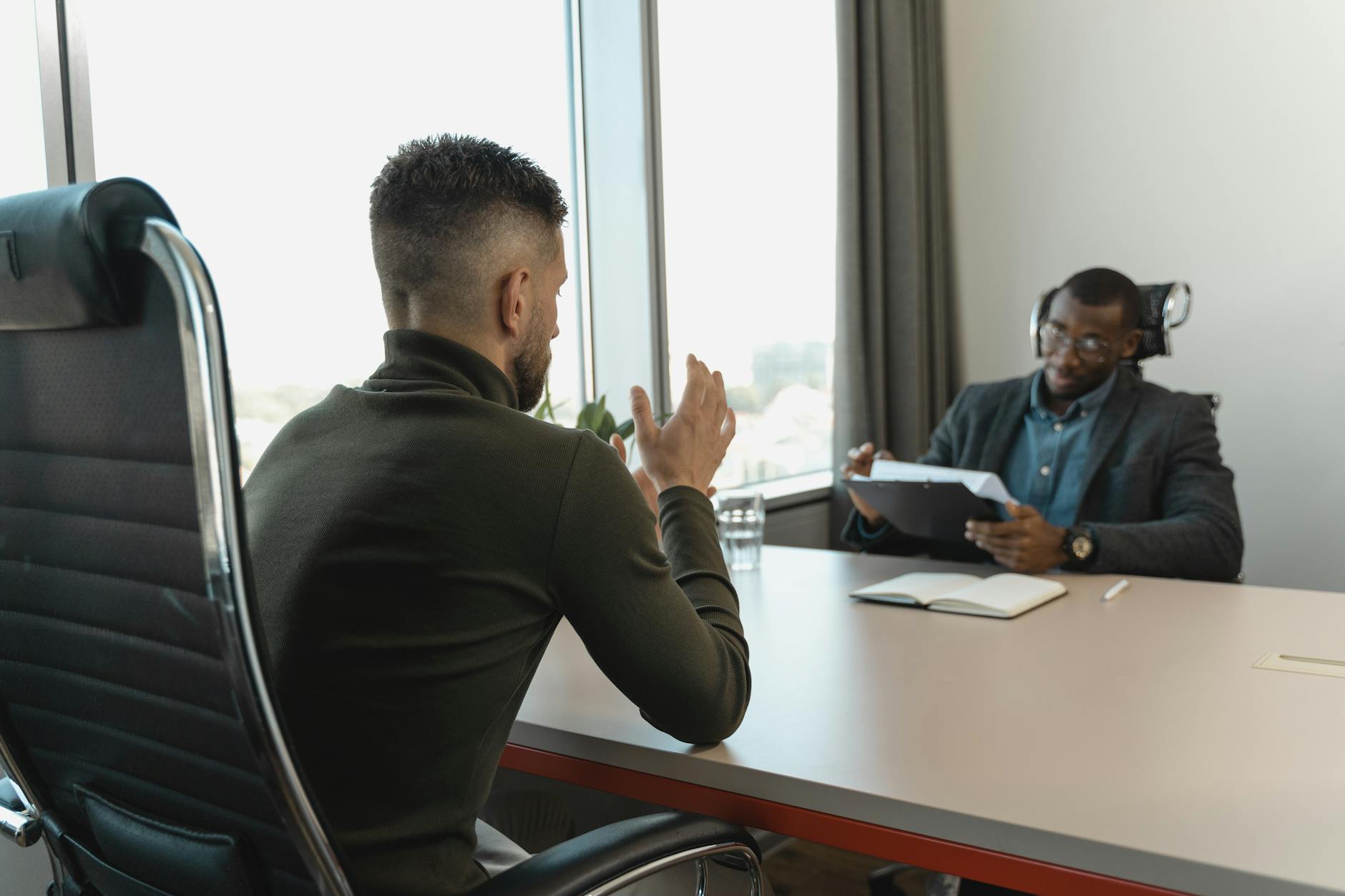
Oil & Gas Safety Officer: 55 Safety Job Interview Questions & Answers
Preparing for an Oil & Gas Safety Officer interview? Here are 55 common safety-related questions along with expert answers to help you succeed.
1. What are the primary responsibilities of an Oil & Gas Safety Officer?
Answer:
An Oil & Gas Safety Officer is responsible for:
- Ensuring compliance with OSHA, HSE, and company safety policies.
- Conducting risk assessments and hazard analyses.
- Organizing safety training for employees.
- Investigating accidents and near-misses.
- Monitoring workplace conditions and PPE usage.
- Implementing emergency response plans.
2. What are the major hazards in the oil and gas industry?
Answer:
Key hazards include:
- Fire and explosion risks (flammable gases/liquids).
- Chemical exposure (H2S, benzene, etc.).
- Confined space hazards.
- High-pressure equipment risks.
- Slips, trips, and falls.
- Machinery and equipment-related injuries.
3. How do you conduct a risk assessment in an oilfield?
Answer:
A risk assessment involves:
- Identifying hazards (chemical, physical, ergonomic).
- Evaluating risks (likelihood and severity).
- Implementing controls (elimination, substitution, engineering controls, PPE).
- Documenting findings and reviewing periodically.
4. What is H2S, and how do you protect workers from it?
Answer:
Hydrogen Sulfide (H2S) is a toxic, flammable gas common in oil & gas. Protection measures include:
- Gas detectors and alarms.
- Proper ventilation in confined spaces.
- SCBA (Self-Contained Breathing Apparatus) for high-risk areas.
- Emergency evacuation plans.
- Training on H2S awareness and first aid.
5. What is a Permit-to-Work (PTW) system, and why is it important?
Answer:
A Permit-to-Work (PTW) is a formal system authorizing high-risk tasks (hot work, confined space entry). It ensures:
- Hazards are identified and controlled.
- Only trained personnel perform the task.
- Proper isolation and lockout/tagout (LOTO) procedures are followed.
6. Explain the hierarchy of controls in hazard management.
Answer:
The hierarchy (from most to least effective):
- Elimination – Remove the hazard.
- Substitution – Replace with a safer alternative.
- Engineering Controls – Isolate workers from hazards (e.g., barriers).
- Administrative Controls – Training, procedures, and signage.
- PPE – Last line of defense (helmets, gloves, respirators).
7. How do you handle a gas leak emergency?
Answer:
Steps include:
- Evacuate the area immediately.
- Activate alarms and notify emergency response.
- Isolate the source (if safe to do so).
- Use gas detectors to monitor levels.
- Prevent ignition sources (no smoking, sparks).
- Provide medical aid if exposure occurs.
8. What is the role of a Job Safety Analysis (JSA)?
Answer:
A JSA breaks down tasks into steps to identify hazards and implement controls. Benefits:
- Improves worker awareness.
- Reduces accidents by addressing risks beforehand.
- Ensures compliance with safety procedures.
9. What are the key elements of an effective safety program?
Answer:
An effective program includes:
- Management commitment.
- Employee involvement.
- Hazard identification & control.
- Safety training.
- Incident reporting & investigation.
- Emergency preparedness.
- Continuous improvement.
10. How do you ensure compliance with OSHA regulations?
Answer:
- Conduct regular safety audits & inspections.
- Provide OSHA-mandated training.
- Maintain proper documentation.
- Implement corrective actions for violations.
- Stay updated on regulatory changes.
11. What is LOTO (Lockout/Tagout), and when is it used?
Answer:
LOTO prevents accidental machine startup during maintenance. It involves:
- Locking energy sources.
- Tagging with warning signs.
- Verifying isolation before work begins.
12. How do you investigate a workplace accident?
Answer:
Steps include:
- Secure the scene.
- Interview witnesses.
- Collect evidence (photos, equipment checks).
- Identify root causes (unsafe acts/conditions).
- Recommend corrective actions.
- Document findings in a report.
13. What are the common causes of fires in oil & gas facilities?
Answer:
Common causes:
- Static electricity near flammable vapors.
- Hot work (welding, cutting) without permits.
- Equipment malfunctions (pump leaks, valve failures).
- Improper storage of flammable materials.
14. What PPE is essential for oilfield workers?
Answer:
Essential PPE includes:
- Hard hats (impact protection).
- Safety goggles/face shields (chemical splashes).
- Fire-resistant clothing (FRC).
- Steel-toe boots.
- Gloves (cut/chemical resistant).
- Hearing protection (in high-noise areas).
15. What is a confined space, and what precautions are needed?
Answer:
A confined space has limited entry/exit and hazardous atmospheres (tanks, pipelines). Precautions:
- Permit-required entry.
- Gas testing before entry.
- Ventilation.
- Standby attendant for rescue.
16. What is the difference between a hazard and a risk?
Answer:
- Hazard: A potential source of harm (e.g., flammable gas, moving machinery).
- Risk: The likelihood and severity of harm occurring due to exposure to the hazard.
17. How do you conduct a safety audit?
Answer:
Steps in a safety audit:
- Review policies & procedures (OSHA, company standards).
- Inspect workplace conditions (PPE, equipment, signage).
- Interview employees (safety awareness, training).
- Check documentation (training records, incident reports).
- Report findings and recommend corrective actions.
18. What is BBS (Behavior-Based Safety)?
Answer:
Behavior-Based Safety (BBS) focuses on observing and improving workers’ safety behaviors. Key aspects:
- Encourages safe habits through positive reinforcement.
- Involves employee participation in safety observations.
- Reduces at-risk behaviors through feedback.
19. How do you handle non-compliant employees?
Answer:
- Educate on safety risks and policies.
- Provide retraining if necessary.
- Enforce disciplinary actions (if repeated violations).
- Encourage reporting of safety concerns without fear of retaliation.
20. What are the emergency response procedures for an oil spill?
Answer:
- Contain the spill (booms, absorbents).
- Stop the source (shut valves, isolate leaks).
- Evacuate & restrict access to prevent ignition.
- Notify authorities (EPA, OSHA if required).
- Clean up using approved methods (bioremediation, skimming).
- Document & report the incident.
21. What is the importance of a safety data sheet (SDS)?
Answer:
An SDS provides critical chemical safety information, including:
- Hazards (flammability, toxicity).
- Safe handling & storage.
- First aid measures.
- Emergency response.
- Required PPE.
22. How do you prevent slips, trips, and falls on-site?
Answer:
- Keep walkways clear of debris & spills.
- Use anti-slip mats in wet areas.
- Ensure proper lighting.
- Mark elevation changes (stairs, ramps).
- Enforce proper footwear (slip-resistant boots).
23. What is the role of a fire watch during hot work?
Answer:
A fire watch monitors for fires during and after hot work (welding, cutting). Duties:
- Check for sparks & smoldering materials.
- Ensure fire extinguishers are ready.
- Maintain a safe perimeter.
- Stay alert for at least 30 minutes after work ends.
24. How do you ensure crane safety in oil & gas operations?
Answer:
- Inspect cranes & rigging before use.
- Ensure qualified operators only.
- Follow load capacity limits.
- Use taglines to control swinging loads.
- Maintain safe clearance from power lines.
25. What are the dangers of working at heights, and how do you mitigate them?
Answer:
Dangers: Falls, dropped objects, structural collapse.
Mitigation:
- Use guardrails, harnesses & lanyards.
- Secure tools with lanyards.
- Inspect scaffolding & ladders before use.
- Train workers on fall protection systems.
26. What is the purpose of a safety committee?
Answer:
A safety committee promotes workplace safety by:
- Reviewing incidents & hazards.
- Recommending safety improvements.
- Encouraging employee participation.
- Ensuring compliance with regulations.
27. How do you promote a safety culture in the workplace?
Answer:
- Lead by example (management commitment).
- Encourage reporting of near-misses.
- Recognize safe behaviors.
- Provide continuous training.
- Involve employees in safety decisions.
28. What are the key requirements of a HAZCOM program?
Answer:
Under OSHA’s Hazard Communication Standard (HCS):
- Chemical inventory & labeling.
- Safety Data Sheets (SDS) accessible.
- Employee training on chemical hazards.
- Written program documentation.
29. How do you respond to a chemical exposure incident?
Answer:
- Remove the victim from exposure.
- Check SDS for first aid measures.
- Administer first aid (flush eyes/skin if needed).
- Seek medical help if severe.
- Report & investigate the incident.
30. What is the difference between flash point and auto-ignition temperature?
Answer:
- Flash Point: The lowest temperature where a liquid gives off enough vapor to ignite (with a spark).
- Auto-Ignition Temperature: The lowest temperature where a substance ignites without a spark.
31. What is a near-miss, and why should it be reported?
Answer:
A near-miss is an unplanned event that could have caused injury/damage but didn’t. Reporting helps:
- Identify hazards before accidents occur.
- Improve safety procedures.
- Prevent future incidents.
32. What are the key components of an emergency action plan (EAP)?
Answer:
An EAP must include:
- Evacuation routes & exits.
- Emergency contacts.
- Roles & responsibilities.
- Fire & spill response procedures.
- Medical emergency protocols.
33. How do you ensure electrical safety in hazardous areas?
Answer:
- Use explosion-proof equipment.
- Follow lockout/tagout (LOTO) procedures.
- Inspect cables & connections for damage.
- Train workers on arc flash hazards.
34. What is ergonomics, and why is it important in oil & gas?
Answer:
Ergonomics ensures workplace design reduces strain injuries. Important because:
- Reduces musculoskeletal disorders.
- Improves worker productivity.
- Minimizes fatigue-related errors.
35. How do you handle a worker refusing to wear PPE?
Answer:
- Explain the risks and legal requirements.
- Provide alternative PPE if comfort is an issue.
- Enforce disciplinary action if refusal continues.
36. What is a process safety management (PSM) program?
Answer:
PSM prevents catastrophic releases of hazardous chemicals. Key elements:
- Process hazard analysis (PHA).
- Mechanical integrity checks.
- Employee training.
- Emergency planning.
37. What are the dangers of hydrogen gas in refineries?
Answer:
- Highly flammable (wide explosive range).
- Colorless & odorless (hard to detect).
- Can cause embrittlement of metals.
38. How do you prevent static electricity fires in oil tanks?
Answer:
- Bonding & grounding during transfers.
- Avoid splashing when filling tanks.
- Use conductive hoses.
39. What is the purpose of a safety stand-down?
Answer:
A safety stand-down pauses work to discuss hazards, recent incidents, and reinforce safety protocols.
40. How do you inspect a fire extinguisher?
Answer:
Check:
- Pressure gauge (in green zone).
- Seal & pin (intact).
- No physical damage.
- Last inspection date.
41. What is a blowout preventer (BOP), and why is it important?
Answer:
A BOP is a critical valve system that seals wells to prevent uncontrolled releases (blowouts).
42. How do you manage contractor safety on-site?
Answer:
- Pre-qualify contractors (safety records).
- Provide site-specific safety training.
- Monitor compliance with safety rules.
43. What is the difference between OSHA and EPA regulations?
Answer:
- OSHA regulates workplace safety.
- EPA regulates environmental protection (spills, emissions).
44. How do you test for toxic gases in confined spaces?
Answer:
Use a multi-gas detector to check for:
- O2 levels (19.5%-23.5%).
- LEL (Lower Explosive Limit).
- H2S & CO levels.
45. What is a safety management system (SMS)?
Answer:
An SMS is a structured framework for managing safety risks, including policies, risk assessments, and audits.
46. What are the common causes of pipeline leaks?
Answer:
- Corrosion.
- Mechanical damage (excavation hits).
- Faulty welds.
- Pressure surges.
47. How do you ensure forklift safety in a refinery?
Answer:
- Train & certify operators.
- Inspect forklifts daily.
- Enforce speed limits.
- Use spotters in congested areas.
48. What is the role of a safety officer during a turnaround?
Answer:
- Conduct hazard assessments.
- Monitor contractor safety.
- Enforce permit-to-work systems.
- Investigate incidents.
49. What is the importance of a pre-job safety meeting?
Answer:
- Identifies hazards before work starts.
- Ensures all workers understand risks.
- Clarifies emergency procedures.
50. How do you stay updated with safety regulations?
Answer:
- Attend OSHA/HSE training.
- Subscribe to industry newsletters.
- Participate in safety forums.
- Review regulatory updates.
51. What is a safety case, and when is it required?
Answer:
A safety case is a comprehensive document that demonstrates how a company identifies, assesses, and controls major hazards in high-risk industries like oil & gas.
Key Components of a Safety Case:
- Hazard Identification (HAZID, HAZOP studies)
- Risk Assessment (quantitative & qualitative analysis)
- Safety Management Systems (SMS)
- Emergency Response Plans
- Proof of Compliance with regulations (e.g., OSHA PSM, EU Seveso Directive)
When is it Required?
- Offshore platforms (e.g., under the Safety Case Regulations in the UK/Norway).
- Major Hazard Facilities (MHFs) handling large quantities of flammable/toxic materials.
- Refineries & chemical plants under Process Safety Management (PSM) standards.
52. How do you prevent dropped object incidents?
Answer:
Dropped objects are a leading cause of fatalities in oil & gas. Prevention strategies include:
Engineering Controls:
- Toe boards & tool tethers on elevated work platforms.
- Barriers & netting to catch falling objects.
- Securing loose materials (pipes, tools) with lanyards.
Administrative Controls:
- Dropped Object Prevention Scheme (DROPS) compliance.
- Regular inspections of lifting equipment.
- Exclusion zones under crane operations.
PPE & Training:
- Hard hats with chin straps.
- Training on safe material handling.
53. What is the role of a safety officer in incident command?
Answer:
During an emergency (fire, spill, explosion), the safety officer supports the Incident Commander (IC) by:
Pre-Incident:
- Ensuring emergency drills are conducted.
- Verifying response equipment (fire extinguishers, spill kits).
During Incident:
- Assessing hazards (gas leaks, structural integrity).
- Evacuation coordination (safe muster points).
- PPE & safety compliance for responders.
Post-Incident:
- Investigating root causes.
- Updating emergency plans based on lessons learned.
54. How do you assess the effectiveness of safety training?
Answer:
Quantitative Metrics:
- Reduction in incidents post-training.
- Training test scores (pass/fail rates).
- Audit findings (compliance improvements).
Qualitative Metrics:
- Employee feedback (surveys, interviews).
- Observations of safe behaviors post-training.
- Participation rates in voluntary safety programs.
Continuous Improvement:
- Refresher courses based on gaps.
- Adapting training methods (e.g., VR simulations for hazard recognition).
55. What are the best practices for handling radioactive materials in oilfields?
Answer:
Radioactive materials (e.g., NORM – Naturally Occurring Radioactive Material) in pipelines/equipment require:
Exposure Control:
- ALARA Principle (As Low As Reasonably Achievable).
- Radiation monitoring badges for workers.
- Shielding (lead containers for storage).
Handling & Disposal:
- Specialized PPE (gloves, respirators).
- Licensed waste disposal (per EPA/NRC regulations).
- Decontamination procedures for equipment.
Training & Compliance:
- OSHA 10/30-Hour Radiation Safety courses.
- Regular dosimeter checks.
Construction Safety Officer: 50+ Safety Job interview Questions & Answers
10 Situational Safety Interview Questions and Answers
25 Technical HSE Interview Questions and Answers