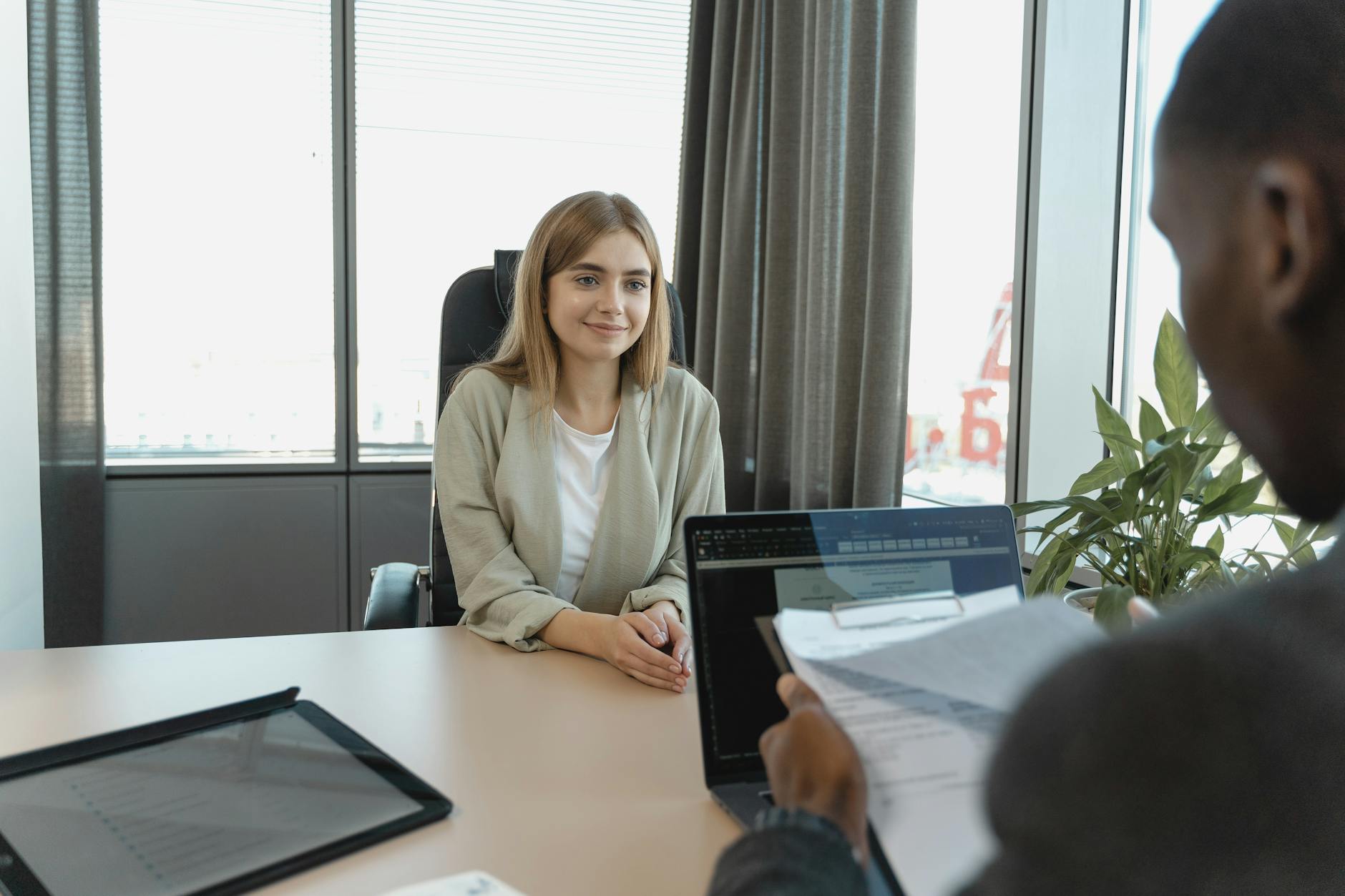
Process Safety Engineer: 50 Safety Job Interview Questions & Answers
General Process Safety Questions
1. What is Process Safety Management (PSM)?
Process Safety Management (PSM) is a regulatory framework designed to prevent the release of hazardous chemicals that could lead to catastrophic incidents. It involves identifying, evaluating, and controlling process hazards through engineering, administrative, and procedural safeguards.
2. What are the key elements of PSM as per OSHA 1910.119?
The 14 elements of PSM include:
- Employee Participation
- Process Safety Information
- Process Hazard Analysis (PHA)
- Operating Procedures
- Training
- Contractor Management
- Pre-Startup Safety Review (PSSR)
- Mechanical Integrity
- Hot Work Permit
- Management of Change (MOC)
- Incident Investigation
- Emergency Planning and Response
- Compliance Audits
- Trade Secrets
3. How does Process Safety differ from Occupational Safety?
- Process Safety focuses on preventing catastrophic incidents (explosions, toxic releases) involving hazardous processes.
- Occupational Safety deals with preventing worker injuries (slips, falls, ergonomic issues).
4. What is a Layer of Protection Analysis (LOPA)?
LOPA is a semi-quantitative risk assessment method used to evaluate the adequacy of Independent Protection Layers (IPLs) in preventing hazardous events.
5. Explain the concept of ALARP (As Low As Reasonably Practicable).
ALARP means reducing risks to the lowest level feasible, considering cost, time, and effort, while ensuring that further risk reduction is grossly disproportionate to the benefits gained.
Hazard Identification & Risk Assessment
6. What are the common Hazard Identification Techniques?
- HAZOP (Hazard and Operability Study)
- What-If Analysis
- FMEA (Failure Modes and Effects Analysis)
- Checklist Analysis
- Bowtie Analysis
7. What is a HAZOP Study? How is it conducted?
HAZOP is a structured technique to identify potential deviations from design intent using guide words (e.g., NO, MORE, LESS) in a systematic review by a multidisciplinary team.
8. What is the difference between Inherent Safety and Engineered Safety?
- Inherent Safety eliminates hazards by design (e.g., using less hazardous materials).
- Engineered Safety adds protective systems (e.g., relief valves, alarms).
9. What is a Safety Integrity Level (SIL)? How is it determined?
SIL measures the reliability of safety instrumented functions (SIFs). It ranges from SIL 1 (lowest) to SIL 4 (highest) and is determined via risk assessment methods like LOPA.
10. How do you conduct a Quantitative Risk Assessment (QRA)?
QRA involves:
- Hazard Identification
- Frequency Analysis (likelihood of failure)
- Consequence Modeling (impact of failure)
- Risk Estimation and Evaluation
Process Safety Engineering & Design
11. What are the key considerations for designing a safe process plant?
- Inherently safer design principles
- Adequate pressure relief systems
- Proper material selection
- Redundancy in safety systems
- Proper spacing and layout
12. What is a Pressure Relief Valve (PRV)? How does it work?
A PRV automatically releases excess pressure to prevent equipment failure. It opens at a set pressure and recloses when normal conditions are restored.
13. What is a Blowdown Drum, and when is it used?
A blowdown drum collects and safely vents emergency releases from pressure relief systems, typically in refineries and chemical plants.
14. What is a BLEVE (Boiling Liquid Expanding Vapor Explosion)?
A BLEVE occurs when a pressurized liquid container fails due to external heat, leading to a violent explosion (e.g., LPG tank exposed to fire).
15. How do you prevent static electricity hazards in flammable liquid handling?
- Bonding and grounding
- Using conductive materials
- Controlling flow velocity
- Avoiding splash filling
Incident Investigation & Emergency Response
16. What are the root cause analysis techniques used in incident investigations?
- 5 Whys
- Fishbone (Ishikawa) Diagram
- Fault Tree Analysis (FTA)
- Event Tree Analysis (ETA)
17. How would you investigate a process safety incident?
- Secure the scene
- Collect evidence (photos, logs, interviews)
- Identify immediate and root causes
- Recommend corrective actions
- Implement lessons learned
18. What is the role of a Process Safety Engineer in emergency response?
- Assisting in emergency shutdown procedures
- Evaluating potential escalation risks
- Supporting incident command
- Post-incident analysis
19. What is an Emergency Relief System (ERS)?
An ERS (e.g., relief valves, rupture disks) safely discharges excess pressure or chemicals during an overpressure scenario.
20. How do you ensure compliance with OSHA’s Process Safety Management (PSM) standards?
- Regular audits
- Employee training
- Proper documentation
- Implementing MOC procedures
Management of Change (MOC) & Compliance
21. What is Management of Change (MOC)? Why is it important?
MOC is a systematic process to review and approve modifications to processes, equipment, or procedures to ensure safety and compliance.
22. What steps are involved in an MOC procedure?
- Identify the proposed change
- Risk assessment (PHA if needed)
- Approval by authorized personnel
- Implementation with proper training
- Documentation and closeout
23. What are common pitfalls in MOC implementation?
- Inadequate risk assessment
- Poor communication
- Skipping pre-startup safety reviews
- Lack of training for personnel
24. How do you handle a situation where a change is made without MOC approval?
- Immediately assess risks
- Stop unauthorized changes if unsafe
- Conduct a retrospective MOC review
- Reinforce MOC training
25. What are the key differences between PSM and EPA’s Risk Management Program (RMP)?
- PSM (OSHA) focuses on worker safety.
- RMP (EPA) focuses on community safety and environmental protection.
Mechanical Integrity & Maintenance
26. What is Mechanical Integrity in Process Safety?
Mechanical Integrity ensures equipment is designed, installed, and maintained correctly to prevent failures.
27. What are critical equipment inspections in a process plant?
- Pressure vessels
- Piping systems
- Relief devices
- Storage tanks
- Rotating machinery
28. How often should safety-critical equipment be inspected?
Based on regulatory requirements, manufacturer recommendations, and risk assessments (e.g., pressure vessels may require annual inspections).
29. What is a Failure Modes and Effects Analysis (FMEA)?
FMEA identifies potential failure modes of components and their impacts on system safety.
30. What is a Safety Instrumented System (SIS)?
An SIS is a set of devices designed to take a process to a safe state when hazardous conditions are detected.
Human Factors & Training
31. How do human factors impact process safety?
Human errors (procedural deviations, lack of training) contribute to major incidents. Proper design, training, and procedures mitigate risks.
32. What are the best practices for operator training in process safety?
- Classroom and hands-on training
- Simulator-based drills
- Regular refresher courses
- Competency assessments
33. How do you ensure effective shift handover in a process plant?
- Standardized checklists
- Clear communication protocols
- Documentation of ongoing issues
34. What is a Near-Miss, and why is reporting it important?
A near-miss is an unplanned event that could have caused harm. Reporting helps prevent future incidents.
35. How do you promote a strong safety culture in an organization?
- Leadership commitment
- Employee involvement
- Transparent reporting
- Continuous improvement
Advanced Process Safety Topics
36. What is Dust Explosion Hazard Assessment?
Evaluating risks from combustible dust (e.g., in grain, chemical industries) and implementing controls (ventilation, suppression systems).
37. What is a Vapor Cloud Explosion (VCE)?
An explosion resulting from ignition of a flammable vapor cloud (e.g., refinery leaks).
38. How do you assess the impact of toxic gas releases?
Using dispersion modeling (e.g., ALOHA, PHAST) to estimate exposure zones and emergency response plans.
39. What is the role of a Process Safety Engineer in a plant expansion project?
- Conducting PHAs
- Ensuring compliance with PSM
- Reviewing design safety features
- Implementing MOC procedures
40. What are the key lessons from major process safety incidents (e.g., Bhopal, Texas City)?
- Importance of MOC
- Proper maintenance
- Effective emergency response
- Strong safety culture
Behavioral & Situational Questions
41. Describe a time you resolved a critical process safety issue.
(Example: Identified a faulty relief valve during an audit, initiated immediate replacement, and updated inspection protocols.)
42. How would you handle a manager who insists on bypassing safety protocols for production?
- Explain risks clearly
- Refer to regulatory requirements
- Escalate if necessary
43. What would you do if you discovered an undocumented process change?
- Halt operations if unsafe
- Conduct a risk assessment
- Implement MOC retroactively
44. How do you stay updated with process safety regulations?
- Attending industry conferences
- Subscribing to safety journals
- Participating in professional networks
45. Give an example of how you improved safety performance in a previous role.
(Example: Introduced a digital MOC system, reducing approval times and improving compliance.)
Technical & Scenario-Based Questions
46. How would you design a flare system for a chemical plant?
- Calculate relief loads
- Size flare headers
- Ensure proper knockout drum design
- Consider radiation and dispersion impacts
47. A reactor is over-pressurizing. What immediate actions would you take?
- Activate emergency shutdown
- Verify relief systems are functioning
- Isolate feed streams
- Evacuate personnel if necessary
48. How do you determine the safe distance for siting control rooms near hazardous areas?
Using QRA and blast overpressure studies to ensure occupant safety.
49. What factors influence the selection of fire protection systems for a storage tank?
- Flammability of stored material
- Tank size and design
- Potential fire scenarios (pool fire, jet fire)
50. Explain the steps for conducting a Pre-Startup Safety Review (PSSR).
- Verify equipment installation
- Confirm safety systems are operational
- Ensure personnel training
- Document compliance
Manufacturing Safety Officer: 50+ Safety Job Interview Questions & Answers
Oil & Gas Safety Officer: 55 Safety Job Interview Questions & Answers
Construction Safety Officer: 50+ Safety Job interview Questions & Answers