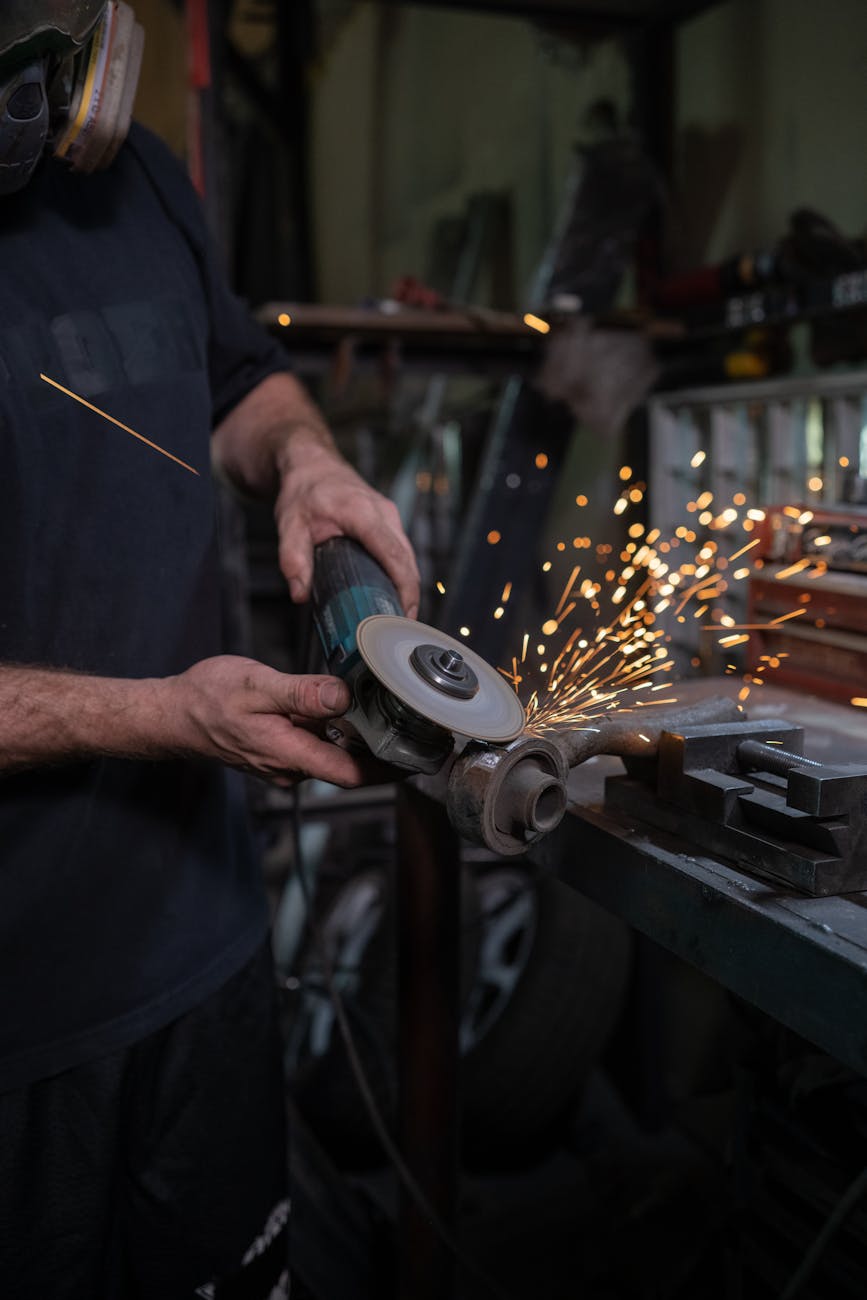
25 Most Common Workplace Hazards & How to Avoid Them
1. Slips, Trips, and Falls
- Keep floors clean and dry.
- Use warning signs for wet floors.
- Ensure proper lighting in walkways.
2. Electrical Hazards
- Regularly inspect electrical equipment.
- Avoid overloading circuits.
- Use insulated tools in electrical work.
3. Fire Hazards
- Store flammable materials safely.
- Maintain fire extinguishers and alarms.
- Conduct regular fire drills.
4. Falling Objects
- Secure heavy items on shelves.
- Wear hard hats in construction zones.
- Use safety nets where necessary.
5. Poor Ergonomics
- Provide adjustable chairs and desks.
- Encourage proper posture and breaks.
- Use ergonomic keyboards and mice.
6. Hazardous Chemicals
- Store chemicals in labeled containers.
- Provide proper ventilation.
- Use personal protective equipment (PPE).
7. Heavy Machinery Accidents
- Train employees on machine operation.
- Use safety guards on equipment.
- Follow lockout/tagout procedures.
8. Workplace Violence
- Implement anti-harassment policies.
- Train staff on conflict resolution.
- Install security cameras if needed.
9. Noise Pollution
- Provide earplugs or noise-canceling headphones.
- Limit exposure to loud noises.
- Use soundproofing where possible.
10. Repetitive Strain Injuries
- Rotate tasks to avoid overuse.
- Encourage stretching exercises.
- Use ergonomic tools.
11. Lack of Proper Training
- Conduct regular safety training sessions.
- Ensure employees know emergency procedures.
- Provide clear instructions for tasks.
12. Confined Spaces
- Test air quality before entry.
- Use proper ventilation.
- Have a rescue plan in place.
13. Extreme Temperatures
- Provide heating/cooling systems.
- Offer breaks in extreme conditions.
- Supply protective clothing.
14. Poor Air Quality
- Ensure proper ventilation.
- Use air purifiers if needed.
- Limit exposure to dust and fumes.
15. Stress and Mental Health Issues
- Promote work-life balance.
- Offer counseling services.
- Encourage open communication.
16. Manual Handling Injuries
- Train employees in proper lifting techniques.
- Use mechanical aids like trolleys.
- Avoid lifting heavy objects alone.
17. Working at Heights
- Use guardrails and harnesses.
- Inspect ladders and scaffolding.
- Avoid working alone at heights.
18. Biological Hazards
- Provide gloves and masks in medical settings.
- Dispose of waste properly.
- Follow hygiene protocols.
19. Vehicle Accidents
- Enforce seatbelt use.
- Maintain company vehicles regularly.
- Avoid distracted driving.
20. Radiation Exposure
- Use shielding in high-risk areas.
- Monitor exposure levels.
- Provide protective gear.
21. Inadequate Lighting
- Install bright, energy-efficient lights.
- Replace burnt-out bulbs promptly.
- Use task lighting where needed.
22. Fatigue and Overwork
- Encourage regular breaks.
- Limit excessive overtime.
- Promote healthy sleep habits.
23. Lack of Emergency Preparedness
- Keep first aid kits accessible.
- Train employees in CPR and first aid.
- Have clear evacuation routes.
24. Poor Housekeeping
- Organize workspaces to avoid clutter.
- Dispose of waste properly.
- Schedule regular cleaning.
25. Cybersecurity Threats
- Train employees on phishing scams.
- Use strong passwords and encryption.
- Regularly update security software.
By identifying and addressing these hazards, workplaces can ensure a safer and more productive environment for employees.
Lifting Plan for Tandem Lifting and Critical Lifting
Critical Lifting Risk Assessment
Tandem Lifting Risk Assessment
Tandem Lifting Vs Critical Lifting
Unsafe Act vs Unsafe Condition Explained with 10 Examples of Each