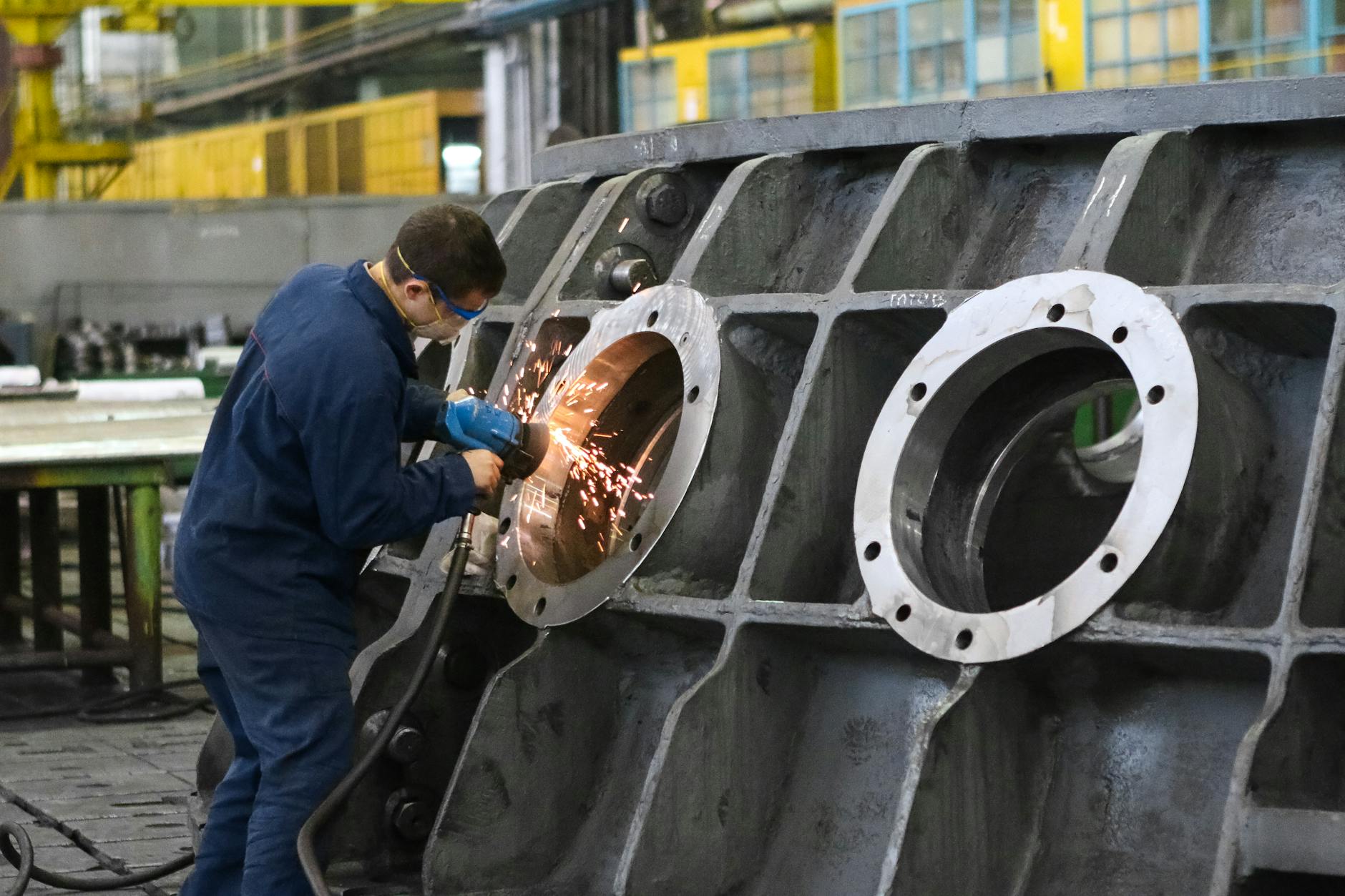
Machine Guarding and Safety
Machine guarding plays a crucial role in ensuring workplace safety across various industries. In an industrial setting, where machinery is a common sight, the risk of accidents is ever-present. However, with proper machine guarding measures in place, these risks can be significantly mitigated, protecting both employees and equipment.
Introduction to Machine Guarding
Importance of Machine Guarding
Machine guarding is essential for preventing accidents and injuries caused by moving parts, flying debris, and other hazards associated with machinery operation. Without adequate guarding, workers are exposed to serious risks, including amputations, crush injuries, and even fatalities.
Statistics on Workplace Accidents Related to Machinery
According to the Occupational Safety and Health Administration (OSHA), approximately 18,000 amputations, lacerations, and crushing injuries occur annually in the United States due to inadequate machine guarding. These incidents not only result in human suffering but also incur significant financial costs for businesses in terms of medical expenses, litigation, and lost productivity.
Types of Machine Guarding
There are various types of machine guarding systems designed to protect workers from different types of hazards:
Fixed Guards
Fixed guards are physical barriers that are permanently attached to the machinery, preventing access to hazardous areas during operation.
Interlocked Guards
Interlocked guards are designed to stop the machine’s operation when the guard is opened or removed, ensuring that workers cannot access the danger zone while the machine is in use.
Adjustable Guards
Adjustable guards can be customized to fit different types of machinery and can be repositioned as needed to provide adequate protection.
Presence-Sensing Devices
Presence-sensing devices use sensors to detect the presence of a worker within the danger zone and automatically stop the machine to prevent accidents.
Two-Hand Tripping Devices
Two-hand tripping devices require operators to use both hands to activate the machine, ensuring that their hands are clear of the danger zone before the machine starts.
Regulatory Requirements for Machine Guarding
Regulatory agencies such as OSHA and the International Organization for Standardization (ISO) have established guidelines and standards for machine guarding to ensure workplace safety. Employers are required to comply with these regulations to protect their employees from hazards associated with machinery operation.
Common Hazards Associated with Machines
Machinery poses various hazards to workers, including:
Entanglement Hazards
Moving parts such as gears, belts, and chains can entangle workers, leading to severe injuries or death.
Crushing Hazards
Machines with moving parts or heavy components can crush workers’ limbs or bodies if proper safeguards are not in place.
Impact Hazards
Objects ejected from machines during operation can strike workers, causing injuries ranging from bruises to concussions.
Ejection Hazards
High-speed machinery can eject materials or debris, posing a risk of injury to nearby workers.
Cutting Hazards
Sharp blades or cutting tools can cause lacerations or amputations if workers come into contact with them during operation.
Principles of Effective Machine Guarding
To ensure the effectiveness of machine guarding systems, employers should follow these principles:
Risk Assessment
Identify potential hazards associated with each machine and assess the level of risk to determine the appropriate guarding measures.
Guard Design and Selection
Select guards that are suitable for the specific hazards present in the workplace and ensure they are properly designed to prevent access to danger zones.
Proper Installation and Maintenance
Install guards according to manufacturer’s specifications and regularly inspect them for damage or wear. Replace or repair guards as needed to maintain their effectiveness.
Employee Training
Provide comprehensive training to employees on the hazards associated with machinery operation and the importance of following safety protocols and using guarding devices correctly.
Benefits of Proper Machine Guarding
Implementing proper machine guarding measures offers several benefits:
Reduction in Workplace Accidents
By preventing access to hazardous areas and controlling exposure to moving parts, machine guarding helps reduce the risk of accidents and injuries in the workplace.
Compliance with Regulations
Complying with regulatory requirements for machine guarding not only protects workers but also helps businesses avoid fines and penalties for non-compliance.
Preservation of Equipment and Assets
Properly guarded machines are less likely to experience breakdowns or damage, leading to lower maintenance costs and longer equipment lifespan.
Challenges in Implementing Machine Guarding
Despite the clear benefits of machine guarding, businesses may face challenges in implementing effective guarding systems:
Cost Considerations
Investing in machine guarding equipment and systems can be costly, especially for small businesses with limited budgets.
Resistance to Change
Some workers may resist the implementation of machine guarding measures, viewing them as cumbersome or inconvenient.
Lack of Awareness
Employers and employees may lack awareness of the importance of machine guarding or the specific hazards present in their workplace.
Conclusion
Machine guarding is a critical component of workplace safety, protecting workers from serious injuries and preventing costly accidents. By understanding the importance of machine guarding, complying with regulations, and investing in effective guarding systems, businesses can create safer work environments for their employees and reduce the risk of accidents and injuries.
Chemical Safety Engineer Salary
Chemical Engineer Safety Aspects
FAQs
- What is machine guarding? Machine guarding refers to the use of physical barriers, devices, and safety controls to protect workers from hazardous machinery during operation.
- Why is machine guarding important? Machine guarding is important because it helps prevent accidents and injuries caused by moving parts, flying debris, and other hazards associated with machinery operation.
- What are the regulatory requirements for machine guarding? Regulatory agencies such as OSHA and ISO have established guidelines and standards for machine guarding to ensure workplace safety.
- What are some common hazards associated with machines? Common hazards associated with machines include entanglement hazards, crushing hazards, impact hazards, ejection hazards, and cutting hazards.
- How can businesses overcome challenges in implementing machine guarding? Businesses can overcome challenges in implementing machine guarding by addressing cost considerations, addressing resistance to change, and increasing awareness through employee training and education.