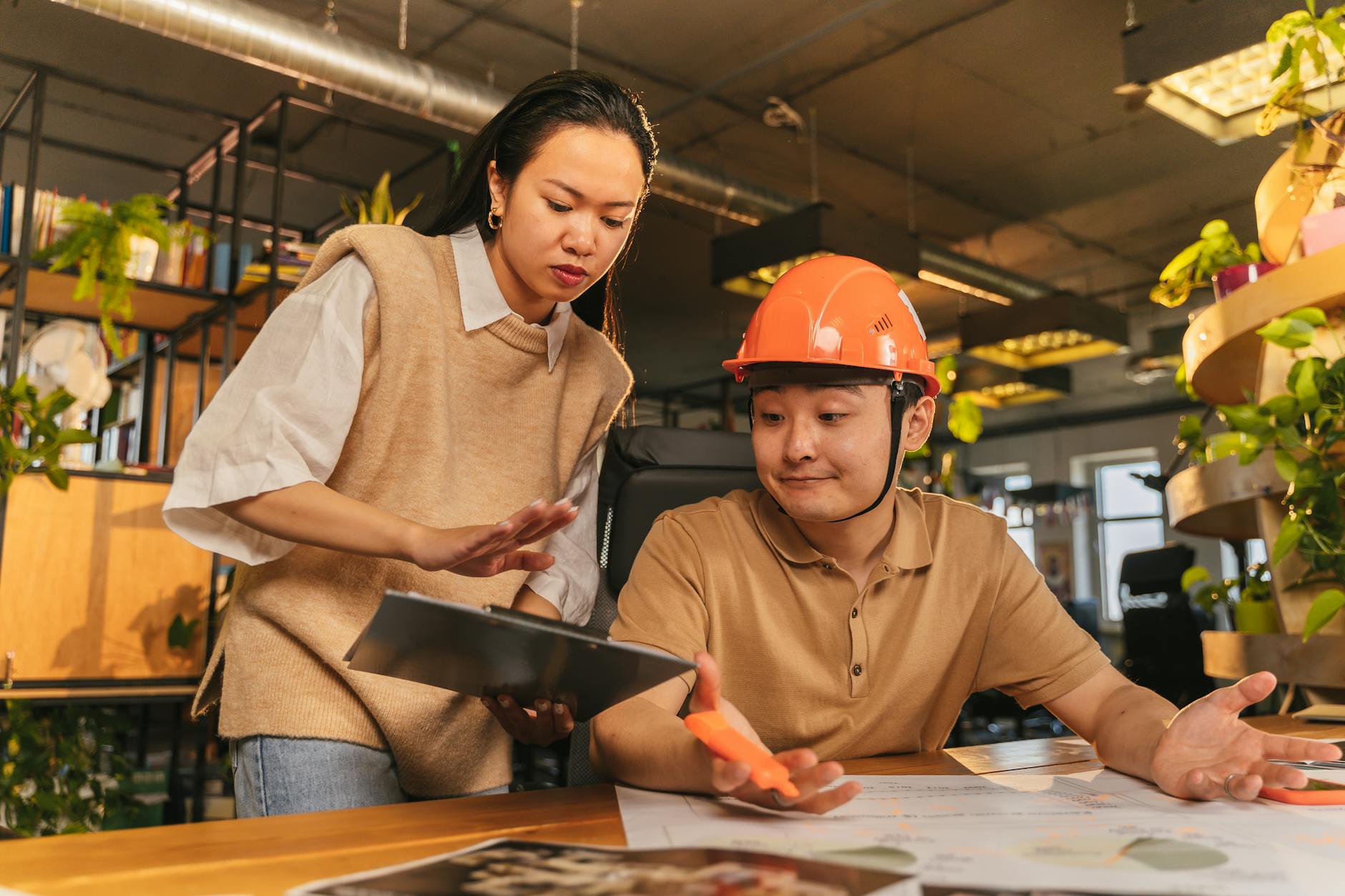
25 Workplace Safety Topics for Meetings
1. Personal Protective Equipment (PPE)
Personal Protective Equipment (PPE) is essential for safeguarding workers from potential hazards. It includes items like helmets, gloves, goggles, ear protection, and safety shoes. Employers must ensure the availability of appropriate PPE based on job requirements. Workers should be trained on the correct use, maintenance, and limitations of PPE. Regular inspections are crucial to identify wear and tear. Compliance with PPE protocols not only protects individuals but also minimizes workplace accidents. Proper PPE usage is a fundamental aspect of creating a safe and healthy work environment, reducing the risk of injuries and enhancing overall productivity.
2. Hazard Communication
Hazard communication ensures that employees are aware of the risks associated with chemicals and substances in the workplace. It involves the use of labels, Safety Data Sheets (SDS), and proper training. Clear signage and instructions help workers identify potential dangers and take necessary precautions. Employers must implement an effective hazard communication program that complies with regulatory standards. Understanding chemical hazards promotes safe handling, storage, and disposal practices. By keeping communication clear and accessible, workplaces can prevent chemical-related accidents and health issues, fostering a culture of safety and awareness among all employees.
3. Fire Safety and Emergency Preparedness
Fire safety is critical to protecting lives and property in the workplace. Employees should be trained on how to use fire extinguishers, recognize fire hazards, and respond to fire alarms. Emergency preparedness includes having clear evacuation routes, conducting regular drills, and maintaining accessible emergency exits. Employers must also ensure that fire suppression systems are functional. Awareness of emergency procedures can significantly reduce panic during real incidents. A proactive approach to fire safety ensures that everyone knows their role in an emergency, enhancing overall workplace safety and readiness.
4. Slips, Trips, and Falls
Slips, trips, and falls are among the most common workplace incidents. These accidents often result from wet floors, uneven surfaces, or misplaced objects. Preventive measures include regular housekeeping, proper signage, and wearing non-slip footwear. Employers should conduct routine inspections to identify and address hazards. Training employees to be vigilant about their surroundings helps minimize these risks. Quick response to spills and maintenance of walking surfaces are crucial for preventing accidents. Fostering a culture of awareness can significantly reduce the occurrence of slips, trips, and falls, ensuring a safer workplace environment.
5. Machine Safety and Lockout/Tagout (LOTO)
Machine safety is vital to prevent injuries from moving parts, electrical hazards, and equipment malfunctions. Lockout/Tagout (LOTO) procedures ensure that machines are properly shut down during maintenance or repairs. Employees must be trained to identify energy sources and apply LOTO devices correctly. Regular equipment inspections and clear operational guidelines enhance safety. Ignoring these protocols can result in severe injuries or fatalities. Establishing a robust machine safety program minimizes risks and ensures compliance with safety regulations, protecting both workers and equipment.
6. Manual Material Handling and Ergonomics
Manual material handling involves lifting, carrying, and moving objects. Poor techniques can lead to musculoskeletal disorders, strains, and injuries. Training employees on proper lifting methods, such as bending the knees and keeping the back straight, is essential. Ergonomic practices, like using mechanical aids and adjusting workstations, reduce physical strain. Employers should assess tasks for ergonomic risks and implement suitable interventions. By promoting safe handling techniques and providing necessary tools, workplaces can prevent injuries and improve employee well-being.
7. Working at Heights
Working at heights requires strict safety measures to prevent falls and injuries. Workers should use fall protection equipment such as harnesses, guardrails, and safety nets. Training programs must cover the proper use, inspection, and maintenance of these devices. Pre-job risk assessments help identify potential hazards. Scaffolding and ladders should be secure, stable, and compliant with safety standards. Employers must also enforce the use of personal fall arrest systems. Prioritizing height safety ensures compliance with regulations and protects employees from life-threatening incidents.
8. Electrical Safety
Electrical safety is essential to prevent shocks, burns, and fires. Employees must be trained to recognize electrical hazards and follow safe practices. This includes inspecting cords, avoiding overloaded circuits, and using equipment with proper grounding. Only qualified personnel should handle electrical repairs. Lockout/Tagout procedures are critical during maintenance. Regular inspections and adherence to safety guidelines minimize risks. Raising awareness about electrical dangers creates a safer work environment and prevents potentially fatal incidents.
9. Confined Space Safety
Confined spaces pose unique risks, including limited oxygen, toxic gases, and restricted movement. Entry into such areas requires proper training, permits, and atmospheric testing. Workers should use appropriate PPE and be aware of emergency procedures. Continuous monitoring of air quality ensures safe conditions. Rescue plans must be in place and practiced regularly. Employers should identify and label confined spaces clearly. Adhering to safety protocols reduces the risk of entrapment, asphyxiation, and other hazards.
10. Hand and Power Tool Safety
Hand and power tool safety focuses on proper use, maintenance, and storage. Employees should inspect tools before use to ensure they are in good condition. Damaged or defective tools should be removed from service immediately. Training on correct handling techniques helps prevent injuries. Personal Protective Equipment (PPE) like gloves and goggles may be required based on the task. Adhering to tool safety guidelines enhances efficiency while minimizing accident risks.
11. Vehicle and Equipment Safety
Safe operation of vehicles and equipment is critical in various industries. Operators must be trained, certified, and familiar with operational procedures. Regular maintenance checks ensure equipment reliability. Safety features like seat belts and backup alarms should be functional. Awareness of surroundings and adherence to traffic rules prevent collisions. Employers should implement protocols for reporting equipment malfunctions. Promoting safe driving habits reduces workplace accidents and protects personnel and assets.
12. Housekeeping and Workplace Organization
Good housekeeping prevents hazards like slips, trips, and fires. Work areas should be clean, organized, and free of clutter. Employees must store tools and materials properly and dispose of waste safely. Routine inspections help identify potential dangers. Clear walkways and accessible emergency exits are essential. A well-organized workplace enhances safety, productivity, and morale.
13. Workplace Violence Prevention
Preventing workplace violence involves recognizing warning signs and taking proactive measures. Training programs should address conflict resolution and reporting procedures. Security measures like access control and surveillance can deter incidents. Employers must establish a zero-tolerance policy for violence and harassment. Open communication and supportive management create a safer, more respectful work environment.
14. First Aid and CPR Awareness
Basic first aid and CPR knowledge can save lives in emergencies. Employees should know the location of first aid kits and how to use them. Regular training sessions ensure familiarity with CPR techniques and emergency response protocols. Employers should designate trained first aid responders. Promoting first aid awareness enhances workplace preparedness and response capabilities.
15. Heat Stress Prevention
Heat stress can cause dehydration, heat exhaustion, and heat stroke. Workers in hot environments should drink water frequently, take breaks in shaded areas, and wear breathable clothing. Employers must educate staff about heat stress symptoms and implement heat safety protocols. Monitoring weather conditions and adjusting workloads accordingly can prevent heat-related illnesses.
16. Cold Stress Awareness
Cold stress can lead to frostbite, hypothermia, and reduced productivity. Workers should wear insulated clothing and limit exposure to extreme cold. Training on recognizing cold stress symptoms is essential. Employers must provide heated break areas and implement safety measures for cold environments. Awareness and preparedness help prevent cold-related health issues.
17. Hearing Protection
Exposure to high noise levels can cause hearing damage. Workers should use earplugs or earmuffs in noisy areas. Employers must conduct noise assessments and provide appropriate hearing protection. Regular hearing tests help monitor employees’ hearing health. Promoting hearing conservation protects workers from long-term auditory issues.
18. Eye Protection and Eye Wash Stations
Eye injuries are preventable with proper protective equipment. Safety goggles and face shields should be worn when handling chemicals, grinding metal, or using power tools. Eye wash stations must be accessible and functional. Training employees on eye safety reduces the risk of injuries and enhances workplace protection.
19. Respiratory Protection
Respiratory hazards like dust, fumes, and vapors require proper protection. Workers must use masks or respirators suitable for the hazard. Fit-testing ensures effectiveness. Employers should assess air quality and provide adequate ventilation. Respiratory safety prevents long-term health complications.
20. Chemical Safety and Spill Response
Chemical safety involves proper handling, storage, and disposal of substances. Employees must understand hazard labels and SDS information. Spill response training ensures quick, safe containment of leaks. Emergency supplies like spill kits should be readily available. Adhering to chemical safety protocols prevents accidents and environmental damage.
How to Conduct a Successful Safety Training Program
List of Safety Training Topics for Employees
Monthly Safety Training Topics for 2025
5 Minute Safety Topics for 2025
21. Lone Worker Safety
Lone workers face unique risks when working independently. Employers should implement communication systems and regular check-ins. Training on emergency procedures is essential. Providing lone workers with safety devices enhances protection and response capabilities.
22. Workplace Ergonomics for Remote Workers
Remote workers need ergonomic setups to avoid strain and discomfort. Proper chair height, screen positioning, and regular breaks support musculoskeletal health. Employers can offer guidance and resources for creating safe home workspaces.
23. Behavior-Based Safety (BBS)
Behavior-Based Safety focuses on observing and reinforcing safe practices. Training programs should promote proactive safety behaviors. Regular feedback and positive reinforcement encourage continuous improvement in workplace safety culture.
24. Near-Miss Reporting
Near-miss reporting identifies potential hazards before incidents occur. Encouraging employees to report close calls helps implement preventive measures. Open, non-punitive reporting systems enhance workplace safety.
25. Mental Health and Stress Management
Mental health is crucial for overall well-being. Workplaces should offer resources like counseling services and stress management workshops. Open communication and supportive leadership foster a positive, productive environment.