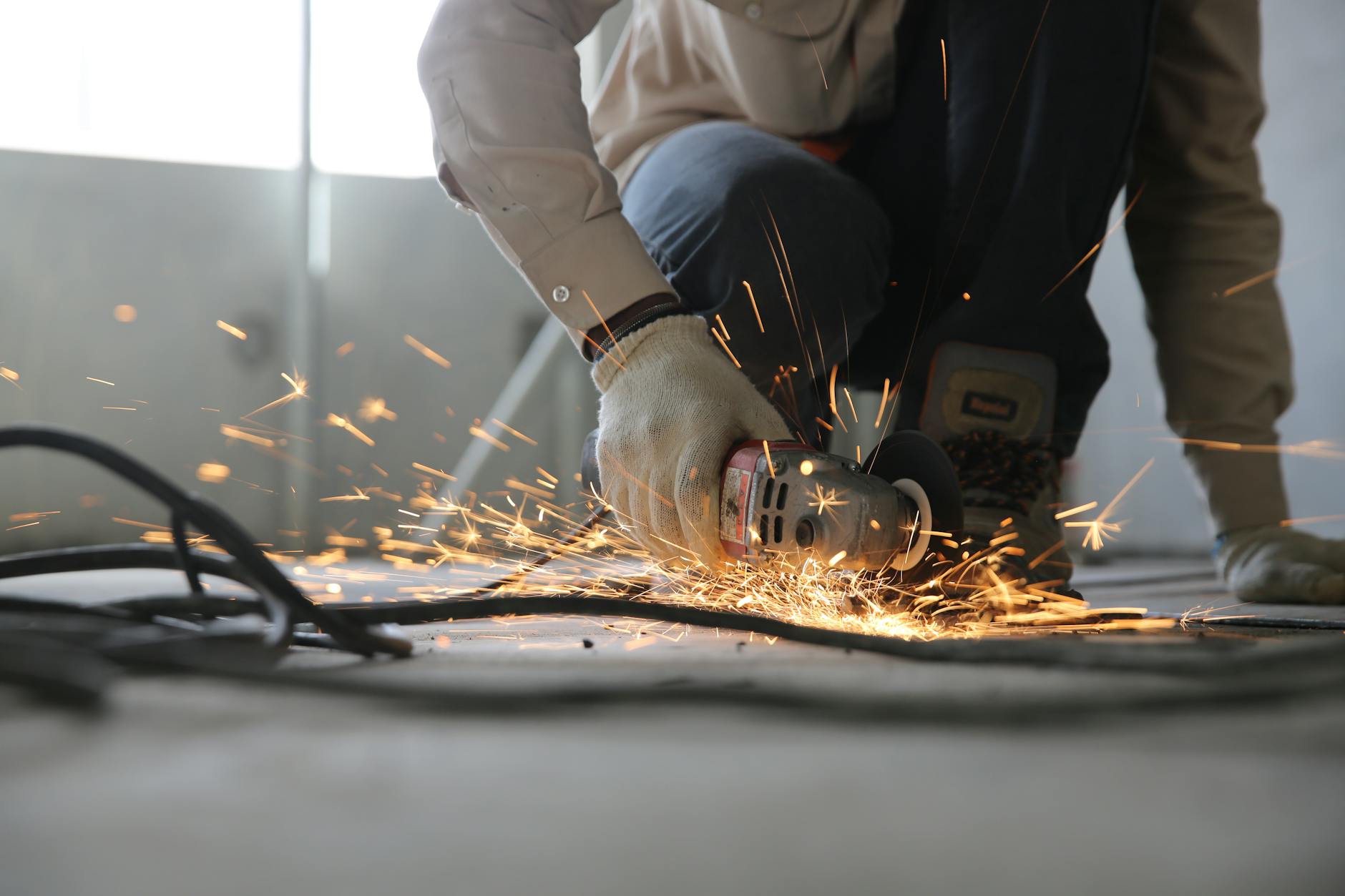
Hazard Hierarchy of Control | Free Download PPT
Introduction to Hazard Control
In any workplace, safety is paramount. Whether you’re working in construction, manufacturing, or even an office setting, hazards can pose risks to health and well-being. That’s where hazard control steps in, a systematic approach to managing workplace dangers.
Why is Hazard Control Important?
Hazard control minimizes the risk of injuries, illnesses, and even fatalities. Think of it as a safety net designed to protect not just individuals but the entire workforce.
The Role of Safety in Hazard Management
Safety isn’t just a checkbox on a compliance list—it’s a culture. When employers and employees actively engage in hazard management, workplaces become more productive and harmonious.
What is the Hazard Hierarchy of Control?
The hazard hierarchy of control is a framework that categorizes and prioritizes control measures to mitigate risks effectively.
Definition and Purpose
The hierarchy outlines five levels of control strategies, ranked from the most effective to the least effective. Its purpose? To systematically reduce workplace risks.
The Structure of the Hierarchy
At the top lies elimination—the most effective measure—while personal protective equipment (PPE) sits at the bottom, acting as the last line of defense.
The Five Levels of the Hazard Hierarchy of Control
Elimination: The Gold Standard
Elimination involves removing the hazard entirely. If a piece of faulty machinery is a hazard, replacing it or removing it eliminates the risk altogether.
Examples of Elimination in the Workplace
Consider redesigning a workspace to remove sharp edges or replacing a hazardous chemical with a non-toxic alternative.
Challenges in Implementing Elimination
While ideal, elimination isn’t always feasible, especially in industries with inherent risks, such as mining or construction.
Substitution: Replacing the Risk
If elimination isn’t possible, substitution steps in. This involves replacing a high-risk element with a less dangerous alternative.
Practical Substitution Methods
For instance, replacing a solvent-based paint with a water-based one reduces exposure to harmful fumes.
Limitations of Substitution
Substitutes may still pose risks, albeit reduced, and may not always be as effective in functionality.
Engineering Controls: Designing for Safety
Engineering controls focus on isolating people from hazards through design solutions.
How Engineering Controls Work
This could involve installing machine guards or creating enclosed spaces for hazardous processes.
Real-World Applications
Think of ventilation systems in chemical labs—they remove harmful fumes and ensure clean air.
Administrative Controls: Rules and Training
Administrative controls revolve around creating policies and providing training to mitigate risks.
Developing Effective Policies
Policies like limiting the number of hours for hazardous tasks can reduce exposure.
Training and Awareness Programs
Regular safety drills and hazard awareness training empower employees to act responsibly.
Personal Protective Equipment (PPE): The Last Line of Defense
PPE is the go-to when other measures can’t fully eliminate risks.
Types of PPE and Their Uses
Helmets, gloves, safety goggles—each piece of PPE is tailored to protect against specific hazards.
Limitations of PPE in Hazard Control
PPE doesn’t eliminate hazards; it merely reduces exposure, making it less reliable compared to other controls
Hazard Hierarchy of Control: A Comprehensive Guide
The Hazard Hierarchy of Control is a systematic approach used in workplace safety to eliminate or reduce risks. It prioritizes hazard control methods from the most effective to the least effective. This framework ensures worker safety by addressing hazards at their source whenever possible. Below is an explanation of the hierarchy’s levels:
1. Elimination (Most Effective)
Definition: Completely removing the hazard from the workplace.
Example: Using automated machinery to eliminate the need for manual handling of hazardous substances.
Elimination is the most effective control method as it removes the hazard entirely, leaving no residual risk.
2. Substitution
Definition: Replacing a hazardous material or process with a less dangerous one.
Example: Switching from a toxic solvent to a non-toxic alternative in cleaning operations.
Substitution minimizes the risk but still requires careful evaluation to ensure the replacement does not introduce new hazards.
3. Engineering Controls
Definition: Isolating workers from the hazard through physical changes to the workplace or equipment.
Example: Installing ventilation systems to remove harmful fumes or enclosing noisy machinery.
These controls aim to create a safer environment without relying on worker behavior.
4. Administrative Controls
Definition: Changing work procedures or policies to reduce exposure to hazards.
Example: Rotating shifts to limit individual exposure time to hazardous environments or conducting safety training sessions.
Administrative controls are less effective because they rely on consistent adherence by employees.
5. Personal Protective Equipment (PPE) (Least Effective)
Definition: Providing workers with gear to protect against hazards.
Example: Gloves, safety goggles, helmets, and respirators.
PPE should be considered a last resort because it does not eliminate the hazard and requires proper use and maintenance.
The Pyramid of Control
The hierarchy is often depicted as a pyramid to emphasize the effectiveness of each control measure. The higher up in the pyramid, the more effective and reliable the control.
Level | Examples | Effectiveness |
---|---|---|
1. Elimination | Remove a dangerous machine | High |
2. Substitution | Replace lead-based paint | High |
3. Engineering | Guardrails on walkways | Moderate |
4. Administrative | Training and procedures | Low |
5. PPE | Hard hats and gloves | Lowest |
Key Takeaways
- Always aim for Elimination or Substitution as the first steps.
- Use Engineering Controls to minimize hazard interaction.
- Apply Administrative Controls and PPE only as supplementary measures.
- Combining controls can enhance safety and effectiveness.
By following the Hazard Hierarchy of Control, organizations can systematically reduce risks and ensure a safer workplace.
Benefits of Implementing the Hazard Hierarchy of Control
Reduced Workplace Injuries and Illnesses
Effective implementation drastically cuts down workplace incidents, fostering a safer environment.
Increased Productivity and Morale
When employees feel safe, their focus and efficiency skyrocket, boosting overall productivity.
Challenges in Adopting the Hierarchy of Control
Overcoming Resistance to Change
Employees and employers may resist changes, especially when they perceive them as inconvenient or costly.
Balancing Costs and Benefits
Some control measures require significant investment, which can be a hurdle for small businesses.
Conclusion
The hazard hierarchy of control is not just a guideline—it’s a life-saving framework. By prioritizing higher-level controls like elimination and substitution, workplaces can significantly mitigate risks, ensuring the safety of everyone involved.
Importance of HIRA (Hazard Identification and Risk Assessment)
Steps of HIRA (Hazard Identification and Risk Assessment)
Components of HIRA (Hazard Identification and Risk Assessment)
What is HIRA?: Hazard Identification and Risk Assessment
Difference Between HIRA and JSA | Explained with Example | Free Download PPT
FAQs
What is the primary goal of the hazard hierarchy of control?
The main goal is to minimize workplace risks systematically, starting with the most effective controls.
Which control method is considered the most effective?
Elimination is the most effective, as it removes the hazard entirely.
How can small businesses implement the hierarchy effectively?
Start with low-cost measures like administrative controls and gradually invest in higher-level solutions.
Are there industries where this hierarchy is not applicable?
The hierarchy applies to almost all industries, but its application may vary based on specific risks.
How often should hazard control measures be reviewed?
Hazard controls should be reviewed regularly—at least annually or whenever there are significant changes in operations.