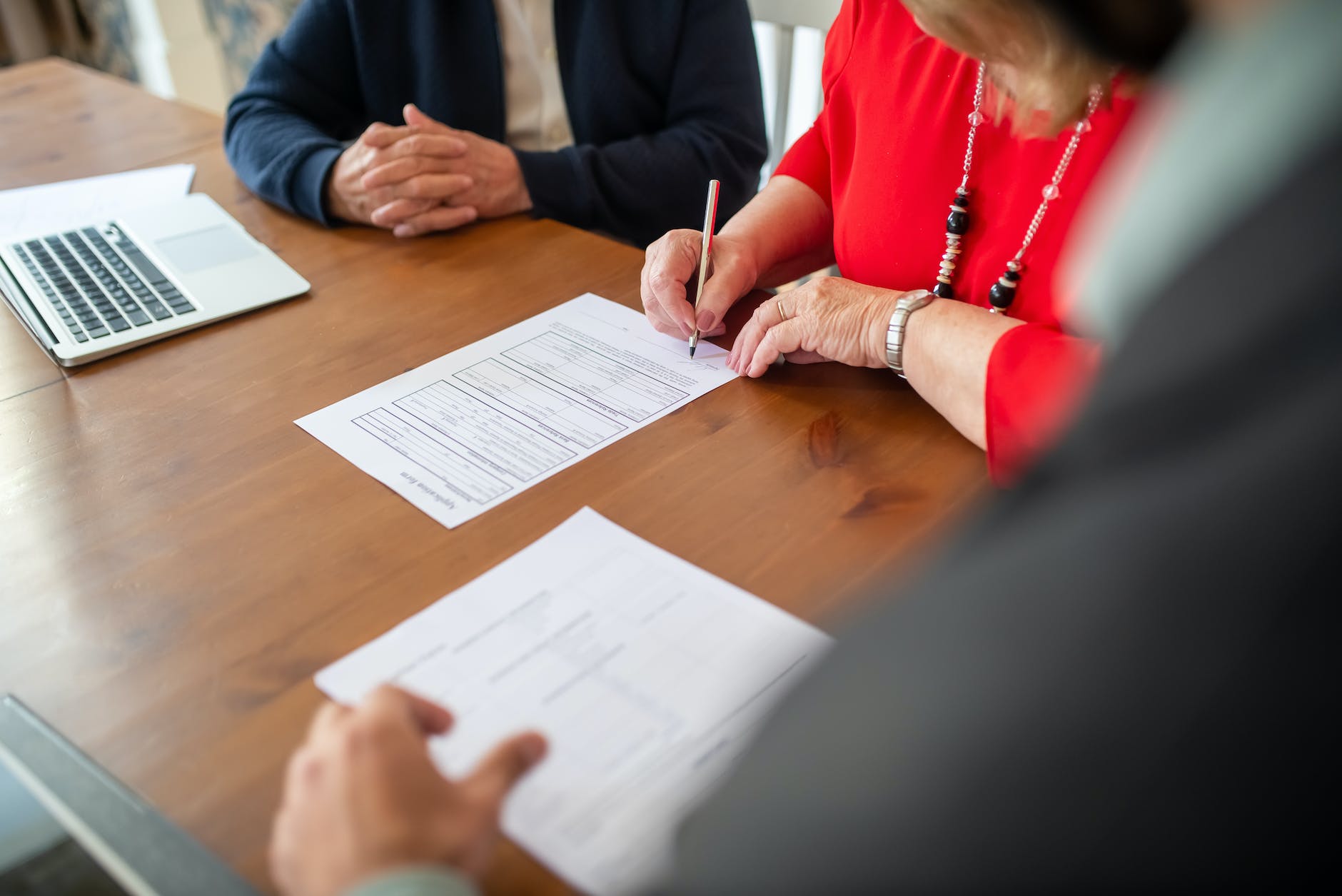
Safety Instrumented Systems (SIS): Design, Implementation, and Maintenance
Introduction
Safety Instrumented Systems (SIS) stand as crucial safeguards in industrial environments, designed to prevent and mitigate the impact of potentially hazardous incidents. Understanding the intricacies of SIS is essential for ensuring the safety and well-being of workers and assets.
Understanding Safety Instrumented Systems
Definition and Purpose of SIS
Safety Instrumented Systems (SIS) are engineered systems designed to monitor and respond to potentially dangerous situations. Their primary purpose is to reduce the risk of accidents and protect personnel, equipment, and the environment from harm.
Components of a Typical SIS
A standard SIS comprises various components, including sensors, logic solvers, and final elements such as valves or shutdown systems. Each component plays a vital role in the overall functionality of the system.
Designing Safety Instrumented Systems
Risk Assessment and SIL Determination
The design process of an SIS starts with a thorough risk assessment, identifying potential hazards and their consequences. Safety Integrity Level (SIL) determination assigns a measure of reliability to the system based on the assessed risk.
Selection of Appropriate SIS Architecture
Choosing the right architecture is crucial in designing an effective SIS. Whether it’s a simple system or a complex configuration, the architecture must align with the identified risks and safety requirements.
Implementation of Safety Instrumented Systems
Installation and Integration into Existing Processes
Implementing an SIS involves integrating it seamlessly into existing processes. This phase requires careful planning to minimize disruptions while enhancing overall safety.
Testing and Validation Procedures
Rigorous testing and validation are imperative to ensure the SIS functions as intended. Various scenarios, including normal operation and potential failure modes, should be simulated and validated to guarantee the reliability of the system.
Maintaining Safety Instrumented Systems
Regular Inspections and Diagnostics
Continuous monitoring through regular inspections and diagnostics is essential for the sustained effectiveness of an SIS. Identifying potential issues before they escalate is a key aspect of maintenance.
Upgrading and Adapting to Changing Needs
As industrial processes evolve, so do the risks associated with them. SIS must be adaptable, and safety engineers should regularly assess and upgrade systems to meet changing safety requirements.
Challenges in Safety Instrumented Systems
Common Challenges Faced During SIS Implementation
Implementing SIS comes with challenges such as system complexity, resistance to change, and potential integration issues. Safety engineers must navigate these challenges to ensure successful implementation.
Strategies for Overcoming SIS-Related Obstacles
Strategies for overcoming challenges include effective communication, thorough training programs, and collaboration with stakeholders. Safety engineers play a critical role in facilitating smooth SIS implementation.
Compliance with Industry Standards
Overview of Relevant Safety Standards
Adherence to industry safety standards is non-negotiable in SIS design and implementation. Safety engineers must stay informed about the latest standards to ensure compliance.
Ensuring Adherence to Regulatory Requirements
SIS must align with regulatory requirements to guarantee legal compliance. Safety engineers collaborate with regulatory bodies and internal stakeholders to ensure all standards are met.
Role of Safety Engineers in SIS
Responsibilities of Safety Engineers in SIS Design and Maintenance
Safety engineers bear the responsibility of designing, implementing, and maintaining effective SIS. Their expertise ensures that safety systems align with industry best practices and comply with regulations.
Collaboration with Other Departments
Effective SIS implementation requires collaboration across departments. Safety engineers work closely with operations, maintenance, and management to create a unified approach to safety.
Continuous Improvement in Safety Instrumented Systems
Feedback Mechanisms and Learning from Incidents
Establishing feedback mechanisms is essential for refining SIS. Safety engineers collect data, analyze incidents, and use feedback to continuously improve systems and address emerging risks.
Incorporating Advancements for Continuous Enhancement
Staying abreast of technological advancements is crucial for safety engineers. Continuous enhancement involves integrating new technologies and methodologies to keep SIS at the forefront of safety practices.
Safety Instrumented Systems (SIS) play a critical role in ensuring the safety and integrity of industrial processes across various sectors, including oil and gas, chemical, pharmaceuticals, and manufacturing. These systems are designed, implemented, and maintained with meticulous attention to detail to mitigate risks and prevent catastrophic incidents.
- Design of SIS: Designing a Safety Instrumented System involves a comprehensive analysis of the process hazards, risk assessment, and identification of safety functions. The design process typically follows international standards such as IEC 61511 and ANSI/ISA 84.01 to ensure compliance and effectiveness.
- Hazard and Risk Analysis: Conducting thorough hazard and risk assessments to identify potential hazards, assess their severity, and determine the required risk reduction targets.
- Safety Integrity Level (SIL) Determination: Assigning Safety Integrity Levels to safety functions based on the risk reduction required. SIL levels range from SIL 1 (lowest) to SIL 4 (highest).
- Functional Safety Requirements: Specifying the functional requirements of the SIS, including sensor selection, logic solver configuration, final element design, and communication protocols.
- Reliability and Availability Analysis: Evaluating the reliability and availability of SIS components to ensure that they meet the required safety standards.
- Implementation of SIS: The implementation phase involves the procurement, installation, configuration, and testing of the Safety Instrumented System components.
- Component Selection: Selecting appropriate sensors, logic solvers, final elements (such as valves or actuators), and other hardware components based on the specified requirements.
- Installation and Wiring: Installing SIS components according to manufacturer specifications and industry best practices, ensuring proper grounding, shielding, and segregation from other systems.
- Logic Configuration: Programming the logic solver (e.g., Safety PLC or Safety Relay) to execute the safety functions as per the safety requirements specification.
- Testing and Validation: Conducting functional testing, loop checks, and safety integrity tests to verify the performance and reliability of the SIS before it is put into service.
- Maintenance of SIS: Proper maintenance is essential to ensure the continued reliability and effectiveness of the Safety Instrumented System throughout its lifecycle.
- Routine Inspections: Performing regular inspections of SIS components, including sensors, actuators, and logic solvers, to detect any signs of degradation or malfunction.
- Calibration and Testing: Calibrating sensors and actuators as per the manufacturer’s recommendations and conducting periodic testing to ensure proper functionality.
- Software Updates and Upgrades: Keeping the SIS software up-to-date with the latest patches and upgrades to address security vulnerabilities and improve performance.
- Change Management: Implementing robust change management procedures to assess the impact of any modifications or alterations to the SIS and ensure that safety integrity is maintained.
In conclusion, the design, implementation, and maintenance of Safety Instrumented Systems require a systematic approach, adherence to international standards, and ongoing vigilance to mitigate risks and safeguard industrial processes and personnel from potential hazards.
Conclusion
In conclusion, Safety Instrumented Systems are indispensable components in ensuring industrial safety. The design, implementation, and maintenance of SIS require meticulous planning, continuous improvement, and the expertise of safety engineers.
Monthly Safety Committee Meeting Topics
Safety Committee Meeting Points
Safety Committee Roles and Responsibilities
FAQs
- What is the purpose of Safety Instrumented Systems?
- Safety Instrumented Systems are designed to monitor and respond to potentially dangerous situations, reducing the risk of accidents and protecting personnel, equipment, and the environment.
- How is the Safety Integrity Level (SIL) determined for an SIS?
- SIL determination involves a thorough risk assessment to assign a measure of reliability to the system based on the assessed risk of potential hazards.
- What are common challenges in implementing SIS?
- Common challenges include system complexity, resistance to change, and potential integration issues. Effective communication and collaboration are crucial for overcoming these challenges.
- How do safety engineers contribute to SIS design?
- Safety engineers play a pivotal role in designing, implementing, and maintaining effective SIS. Their expertise ensures that safety systems align with industry best practices and comply with regulations.