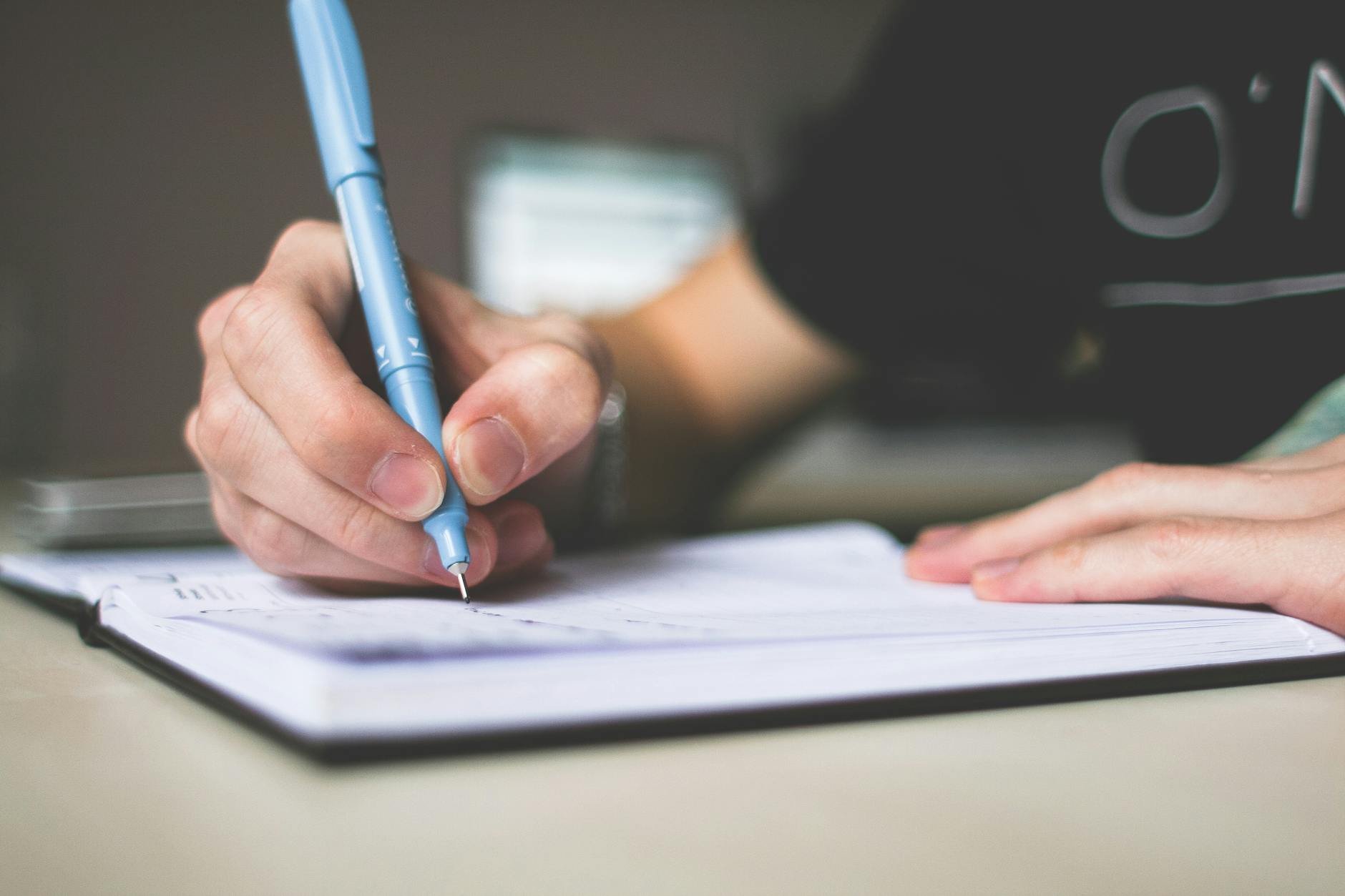
Steps of HIRA (Hazard Identification and Risk Assessment)
Introduction
When it comes to workplace safety, no system is more fundamental than HIRA—Hazard Identification and Risk Assessment. It serves as a cornerstone for protecting employees and ensuring smooth operations. But what exactly is HIRA, and why is it so vital? Let’s break it down step by step.
Understanding the Basics of HIRA
Definition of HIRA
HIRA stands for Hazard Identification and Risk Assessment, a systematic process used to identify potential hazards in the workplace, assess their associated risks, and implement measures to mitigate them. It combines proactive strategies to prevent accidents and foster a safe working environment.
Why HIRA is Crucial in the Workplace
HIRA isn’t just about ticking a compliance box—it’s about saving lives. By identifying potential dangers and addressing them before they become issues, businesses can safeguard their workforce. Moreover, it ensures adherence to legal and regulatory standards, minimizing the risk of hefty penalties.
Steps of HIRA
Step 1: Identifying Hazards
The first step in HIRA is recognizing potential hazards. A hazard is anything with the potential to cause harm, whether it’s a piece of equipment, a chemical substance, or a poorly designed process.
Methods to Identify Hazards:
- Conducting workplace inspections.
- Consulting employees who interact with machinery or materials.
- Reviewing incident and accident reports.
Step 2: Assessing Risks
Risk assessment involves determining the likelihood of a hazard causing harm and the severity of its potential impact.
Tools for Risk Assessment:
- Risk matrices.
- Probability and impact scales.
Step 3: Analyzing Risks
This step focuses on evaluating the relationship between the likelihood of an incident and its consequences. A commonly used approach is the Likelihood vs. Severity Matrix, which categorizes risks into low, medium, and high.
Step 4: Evaluating Risks
Risk evaluation determines whether identified risks are acceptable or require intervention. This involves applying frameworks like ALARP (As Low As Reasonably Practicable) to decide the extent of necessary controls.
Step 5: Implementing Controls
The final step is to apply control measures to eliminate or reduce risks. The Hierarchy of Controls is a guiding principle:
- Eliminate the hazard.
- Substitute with a less hazardous option.
- Implement engineering controls.
- Apply administrative controls.
- Use personal protective equipment (PPE).
Tools and Techniques Used in HIRA
Common Tools for Hazard Identification
- Checklists: Standardized forms to ensure all potential hazards are considered.
- Software Solutions: Platforms designed for advanced hazard tracking and risk analysis.
Techniques for Risk Assessment
- Job Safety Analysis (JSA): Breaks tasks into steps to identify risks.
- Fault Tree Analysis (FTA): A visual tool to trace root causes of failures.
Challenges in Conducting HIRA
Inadequate Data Collection
Without accurate data, even the best risk assessments can fail. It’s crucial to ensure all relevant information is gathered, whether it’s historical incident records or real-time observations.
Resistance to Change
Employees may resist adopting new safety practices. Overcoming this requires effective communication and training.
Benefits of Conducting HIRA
Improved Workplace Safety
With HIRA in place, businesses experience fewer accidents, ensuring a healthier and more productive workforce.
Legal Compliance
Regular HIRA helps organizations meet local and international safety standards, avoiding legal repercussions.
Steps of HIRA (Hazard Identification and Risk Assessment)
HIRA, or Hazard Identification and Risk Assessment, is a structured approach used in workplaces to identify potential hazards, evaluate associated risks, and implement measures to mitigate them. Below are the detailed steps involved in HIRA:
1. Establish the Context
- Define Objectives: Identify why the HIRA is being conducted (e.g., compliance, safety improvement).
- Determine Scope: Outline the areas, processes, or tasks to be assessed.
- Gather Information: Collect data about the workplace, equipment, processes, materials, and workforce.
2. Hazard Identification
- Inspect the Workplace: Conduct a physical walkthrough to identify hazards in the environment, equipment, and operations.
- Classify Hazards: Categorize hazards as physical, chemical, biological, ergonomic, or psychosocial.
- Engage the Workforce: Consult employees and supervisors to uncover hazards based on their experience.
- Review Past Incidents: Analyze previous accidents, near misses, and safety reports.
3. Risk Assessment
- Evaluate Likelihood: Determine how probable it is for a hazard to cause harm.
- Assess Severity: Assess the potential impact or severity of the harm.
- Calculate Risk Level: Use a risk matrix or formula (Risk = Likelihood × Severity) to prioritize hazards.
- Consider Exposure: Take into account the frequency and duration of exposure to the hazard.
4. Risk Control
- Apply the Hierarchy of Controls:
- Elimination: Remove the hazard entirely.
- Substitution: Replace the hazard with something less dangerous.
- Engineering Controls: Implement physical changes to isolate or reduce the hazard.
- Administrative Controls: Modify procedures, training, or policies to reduce exposure.
- Personal Protective Equipment (PPE): Use as a last resort to protect workers.
- Document Controls: Ensure all control measures are recorded for accountability.
5. Monitor and Review
- Regular Inspections: Continuously monitor the effectiveness of implemented controls.
- Update HIRA: Revise the assessment when new hazards emerge, equipment changes, or after incidents.
- Feedback Mechanism: Involve employees in ongoing safety evaluations and encourage reporting.
6. Communication and Training
- Share Findings: Communicate hazards, risks, and control measures with the workforce.
- Provide Training: Equip employees with the skills and knowledge to recognize and handle hazards safely.
By following these steps, organizations can systematically identify hazards, assess risks, and implement appropriate controls, creating a safer work environment.
Conclusion
HIRA is more than a process; it’s a commitment to creating a safe and thriving workplace. By identifying hazards, assessing risks, and implementing effective controls, businesses can protect their most valuable asset: their people.
What is HIRA?: Hazard Identification and Risk Assessment
Difference Between HIRA and JSA | Explained with Example | Free Download PPT
Risk Assessment vs Job Safety Analysis
What are the 5 Steps of a JSA?
5 Step Process of Risk Assessment
FAQs
- What industries benefit the most from HIRA?
Industries like construction, manufacturing, and oil & gas gain significant advantages from HIRA. - How often should HIRA be conducted?
Ideally, it should be done annually or whenever there are changes to the work environment. - Who is responsible for carrying out HIRA?
Safety officers and management teams typically oversee the process, often involving employee input. - What are the consequences of skipping HIRA?
Increased accidents, legal penalties, and a tarnished reputation. - Can HIRA be customized for small businesses?
Absolutely! Scaled-down versions of HIRA are equally effective for smaller setups.