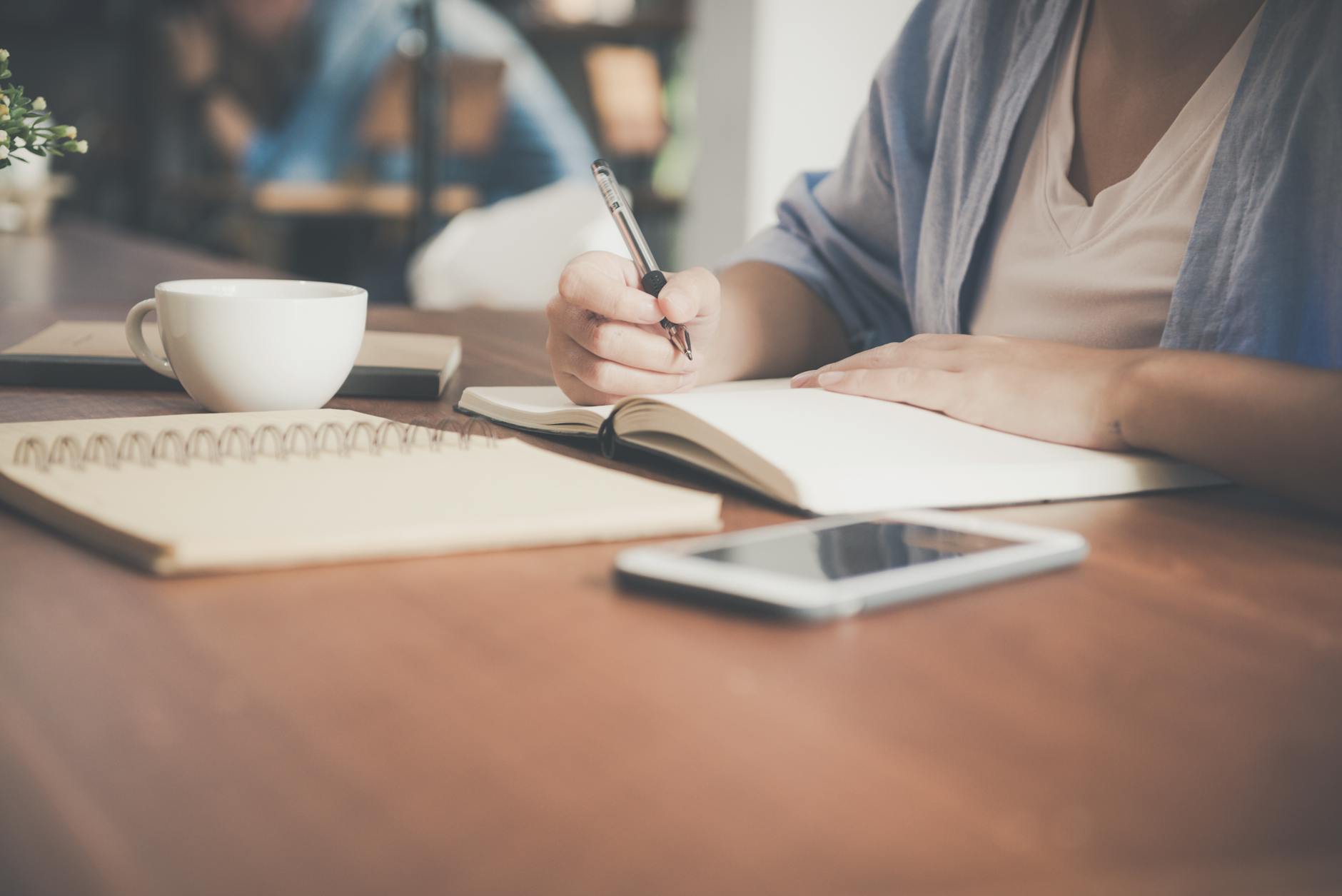
Introduction to Kaizen 5S
In the realm of continuous improvement methodologies, Kaizen stands as a beacon of efficiency and productivity. Kaizen, a Japanese term meaning “change for better,” emphasizes small, incremental changes that lead to significant improvements over time. Within the framework of Kaizen, the 5S methodology plays a crucial role in optimizing workplace organization and efficiency.
Understanding Kaizen Methodology
What is Kaizen?
Kaizen is a philosophy centered on the concept of continuous improvement. It advocates for ongoing efforts to enhance processes, products, or services incrementally. Rooted in the Japanese culture, Kaizen encourages every employee, from top management to frontline workers, to contribute ideas for improvement.
What is 5S?
5S is a systematic approach to workplace organization derived from Japanese terms: Seiri (Sort), Seiton (Set in Order), Seiso (Shine), Seiketsu (Standardize), and Shitsuke (Sustain). The 5S methodology aims to create a clean, organized, and efficient work environment, thereby improving safety, quality, and productivity.
The Importance of Kaizen 5S in Business
Kaizen 5S is instrumental in promoting a culture of continuous improvement within organizations. By fostering discipline, teamwork, and attention to detail, it enables companies to streamline processes, reduce waste, and enhance overall performance.
The 5S Principles Explained
Sort (Seiri)
Sorting involves eliminating unnecessary items from the workplace, keeping only the essentials. It helps declutter workspaces, making it easier to locate tools, materials, and information.
Set in Order (Seiton)
Setting in order focuses on arranging essential items in a logical and efficient manner. By assigning specific locations for tools and supplies, Seiton minimizes wasted time searching for items and promotes a more organized workflow.
Shine (Seiso)
Shining refers to keeping the workplace clean and free of debris. Regular cleaning and maintenance activities not only improve aesthetics but also prevent safety hazards and equipment malfunctions.
Standardize (Seiketsu)
Standardizing involves establishing standardized processes and procedures for maintaining cleanliness and organization. It ensures consistency and sustainability of the 5S practices across the organization.
Sustain (Shitsuke)
Sustaining entails fostering a culture of continuous improvement and accountability. It involves training employees, conducting regular audits, and reinforcing 5S principles to maintain long-term success.
Benefits of Implementing Kaizen 5S
The implementation of Kaizen 5S offers numerous benefits to businesses, including:
- Enhanced efficiency and productivity
- Improved workplace safety
- Reduced waste and costs
- Increased employee morale and engagement
- Better quality control and customer satisfaction
Steps to Implement Kaizen 5S in Your Workplace
Implementing Kaizen 5S involves the following steps:
Getting Started
- Gain leadership support and commitment.
- Form a cross-functional team.
- Set clear objectives and goals.
Sorting
- Identify and remove unnecessary items.
- Classify essential items based on frequency of use.
- Implement visual management techniques.
Setting in Order
- Designate specific locations for tools and supplies.
- Arrange items based on workflow and frequency of use.
- Utilize labeling and signage for easy identification.
Shining
- Establish cleaning schedules and responsibilities.
- Conduct regular inspections to maintain cleanliness.
- Address cleanliness issues promptly.
Standardizing
- Develop standardized procedures for 5S activities.
- Create visual aids and checklists for guidance.
- Train employees on 5S principles and expectations.
Sustaining
- Foster a culture of continuous improvement.
- Provide ongoing training and support.
- Recognize and reward employees for adherence to 5S practices.
Examples of Successful Kaizen 5S Implementations
Numerous organizations have successfully implemented Kaizen 5S to improve efficiency and productivity. For example:
- Toyota adopted 5S principles in its manufacturing processes, leading to significant improvements in quality and efficiency.
- Boeing implemented 5S practices in its assembly plants, resulting in reduced production time and increased safety.
Challenges in Implementing Kaizen 5S
While implementing Kaizen 5S offers many benefits, organizations may encounter challenges such as:
- Resistance to change from employees accustomed to existing work practices.
- Lack of management support and commitment.
- Difficulty in sustaining 5S practices over the long term.
Tips for Overcoming Kaizen 5S Implementation Challenges
To overcome challenges in implementing Kaizen 5S, organizations can:
- Communicate the benefits of 5S to employees and stakeholders.
- Provide training and support to ensure buy-in from all levels of the organization.
- Lead by example and demonstrate commitment to 5S principles.
- Continuously monitor and adjust 5S practices based on feedback and performance metrics.
Monitoring and Measuring the Success of Kaizen 5S
Monitoring and measuring the success of Kaizen 5S involves:
- Tracking key performance indicators such as productivity, quality, and safety.
- Conducting regular audits to assess adherence to 5S principles.
- Soliciting feedback from employees and stakeholders to identify areas for improvement.
Continuous Improvement and Kaizen 5S
Kaizen 5S is not a one-time activity but an ongoing process of continuous improvement. By continually refining processes and practices, organizations can achieve higher levels of efficiency, quality, and customer satisfaction.
Kaizen 5S in Various Industries
Kaizen 5S principles are applicable across various industries, including manufacturing, healthcare, hospitality, and service sectors. Regardless of the industry, the fundamental principles of 5S—Sort, Set in Order, Shine, Standardize, and Sustain—can drive positive change and improvement.
Case Studies of Kaizen 5S Success Stories
Several case studies illustrate the effectiveness of Kaizen 5S in different settings. For instance:
- A hospital implemented 5S practices in its operating rooms, resulting in reduced surgical errors and improved patient outcomes.
- A retail store adopted 5S principles in its inventory management, leading to reduced stockouts and improved customer satisfaction.
Conclusion
Kaizen 5S is a powerful tool for enhancing efficiency, productivity, and quality in the workplace. By embracing the principles of Sort, Set in Order, Shine, Standardize, and Sustain, organizations can create a culture of continuous improvement that drives success in today’s competitive business environment.
Mobile Equipment Safety: Prioritizing Operator Training and Maintenance Practices
Zero Harm Culture: Nurturing a Safety Mindset in the Workplace
Chemical Hygiene in Laboratories: Promoting Safe Handling and Storage Practices
Radiation Monitoring: Safeguarding Environments through Dosimetry and Contamination Control
FAQs on Kaizen 5S
- What are the primary objectives of implementing Kaizen 5S?
- The primary objectives of implementing Kaizen 5S include improving efficiency, enhancing workplace safety, reducing waste, standardizing processes, and fostering a culture of continuous improvement.
- How can organizations overcome resistance to change when implementing Kaizen 5S?
- Organizations can overcome resistance to change by involving employees in the process, providing training and support, communicating the benefits of 5S, leading by example, and addressing concerns or objections proactively.
- What role does leadership play in the successful implementation of Kaizen 5S?
- Leadership plays a crucial role in the successful implementation of Kaizen 5S by providing vision, direction, and support. Leaders should demonstrate commitment to 5S principles, allocate resources, empower employees, and facilitate a culture of continuous improvement.
- How often should organizations conduct audits of their 5S practices?
- Organizations should conduct regular audits of their 5S practices to ensure compliance and identify areas for improvement. The frequency of audits may vary depending on factors such as the size of the organization, the complexity of operations, and the maturity of the 5S program.
- Can Kaizen 5S principles be applied to non-manufacturing industries?
- Yes, Kaizen 5S principles can be applied to non-manufacturing industries such as healthcare, retail, hospitality, and service sectors. Regardless of the industry, the fundamental principles of Sort, Set in Order, Shine, Standardize, and Sustain can improve efficiency, productivity, and quality.