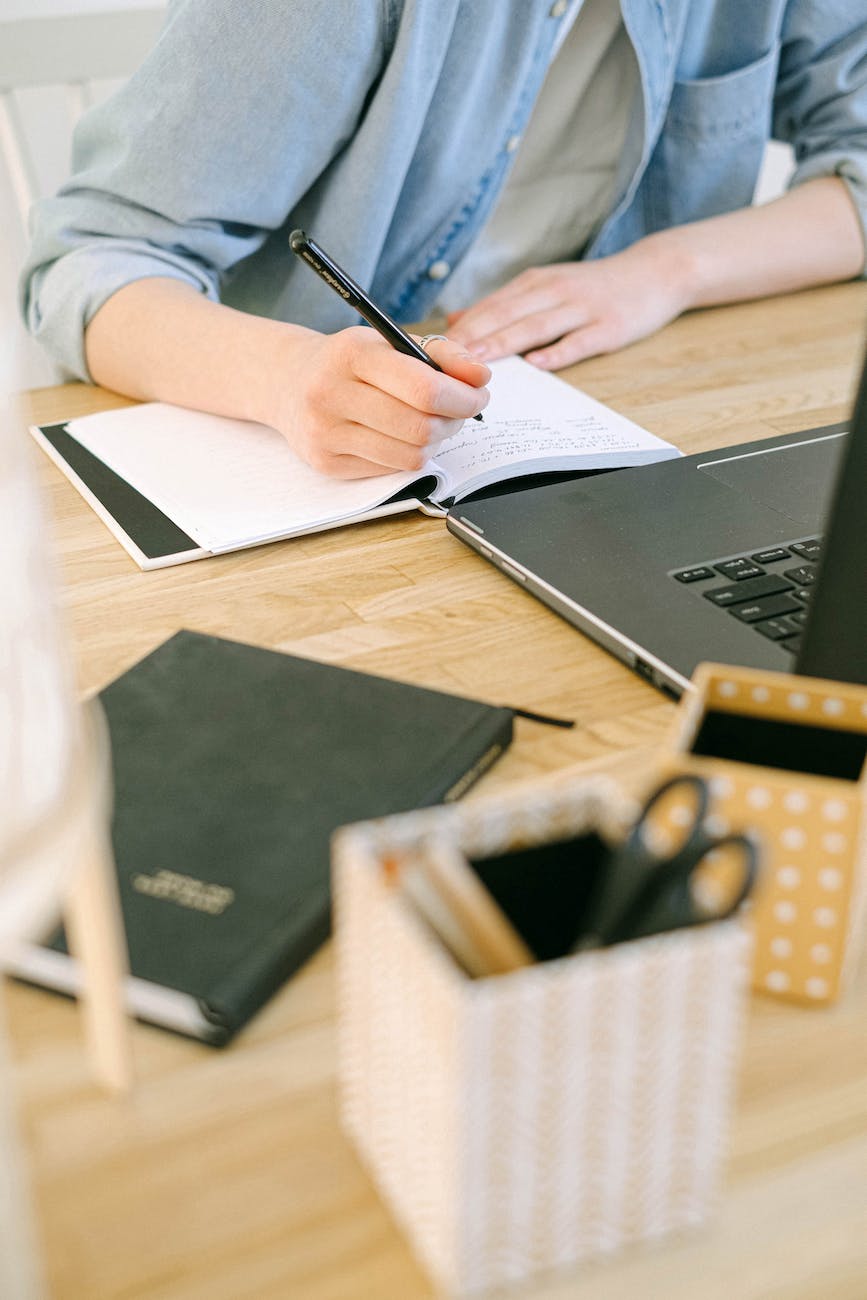
Job Hazard Analysis (JHA): Identifying and Eliminating Worksite Risks
Introduction
A proactive approach to workplace safety involves identifying and mitigating potential risks through comprehensive assessments. Job Hazard Analysis (JHA), also known as Job Safety Analysis (JSA), is a systematic process designed to evaluate tasks, identify hazards, and eliminate or control risks. This article delves into the significance of JHA in safeguarding workplaces and outlines the steps organizations can take to conduct effective hazard analyses.
Understanding Job Hazard Analysis (JHA)
- Definition and Purpose
- Definition: JHA is a structured process that involves breaking down a job into individual tasks, identifying potential hazards, and implementing controls to minimize or eliminate risks.
- Purpose: The primary goal of JHA is to enhance workplace safety by preventing accidents and injuries through proactive hazard identification.
- Key Components of JHA
- Task Identification: Breaking down a job into specific tasks to analyze each step individually.
- Hazard Identification: Identifying potential hazards associated with each task.
- Risk Assessment: Evaluating the severity and likelihood of identified hazards.
- Control Measures: Implementing controls to eliminate or minimize risks.
Steps in Conducting Job Hazard Analysis
- Selecting Jobs for Analysis
- Prioritization: Identifying jobs with higher risk levels or those with a history of incidents for analysis.
- Involving Employees: Consulting workers to gain insights into potential hazards in their respective tasks.
- Breaking Down Jobs into Tasks
- Task Identification: Listing each step involved in a job.
- Sequencing Tasks: Organizing tasks in the order they occur during job execution.
- Identifying Potential Hazards
- Physical Hazards: Identifying dangers related to machinery, equipment, or workplace layout.
- Chemical Hazards: Assessing risks associated with exposure to chemicals.
- Biological Hazards: Recognizing potential risks from biological agents.
- Ergonomic Hazards: Evaluating risks related to poor workstation design or repetitive tasks.
- Assessing Risks
- Severity and Likelihood: Assigning a rating to the severity and likelihood of each identified hazard.
- Risk Matrix: Using a risk matrix to prioritize hazards based on their potential impact.
- Implementing Controls
- Elimination: Completely removing the hazard if possible.
- Substitution: Replacing the hazard with a less risky alternative.
- Engineering Controls: Modifying equipment or processes to minimize risks.
- Administrative Controls: Introducing procedures or policies to reduce exposure.
- Personal Protective Equipment (PPE): Providing appropriate PPE as a last line of defense.
- Documenting and Communicating Findings
- Written Documentation: Creating a detailed report outlining identified hazards, risks, and control measures.
- Communication: Sharing findings with employees and relevant stakeholders.
- Training: Ensuring that workers are educated on the identified risks and control measures.
Benefits of Job Hazard Analysis
- Prevention of Accidents and Injuries
- JHA helps organizations proactively identify and eliminate potential hazards, reducing the likelihood of accidents and injuries.
- Enhanced Employee Involvement
- Involving employees in the JHA process fosters a culture of safety and encourages workers to actively contribute to identifying risks in their tasks.
- Regulatory Compliance
- Conducting JHA ensures compliance with occupational health and safety regulations, demonstrating a commitment to maintaining a safe work environment.
- Improved Efficiency
- By identifying and mitigating risks, JHA can lead to more efficient and streamlined work processes, enhancing overall workplace productivity.
Conclusion
Job Hazard Analysis is a powerful tool that empowers organizations to systematically identify, assess, and control workplace risks. By breaking down jobs into tasks, analyzing potential hazards, and implementing effective controls, employers can create safer work environments, protect their workforce, and ensure regulatory compliance. Embracing a proactive approach through JHA contributes to a culture of safety and fosters continuous improvement in occupational health and safety practices.
How to Validate Root Cause in Six Sigma
Root Cause Analysis Tools in Six Sigma
Process of Root Cause Analysis
Frequently Asked Questions (FAQs)
- What is Job Hazard Analysis (JHA), and why is it important?
- JHA is a systematic process for identifying and eliminating or controlling workplace hazards. It is important for preventing accidents, enhancing employee involvement in safety, and ensuring regulatory compliance.
- What are the key components of JHA?
- Key components include task identification, hazard identification, risk assessment, and the implementation of control measures.
- What are the steps involved in conducting Job Hazard Analysis?
- Steps include selecting jobs for analysis, breaking down jobs into tasks, identifying potential hazards, assessing risks, implementing controls, and documenting and communicating findings.
- What are the benefits of Job Hazard Analysis?
- Benefits include the prevention of accidents and injuries, enhanced employee involvement in safety, regulatory compliance, and improved overall workplace efficiency.