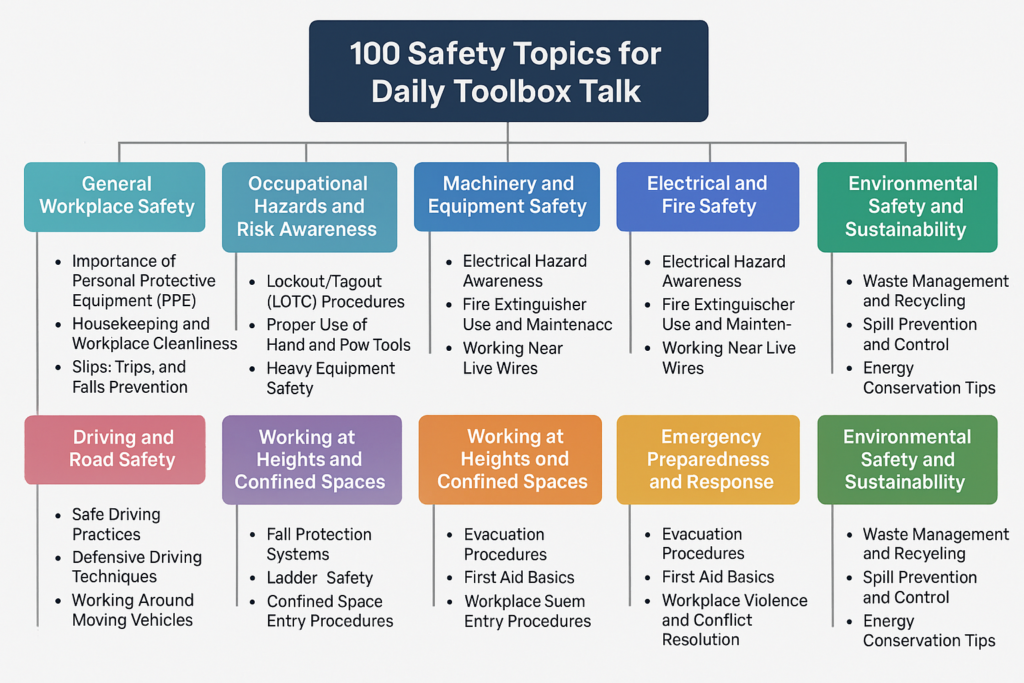
100 Safety Topics for Daily Toolbox Talk
Introduction
A Toolbox Talk is a short safety meeting held before work begins to discuss specific hazards and preventive measures. These daily discussions are essential for maintaining workplace safety and ensuring that workers stay aware of potential risks. Whether you work in construction, manufacturing, or any industry with occupational hazards, conducting regular toolbox talks can significantly reduce workplace incidents.
General Workplace Safety
Importance of Personal Protective Equipment (PPE)
PPE, such as helmets, gloves, and safety goggles, is the first line of defense against workplace injuries. Employees should wear the appropriate PPE for their job tasks and ensure it is in good condition.
Housekeeping and Workplace Cleanliness
A clutter-free workplace reduces the risk of accidents. Keeping walkways clear, storing tools properly, and disposing of waste regularly are all critical safety measures.
Slips, Trips, and Falls Prevention
Many workplace injuries occur due to slips, trips, and falls. Employees should always be mindful of wet floors, uneven surfaces, and obstructed pathways.
Fire Safety and Emergency Preparedness
Workers should know the locations of fire extinguishers, emergency exits, and assembly points. Fire drills should be conducted regularly to ensure everyone understands evacuation procedures.
Occupational Hazards and Risk Awareness
Identifying and Controlling Hazards
Workers should be trained to identify hazards and report them immediately. Implementing controls such as barriers, ventilation, or safety signage can help mitigate risks.
Hazard Communication (HazCom)
Employers should provide clear labeling and Safety Data Sheets (SDS) for hazardous substances. Employees should understand the risks associated with chemicals and how to handle them safely.
Risk Assessment Techniques
Performing job safety analyses (JSAs) and risk assessments can help identify potential hazards before an accident occurs.
Machinery and Equipment Safety
Lockout/Tagout (LOTO) Procedures
Before performing maintenance on machinery, workers should follow LOTO procedures to prevent accidental startup.
Proper Use of Hand and Power Tools
Using tools correctly reduces the risk of injury. Workers should inspect tools before use and follow manufacturer guidelines.
Heavy Equipment Safety
Only trained personnel should operate heavy machinery, and operators should always be aware of their surroundings.
Electrical and Fire Safety
Electrical Hazard Awareness
Exposed wires and overloaded circuits pose significant risks. Employees should report electrical issues immediately.
Fire Extinguisher Use and Maintenance
Workers should be trained on how to use fire extinguishers and ensure they are inspected regularly.
Working Near Live Wires
Only authorized personnel should work on or near live electrical equipment. Proper PPE should always be used.
Health and Well-being in the Workplace
Heat Stress and Hydration
Employees should stay hydrated and take breaks when working in hot environments.
Ergonomics and Injury Prevention
Proper posture and workstation adjustments can prevent musculoskeletal disorders.
Mental Health and Stress Management
Workplace stress can affect safety. Encouraging open communication and stress management techniques can help employees stay focused and productive.
Emergency Preparedness and Response
Evacuation Procedures
Every employee should be familiar with evacuation routes and assembly points.
First Aid Basics
Basic first aid knowledge can save lives. Employees should know how to treat minor injuries and when to seek medical attention.
Here are 100 Safety Topics for Daily Toolbox Talks, categorized for better organization:
General Workplace Safety
- Housekeeping and Workplace Cleanliness
- Slips, Trips, and Falls Prevention
- Proper Use of PPE (Personal Protective Equipment)
- Fire Prevention and Emergency Response
- Electrical Safety Awareness
- Safe Use of Ladders and Scaffolding
- Machine Guarding and Lockout/Tagout (LOTO)
- Hazard Communication (HazCom)
- Manual Handling and Lifting Techniques
- Safe Use of Hand and Power Tools
Health and Wellness
- Heat Stress Prevention
- Cold Weather Safety
- Hydration and Nutrition at Work
- Fatigue and Workplace Productivity
- Mental Health Awareness
- Preventing Workplace Stress
- Safe Handling of Hazardous Chemicals
- Respiratory Protection
- First Aid and CPR Awareness
- Ergonomics in the Workplace
Construction Safety
- Working at Heights – Fall Protection
- Trenching and Excavation Safety
- Confined Space Entry Procedures
- Heavy Equipment Safety
- Proper Material Storage and Handling
- Struck-By and Caught-In/Between Hazards
- Scaffold Safety Guidelines
- Traffic Control and Flagging Safety
- Safe Use of Cranes and Rigging
- Hot Work and Fire Watch
Oil & Gas Industry Safety
- H2S (Hydrogen Sulfide) Awareness
- Drilling Rig Safety
- Safe Handling of Flammable Liquids and Gases
- Emergency Shutdown Procedures
- Well Control Safety
- Blowout Prevention
- Gas Leak Detection and Response
- Pipeline Safety and Inspections
- Working in High-Pressure Environments
- Offshore Safety Protocols
Warehouse and Logistics Safety
- Forklift and Powered Industrial Truck Safety
- Pedestrian Safety in Warehouses
- Safe Loading and Unloading of Trucks
- Dock Safety and Trailer Securing
- Proper Stacking and Storage of Materials
- Safe Handling of Hazardous Materials in Warehouses
- Fire Prevention in Storage Areas
- Using Conveyors and Automated Systems Safely
- Preventing Musculoskeletal Disorders (MSDs) in Warehouses
- Spill Prevention and Cleanup
Transportation and Driving Safety
- Defensive Driving Techniques
- Seatbelt Safety Awareness
- Avoiding Distracted Driving
- Vehicle Maintenance and Pre-Trip Inspections
- Road Rage Prevention
- Safe Use of Company Vehicles
- Driving in Adverse Weather Conditions
- Safe Fueling Practices
- Load Securement and Stability
- Emergency Procedures for Vehicle Breakdowns
Electrical and Energy Safety
- Arc Flash and Electrical Hazard Prevention
- Overhead and Underground Power Line Safety
- Battery Handling and Storage Safety
- Safe Use of Extension Cords
- Grounding and Bonding in Electrical Systems
- Working Safely Near Energized Equipment
- Static Electricity Hazards
- Proper Use of Circuit Breakers and Fuses
- Electrical Shock First Aid Procedures
- Energy Isolation and Lockout/Tagout (LOTO)
Emergency Preparedness and Response
- Workplace Emergency Action Plan
- Earthquake Safety Procedures
- Hurricane and Storm Preparedness
- Fire Extinguisher Use and Maintenance
- Active Shooter Preparedness
- Chemical Spill Response
- Workplace Violence Prevention
- Bloodborne Pathogens Awareness
- Search and Rescue Procedures in the Workplace
- First Responder Communication and Coordination
Environmental Safety and Sustainability
- Waste Management and Recycling Best Practices
- Water Conservation at Work
- Preventing Air and Noise Pollution
- Spill Control and Secondary Containment
- Safe Handling and Disposal of Hazardous Waste
- Sustainable Energy Use in the Workplace
- Wildlife Safety in Outdoor Work Environments
- Proper Disposal of E-Waste
- Environmental Regulations Compliance
- Best Practices for Reducing Carbon Footprint
Behavior-Based Safety and Leadership
- Leading by Example in Workplace Safety
- Encouraging a Safety-First Culture
- Effective Communication of Safety Concerns
- Employee Involvement in Safety Programs
- Safety Observation and Reporting System
- Conducting Job Hazard Analysis (JHA)
- Positive Reinforcement for Safe Behavior
- Lessons Learned from Workplace Accidents
- The Role of Supervisors in Safety
- Continual Improvement in Workplace Safety
Conclusion
Daily toolbox talks play a crucial role in reinforcing workplace safety. By discussing relevant safety topics regularly, employers can create a culture of safety that protects workers and minimizes risks.
FAQs
1. What is the ideal length for a toolbox talk?
A toolbox talk should last between 5-15 minutes to keep employees engaged without disrupting workflow.
2. How often should toolbox talks be conducted?
Daily toolbox talks are recommended, especially in high-risk industries like construction and manufacturing.
3. What should be included in a toolbox talk?
Key safety concerns, hazard identification, preventive measures, and real-life examples should be covered.
4. Who is responsible for conducting a toolbox talk?
Supervisors, safety officers, or team leaders should lead toolbox talks, but all employees should be encouraged to participate.
5. Can toolbox talks prevent workplace accidents?
Yes! Regular toolbox talks keep safety top of mind, reducing the likelihood of accidents and injuries.