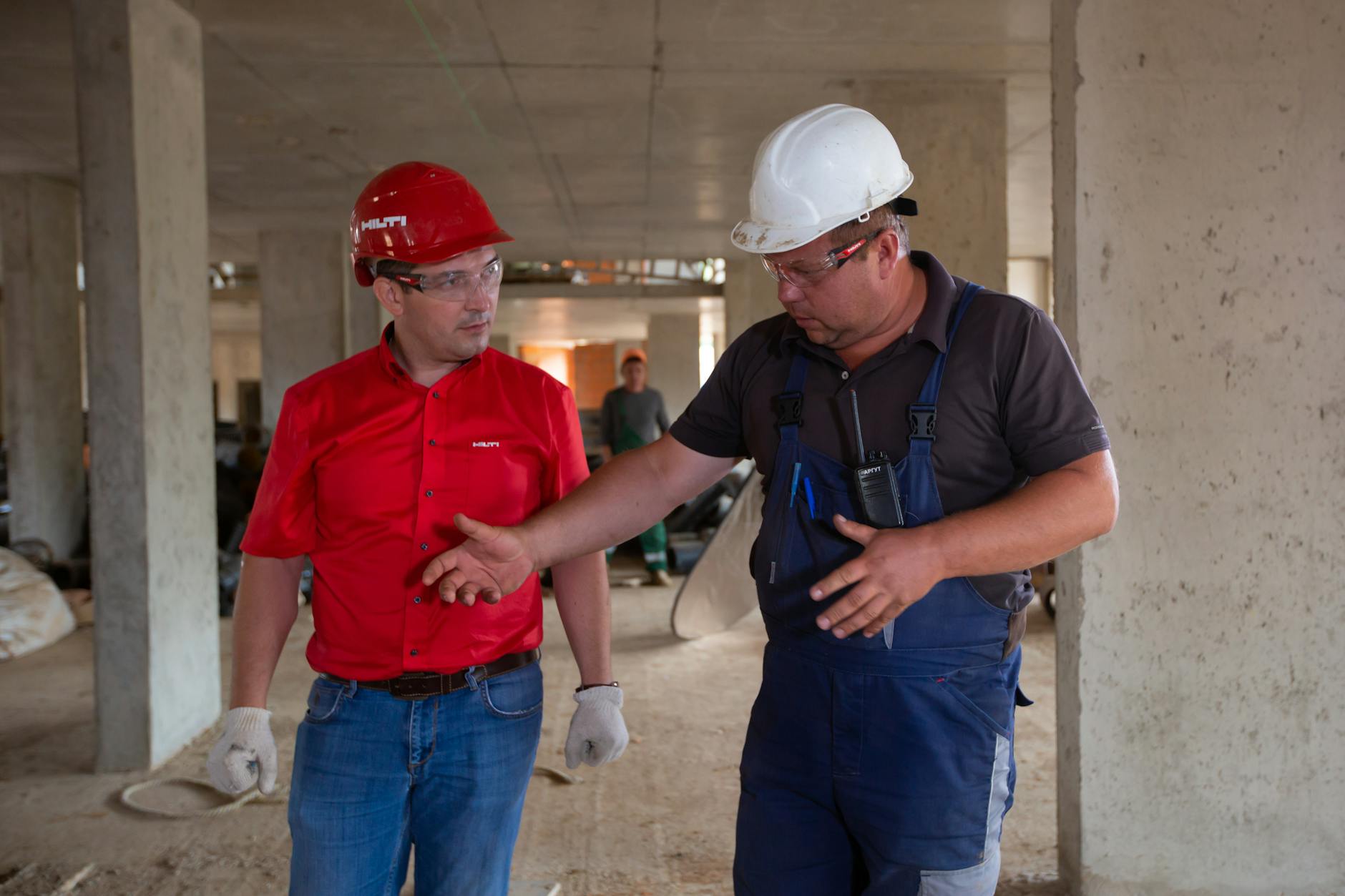
50 Responsibilities of an OSHA Safety Officer
Introduction
What is an OSHA Safety Officer?
An OSHA Safety Officer is a trained professional responsible for ensuring workplace safety and compliance with Occupational Safety and Health Administration (OSHA) regulations. These officers are critical in preventing workplace injuries, promoting health and safety standards, and creating a secure working environment for all employees.
Why OSHA Safety Officers Are Important
OSHA Safety Officers are the cornerstone of workplace safety. They not only prevent accidents but also foster a culture of safety. Their role is to safeguard both human lives and business assets by making sure every part of the workplace complies with safety regulations. In this article, we’ll explore the 50 key responsibilities of an OSHA Safety Officer.
Role and Purpose of an OSHA Safety Officer
Ensuring Compliance with OSHA Standards
The primary role of an OSHA Safety Officer is to ensure that the workplace adheres to OSHA’s stringent safety guidelines. Compliance helps prevent accidents and reduces legal and financial risks for businesses.
Protecting Employee Health and Safety
By overseeing health and safety procedures, an OSHA Safety Officer plays a direct role in protecting employees. This includes everything from maintaining equipment to ensuring that workers are properly trained to deal with hazardous situations.
50 Key Responsibilities of an OSHA Safety Officer
Planning and Development
- Conducting Workplace Risk Assessments
OSHA Safety Officers begin by assessing potential risks in the workplace. These assessments help identify hazards like slippery floors, heavy machinery, or poor ventilation, so they can take corrective action. - Developing Safety Protocols and Procedures
After assessing risks, they develop safety protocols and procedures to eliminate or control those hazards, ensuring the well-being of all employees. - Creating Safety Training Programs
Safety officers design and deliver training programs to educate employees on safety protocols, proper handling of equipment, and emergency procedures. - Reviewing and Updating Safety Policies
To maintain an effective safety culture, OSHA officers periodically review and update safety policies, ensuring they align with current regulations and best practices. - Preparing Safety Audits and Reports
Regular audits are conducted to ensure adherence to safety procedures. The results are documented in detailed reports for internal review and compliance verification.
Monitoring and Evaluation
- Inspecting Worksites Regularly
OSHA Safety Officers regularly inspect worksites to identify potential hazards. These inspections ensure that workers are not exposed to dangerous conditions. - Monitoring Safety Equipment
Ensuring that safety equipment, such as fire extinguishers, first-aid kits, and safety alarms, is in good working order is a key responsibility. - Ensuring Proper PPE Usage
Safety officers ensure employees use the necessary personal protective equipment (PPE) like helmets, gloves, and goggles to mitigate health risks. - Monitoring Hazardous Materials Handling
When dangerous substances are handled, it is crucial to monitor how they are stored, labeled, and disposed of to prevent accidents or contamination. - Ensuring Compliance with Environmental Health Regulations
Ensuring that work practices comply with environmental health standards is another key responsibility, preventing harm to both workers and the surrounding community.
Reporting and Documentation
- Investigating Accidents and Incidents
In the event of an accident, the safety officer investigates to determine its cause, document it, and recommend measures to prevent future incidents. - Reporting Workplace Injuries and Illnesses
Reporting injuries and illnesses as required by OSHA helps track workplace safety and supports legal compliance. - Maintaining OSHA Compliance Records
Keeping accurate records of workplace injuries, safety training, and inspections ensures ongoing compliance with OSHA regulations. - Preparing Detailed Safety Reports for Management
Safety officers prepare regular reports for management, highlighting potential hazards, safety concerns, and recommendations for improvements. - Documenting Safety Training Attendance
To comply with OSHA regulations, safety officers maintain records of employee participation in safety training sessions.
Training and Education
- Conducting Onboarding Safety Sessions
New employees are given a comprehensive safety orientation, which includes safety policies, emergency protocols, and potential workplace hazards. - Educating Workers About OSHA Standards
Educating employees on the latest OSHA standards and their role in maintaining safety is vital for compliance. - Leading Safety Drills and Emergency Response Trainings
Regular safety drills, such as fire or evacuation procedures, are conducted to ensure employees know how to act in an emergency. - Teaching First-Aid and CPR Skills
OSHA Safety Officers often provide or arrange for training in first aid and CPR to ensure workers can respond appropriately in case of medical emergencies. - Promoting Safety Awareness Programs
They organize campaigns and programs that keep safety at the forefront of employees’ minds, encouraging everyone to be proactive about safety.
Communication and Leadership
- Acting as a Safety Consultant for Management
As experts in OSHA regulations, Safety Officers consult with management on how to improve workplace safety policies. - Communicating Safety Policies to Employees
Ensuring that all employees understand and follow safety policies is a key task for OSHA Safety Officers. - Collaborating with Other Departments for Safety Initiatives
They collaborate with various departments, such as HR and Operations, to integrate safety into all aspects of the business. - Leading Safety Committees or Task Forces
Safety officers often lead committees or task forces focused on improving workplace safety and implementing new safety programs. - Managing Safety Program Budgets
Managing the budget for safety programs ensures that sufficient resources are allocated to training, equipment, and compliance efforts.
Regulatory Compliance
- Ensuring Compliance with Federal, State, and Local Regulations
An OSHA Safety Officer ensures that the workplace complies with all applicable federal, state, and local health and safety laws. - Interacting with OSHA Inspectors and Regulators
Regular interactions with OSHA inspectors help ensure that the workplace meets all the required standards and regulations. - Ensuring Correct Reporting of Safety Data
They oversee accurate reporting of safety data to OSHA and other authorities to maintain compliance. - Keeping Up-to-Date with OSHA Regulation Changes
They continuously monitor and adjust to changes in OSHA standards, ensuring the workplace remains compliant. - Facilitating OSHA Compliance Audits
Safety officers coordinate with external OSHA auditors to conduct regular compliance audits.
Risk Management
- Identifying Potential Workplace Hazards
Identifying hazards before they cause harm is one of the primary duties of a safety officer. - Implementing Risk Control Measures
Once hazards are identified, OSHA Safety Officers work to implement control measures to minimize risks. - Analyzing Safety Trends and Patterns
They analyze incident reports and safety data to identify trends and implement preventive measures. - Developing Emergency Response Plans
Developing detailed emergency plans for situations like fires, earthquakes, or chemical spills is crucial. - Conducting Safety Drills for Various Emergencies
Practicing emergency procedures ensures that employees are prepared for any crisis.
Employee Engagement
- Promoting a Safety-First Culture
A Safety Officer fosters a culture where safety is prioritized at all levels of the organization. - Encouraging Employee Participation in Safety Programs
Involving employees in safety initiatives helps create a more committed and aware workforce. - Responding to Safety Concerns and Complaints
Safety officers listen to employees’ safety concerns and take appropriate actions to resolve them. - Conducting Safety Surveys and Feedback Sessions
Feedback is gathered from employees to improve safety practices and policies. - Recognizing Employees for Safety Compliance
Recognizing and rewarding safety-conscious employees motivates others to follow suit.
Continuous Improvement
- Reviewing Incident Reports to Identify Improvement Areas
Post-incident reviews help highlight areas for improvement and prevent similar accidents in the future. - Implementing Lessons Learned from Safety Incidents
Applying lessons from past incidents helps strengthen safety protocols and minimize future risks. - Monitoring the Effectiveness of Safety Programs
Continuous monitoring ensures safety programs are effective and improvements are made as necessary. - Updating Safety Procedures Based on Feedback
They incorporate employee feedback into updated safety procedures, improving their effectiveness. - Enhancing Safety Protocols Over Time
The role of an OSHA Safety Officer includes continuously enhancing safety practices to stay ahead of evolving risks.
Specialized Responsibilities
- Overseeing Construction Safety
Construction sites present unique hazards, and safety officers ensure compliance with specific safety standards in this environment. - Managing Chemical Safety and Spill Response
Handling and disposing of hazardous chemicals safely is a major responsibility, including emergency response in case of spills. - Addressing Ergonomic Safety Concerns
Ensuring that workstations are ergonomically designed to prevent injuries like carpal tunnel or back strain is crucial. - Ensuring Fire Safety and Prevention
Ensuring fire hazards are minimized and proper fire safety procedures are followed is a critical responsibility. - Managing Electrical and Mechanical Safety Risks
Ensuring that electrical equipment is safely maintained and that employees follow mechanical safety guidelines is also vital.
Conclusion
The responsibilities of an OSHA Safety Officer are vast and integral to maintaining a safe and compliant workplace. From conducting inspections to fostering a safety-first culture, these professionals play a key role in protecting both employees and businesses. Their efforts ensure that workplaces not only meet regulatory requirements but also become environments where safety is a priority for everyone.
Advanced Knowledge for Safety Officers
Basic Knowledge for Safety Officer
10 Mistakes to Avoid as a New Safety Officer
Becoming a Safety Officer in 2024: Education, Skills, and Career Path
FAQs
- What qualifications do you need to become an OSHA Safety Officer?
OSHA Safety Officers typically need a background in safety management, industrial hygiene, or a related field, along with certifications like OSHA 30-hour or 40-hour training. - How often should OSHA Safety Officers conduct workplace inspections?
Inspections should be conducted regularly, with frequency depending on the size and nature of the workplace. Some high-risk areas may require more frequent inspections. - What are the most common safety issues OSHA Safety Officers handle?
Common safety concerns include falls, electrical hazards, hazardous material handling, machinery safety, and ergonomics. - Can an OSHA Safety Officer enforce safety policies on their own?
While they play a critical role in ensuring compliance, enforcing policies often involves collaboration with management and regulatory authorities. - How does an OSHA Safety Officer contribute to reducing workplace accidents?
By conducting regular inspections, providing safety training, and addressing potential hazards proactively, an OSHA Safety Officer helps minimize accidents and injuries.