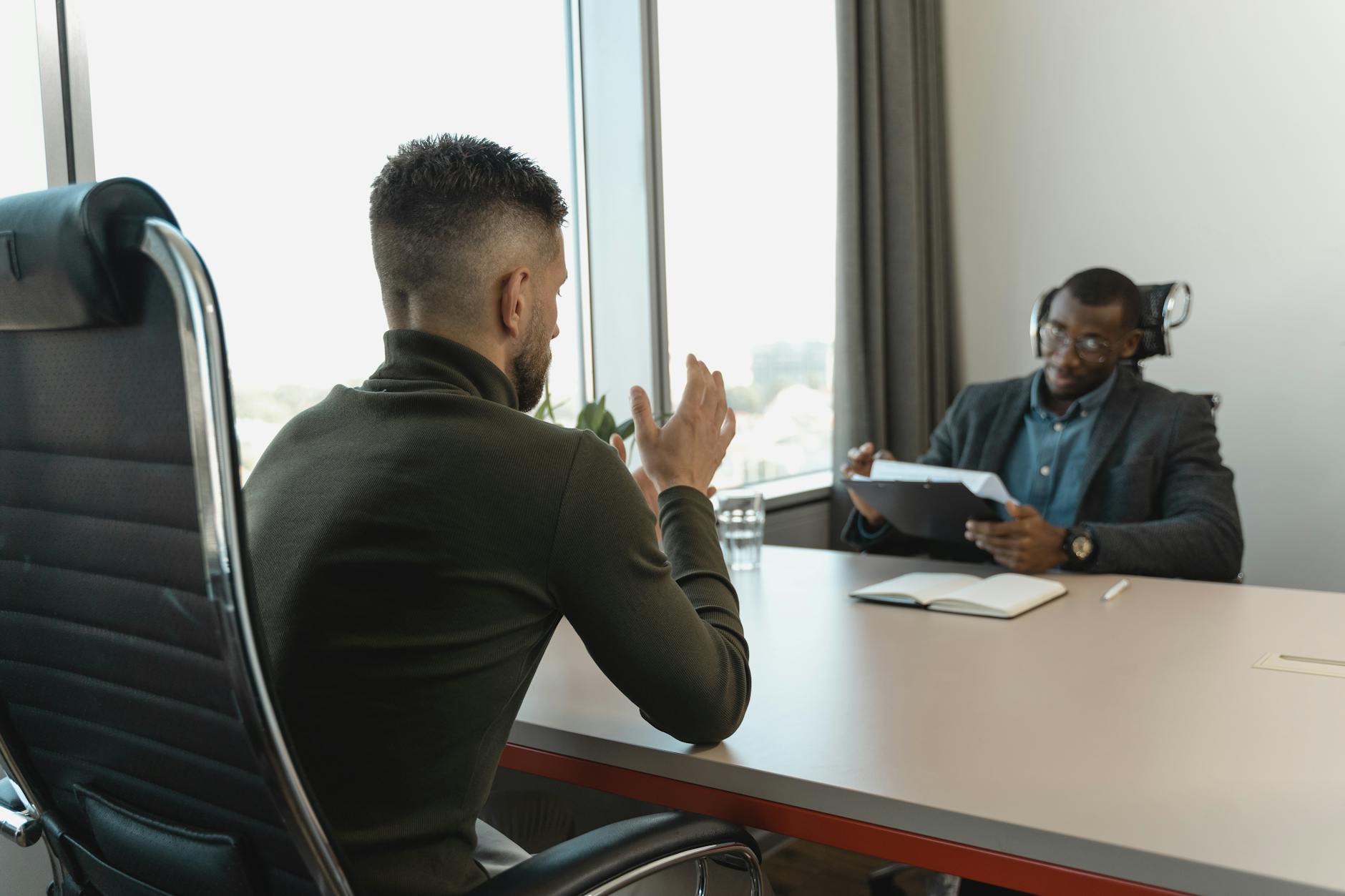
101 Safety Officer Interview Questions and Sample Answers | Free Download
Introduction
Importance of Interview Preparation for Safety Officers
Preparing for a safety officer interview is crucial to land the role you desire. Employers want to see both technical expertise and strong communication skills to ensure the safety of their teams and projects.
Overview of Safety Officer Roles and Responsibilities
A safety officer ensures workplace safety compliance, mitigates risks, and educates teams on safety measures. From conducting inspections to implementing safety policies, their role is vital across industries.
General Interview Questions
Tell Me About Yourself
Sample Answer:
“I am a dedicated safety professional with over five years of experience in ensuring compliance with safety regulations in manufacturing environments. I hold a certification in OSHA standards and have a proven track record of reducing workplace incidents by 30% through proactive measures.”
Why Do You Want to Work as a Safety Officer?
Sample Answer:
“I am passionate about creating safe environments where employees can thrive without fear of harm. I believe safety is the foundation of any successful operation, and I am eager to contribute my skills to your organization.”
Technical Knowledge Questions
What is a Job Hazard Analysis (JHA)?
Sample Answer:
“A JHA identifies potential hazards associated with a specific job task and determines measures to mitigate those risks. It’s a proactive approach to preventing workplace accidents.”
Can You Explain the Difference Between a Hazard and a Risk?
Sample Answer:
“A hazard is anything that has the potential to cause harm, such as chemicals or equipment. A risk is the likelihood of that harm occurring.”
Situational and Behavioral Questions
How Would You Handle a Workplace Accident?
Sample Answer:
“In the event of an accident, my first priority is to ensure the injured person’s safety and provide immediate medical assistance. Then, I secure the area to prevent further harm, gather witness statements, and document the incident thoroughly. I conduct a root cause analysis to identify what went wrong and implement corrective actions to prevent recurrence.”
Describe a Time When You Implemented a Safety Improvement
Sample Answer:
“In my previous role, I noticed that workers frequently bypassed safety harnesses due to their inconvenient placement. I collaborated with management to redesign the placement strategy, ensuring accessibility. This small change increased compliance by 40% and reduced near-miss incidents significantly.”
Industry-Specific Questions
Safety Challenges in Construction Projects
Key Considerations:
- Heavy equipment and machinery use
- Working at heights
- Exposure to hazardous materials
- Coordination with multiple contractors
Sample Answer:
“In construction, it’s essential to have strict adherence to PPE use, daily toolbox talks, and a well-documented emergency response plan. Regular audits and safety drills are also critical to maintaining a safe environment.”
What Safety Measures Are Critical in Oil and Gas?
Sample Answer:
“Oil and gas environments are inherently high-risk. Key measures include maintaining fire safety equipment, ensuring proper storage of flammable substances, and conducting regular H2S gas monitoring. Employee training on evacuation protocols is equally crucial.”
Regulatory and Compliance Questions
What is OSHA, and Why is it Important?
Sample Answer:
“OSHA, or the Occupational Safety and Health Administration, is a U.S. agency that sets and enforces safety standards in the workplace. Its guidelines help organizations minimize risks, protect employees, and avoid costly legal issues.”
How Do You Stay Updated with Safety Regulations?
Sample Answer:
“I regularly attend industry workshops and seminars, subscribe to safety publications, and participate in online forums. Staying connected with professional organizations also helps me keep abreast of the latest developments.”
Technical Skills Assessment
Are You Proficient in Safety Software and Tools?
Sample Answer:
“Yes, I have hands-on experience with safety management software such as EHS Insight and Intelex. These tools have been instrumental in streamlining incident reporting, tracking compliance, and conducting audits efficiently.”
How Do You Conduct Risk Assessments?
Sample Answer:
“I follow a systematic process: identifying potential hazards, evaluating the likelihood and severity of risks, and implementing control measures. I prioritize actions based on the risk matrix and continuously monitor their effectiveness.”
Communication and Leadership Questions
How Do You Train Employees on Safety Protocols?
Sample Answer:
“I use a mix of interactive sessions, visual aids, and practical demonstrations to ensure employees grasp the importance of safety protocols. Regular quizzes and feedback sessions help reinforce learning.”
Describe a Time You Managed a Difficult Employee in Terms of Safety
Sample Answer:
“An employee repeatedly ignored PPE guidelines. I scheduled a one-on-one meeting to understand their concerns, which revealed discomfort with the provided gear. After arranging alternative equipment and explaining the risks involved, compliance improved immediately.”
Personal Traits and Competencies
How Do You Handle Stress in High-Risk Situations?
Sample Answer:
“I stay calm by focusing on actionable steps. Clear communication and teamwork are key to managing emergencies effectively. Reflecting on past experiences and practicing mindfulness also helps me maintain composure.”
What Makes You an Effective Safety Officer?
Sample Answer:
“My attention to detail, proactive approach, and ability to build trust with employees ensure effective safety management. I believe in leading by example and consistently advocating for a safety-first culture.”
Mock Questions for Practice
Mock Scenario 1: Identifying Hazards
Question: “You’re inspecting a new site and notice several cables lying across walkways. What do you do?”
Sample Answer:
“I would immediately arrange to secure the cables with covers or reroute them to eliminate the trip hazard. Next, I’d brief the team about temporary measures and ensure the issue is logged for permanent resolution.”
Mock Scenario 2: Emergency Response
Question: “How would you respond to a fire in the workplace?”
Sample Answer:
“I would activate the alarm system, ensure evacuation routes are clear, and assist in evacuating personnel. After notifying emergency services, I’d use a fire extinguisher if safe and feasible to do so.”
101 Safety Officer Interview Questions with detailed sample answers for each question.
General Questions
- Tell us about yourself.
Detailed Answer:
“I hold a degree in Occupational Health and Safety and have over six years of experience in construction and oil and gas industries. My primary responsibilities have included developing safety protocols, conducting audits, and ensuring compliance with safety regulations. I take pride in creating a culture of safety that has led to a 40% reduction in incidents in my last organization.” - Why do you want to work as a Safety Officer?
Detailed Answer:
“I am deeply passionate about workplace safety and believe every employee deserves to work in a safe environment. My role as a Safety Officer allows me to make a tangible difference in reducing risks and protecting lives. This aligns perfectly with my personal and professional values.” - What do you know about our company?
Detailed Answer:
“Your company is recognized for its commitment to innovation and safety, especially in the construction industry. I am impressed by your recent achievement of ISO 45001 certification and your investment in advanced safety training programs for employees.”
Technical Knowledge Questions
- What is a risk assessment?
Detailed Answer:
“Risk assessment is the process of identifying workplace hazards, evaluating the risks associated with those hazards, and implementing measures to eliminate or control them. For example, in a manufacturing plant, I assessed risks from moving machinery and implemented guardrails and training to reduce incidents.” - What does ‘permit to work’ mean?
Detailed Answer:
“A permit to work is a formal document that authorizes specific high-risk activities, such as confined space entry, electrical work, or hot work. It ensures that all safety protocols are in place before starting the job, minimizing the risk of accidents.” - What is PPE, and why is it important?
Detailed Answer:
“PPE stands for Personal Protective Equipment, such as helmets, gloves, goggles, and respirators. It is crucial because it provides a last line of defense against workplace hazards. For instance, in chemical handling, PPE protects workers from exposure to harmful substances.”
Regulatory and Compliance Questions
- What is OSHA, and why is it important?
Detailed Answer:
“OSHA stands for the Occupational Safety and Health Administration. It is vital because it sets and enforces workplace safety standards, protecting workers from injuries and illnesses. Compliance with OSHA regulations not only saves lives but also improves operational efficiency.” - Explain the hierarchy of hazard control.
Detailed Answer:
“The hierarchy of controls prioritizes hazard mitigation methods:- Elimination: Remove the hazard entirely.
- Substitution: Replace the hazard with something safer.
- Engineering controls: Isolate people from the hazard.
- Administrative controls: Change work practices.
- PPE: Provide protective equipment as a last resort.
For example, in a noisy environment, eliminating the noise source is the most effective, while providing earplugs is the least effective.”
- What is the purpose of a safety audit?
Detailed Answer:
“A safety audit is conducted to evaluate an organization’s compliance with safety regulations, identify potential hazards, and assess the effectiveness of current safety measures. Regular audits help in proactively addressing risks.”
Scenario-Based Questions
- How would you handle a worker not wearing PPE?
Detailed Answer:
“I would first approach the worker calmly and explain the importance of PPE for their safety. I would verify if PPE was provided and if the worker was trained on its use. If non-compliance persists, I would document the incident and escalate it as per company policy.” - What would you do if you identified a major hazard on-site?
Detailed Answer:
“I would immediately stop work in the affected area, inform the site supervisor, and assess the hazard. After conducting a risk assessment, I would implement control measures and only allow work to resume once the area is safe.” - How would you respond to a fire in the workplace?
Detailed Answer:
“I would activate the fire alarm, guide employees to the designated evacuation point, and ensure no one is left behind. If trained, I might use a fire extinguisher for small fires. Post-incident, I would review the emergency response plan to address any shortcomings.”
Behavioral Questions
- Describe a time you successfully implemented a safety improvement.
Detailed Answer:
“In my previous role, we faced frequent slip-and-fall incidents due to wet floors. I introduced anti-slip mats, improved signage, and trained employees on spill management. These measures reduced such incidents by 50% within six months.” - How do you manage stress during emergencies?
Detailed Answer:
“I focus on following established protocols and prioritizing actions based on the severity of the situation. My training and experience help me remain calm and make rational decisions under pressure.” - How do you communicate safety policies to employees?
Detailed Answer:
“I use a mix of methods, including clear written policies, regular training sessions, toolbox talks, and visual aids like posters. I also encourage feedback to ensure employees fully understand and follow the policies.”
Leadership and Training Questions
- How do you motivate employees to follow safety procedures?
Detailed Answer:
“I lead by example, recognize and reward safe behavior, and make safety training engaging and relatable. I also involve employees in safety planning to give them a sense of ownership.” - Have you ever trained someone in safety protocols? How?
Detailed Answer:
“Yes, I conducted fire safety training for warehouse staff. I used a combination of presentations, videos, and hands-on fire extinguisher practice. Afterward, I assessed their understanding through a quiz and drills.” - How do you stay updated on safety regulations?
Detailed Answer:
“I attend safety seminars, subscribe to industry newsletters, participate in webinars, and maintain memberships in professional organizations like the National Safety Council.”
- What is an HSE policy?
Detailed Answer:
“HSE stands for Health, Safety, and Environment. An HSE policy outlines an organization’s commitment to ensuring the health and safety of employees and minimizing environmental impact. It acts as a guideline for achieving these objectives.” - What steps would you take to control a chemical spill?
Detailed Answer:
“First, I would evacuate the area and ensure personal safety by using appropriate PPE. Then, I’d contain the spill using absorbent materials, consult the SDS for cleanup instructions, and report the incident for further action.”
Technical Knowledge Questions
- What is the difference between a hazard and a risk?
Detailed Answer:
“A hazard is anything with the potential to cause harm, such as machinery or chemicals. A risk is the likelihood that the hazard will cause harm and the severity of the consequences. For example, a slippery floor is a hazard, while the risk depends on how often people walk on it and the potential injuries.” - What is a Job Safety Analysis (JSA)?
Detailed Answer:
“A JSA is a process where tasks are broken down into steps, potential hazards for each step are identified, and control measures are implemented. It ensures that workers understand the risks and follow safe practices. For example, before operating heavy machinery, a JSA helps ensure safety.” - What is the lockout/tagout procedure?
Detailed Answer:
“Lockout/tagout is a safety procedure to ensure that machinery is properly shut off and not started again before maintenance is complete. It involves locking the energy source and tagging it to inform others of the ongoing work.” - What are confined space hazards?
Detailed Answer:
“Confined space hazards include oxygen deficiency, toxic gases, flammable atmospheres, and restricted entry or exit. Proper permits, atmospheric testing, and rescue plans are essential to ensure safety in confined spaces.” - What is an emergency evacuation plan?
Detailed Answer:
“An emergency evacuation plan outlines procedures for safely evacuating people during emergencies like fires, chemical spills, or natural disasters. It includes escape routes, assembly points, and roles and responsibilities during the evacuation.”
Regulatory and Compliance Questions
- What is ISO 45001, and why is it important?
Detailed Answer:
“ISO 45001 is an international standard for occupational health and safety management systems. It helps organizations proactively improve safety performance, reduce workplace injuries, and ensure compliance with legal requirements.” - What is the importance of incident reporting?
Detailed Answer:
“Incident reporting helps identify the root cause of accidents or near misses, enabling corrective actions to prevent recurrence. It also fosters a culture of transparency and continuous improvement.” - How do you prepare for a safety audit?
Detailed Answer:
“I prepare by reviewing the latest safety policies, ensuring all records are up to date, conducting a pre-audit walkthrough, and addressing potential non-compliance areas.” - What are your responsibilities during a regulatory inspection?
Detailed Answer:
“During an inspection, I act as the liaison between the regulator and the company, provide requested documents, ensure the inspector’s safety on-site, and address any concerns they identify.” - What is a safety committee, and how do you ensure its effectiveness?
Detailed Answer:
“A safety committee is a group of employees and management representatives focused on improving workplace safety. To ensure effectiveness, I set clear objectives, conduct regular meetings, and track progress on identified safety issues.”
Behavioral and Scenario-Based Questions
- Describe a time when you conducted a safety inspection. What did you find?
Detailed Answer:
“During a routine safety inspection at a construction site, I found several workers not wearing hard hats. I addressed the issue immediately by halting work, providing a safety briefing, and ensuring compliance moving forward.” - How would you respond to an employee refusing to follow safety rules?
Detailed Answer:
“I would speak privately with the employee to understand their concerns or reasons for non-compliance. Then, I’d reinforce the importance of safety rules, provide additional training if needed, and escalate the matter if the behavior persists.” - What would you do if you identified a safety violation by a supervisor?
Detailed Answer:
“I would document the violation and address it respectfully with the supervisor, emphasizing the importance of leading by example. If the issue isn’t resolved, I’d escalate it according to company policy.” - How do you prioritize safety tasks during a high-pressure situation?
Detailed Answer:
“I focus on addressing the most critical hazards first, such as life-threatening risks. I delegate tasks when possible and ensure constant communication with the team to manage the situation efficiently.” - Have you ever managed a safety-related project? What was the outcome?
Detailed Answer:
“I led a project to implement a fall protection system in a high-risk area. This involved risk assessments, vendor selection, and employee training. The result was a 90% reduction in fall-related incidents within six months.”
Advanced Technical Questions
- What is the role of ergonomics in workplace safety?
Detailed Answer:
“Ergonomics involves designing workspaces and tasks to fit employees, reducing strain and preventing musculoskeletal disorders. For example, providing adjustable chairs and proper lifting techniques can minimize back injuries.” - What is process safety management (PSM)?
Detailed Answer:
“PSM focuses on preventing accidents involving hazardous chemicals through comprehensive management systems. It includes process design, maintenance, and emergency preparedness.” - How do you handle noise hazards?
Detailed Answer:
“I assess noise levels using sound meters, implement engineering controls like barriers, provide hearing protection, and schedule regular hearing tests for workers.” - What are leading and lagging safety indicators?
Detailed Answer:
“Leading indicators predict safety performance, such as training hours or safety observations. Lagging indicators measure past performance, like incident rates or lost workdays.” - What are the common hazards in the oil and gas industry?
Detailed Answer:
“Common hazards include fire, explosion risks, toxic gases, confined spaces, and equipment-related accidents. Rigorous training, PPE, and adherence to standards like API RP 75 mitigate these risks.”
Miscellaneous Questions
- What steps do you take to ensure safety in remote locations?
Detailed Answer:
“I provide emergency communication devices, conduct thorough risk assessments, supply safety kits, and implement strict check-in procedures.” - How do you handle safety challenges with multi-language teams?
Detailed Answer:
“I use multilingual materials, visual aids, and interpreters during training. I also promote a safety culture where employees feel comfortable raising concerns in any language.” - What is your experience with safety management software?
Detailed Answer:
“I have used platforms like Intelex and SAP EHS to manage incident reporting, audits, and compliance tracking. These tools streamline processes and improve data accuracy.” - What would you do if your safety recommendations were ignored?
Detailed Answer:
“I would document my recommendations, provide supporting data, and escalate the issue to higher management if necessary. Safety is non-negotiable, and I’d persist until the matter is addressed.” - How do you measure the success of a safety program?
Detailed Answer:
“I track KPIs such as incident rates, training completion percentages, and employee feedback. A decline in accidents and increased compliance indicate success.”
Closing Questions
- What do you think is the most significant challenge in safety today?
Detailed Answer:
“Balancing safety with productivity is a major challenge. It requires fostering a culture where safety is viewed as integral to operational success.” - Where do you see yourself in five years?
Detailed Answer:
“I aim to advance my career by obtaining certifications like CSP and contributing to safety innovations in high-risk industries.” - What motivates you as a Safety Officer?
Detailed Answer:
“Knowing that my work directly impacts the well-being of employees and prevents accidents motivates me. Every incident-free day feels like a personal accomplishment.”
Behavioral and Situational Questions
- Describe a time you had to convince management to invest in safety improvements.
Detailed Answer:
“In a previous role, I noticed frequent manual handling injuries in the warehouse. I proposed purchasing automated lifting equipment, supported by data showing injury trends and potential cost savings from reduced lost workdays. After presenting a cost-benefit analysis, management approved the investment, which led to a significant decline in injuries.” - How would you manage safety during a major project deadline?
Detailed Answer:
“I prioritize safety by ensuring adequate planning, allocating resources, and conducting pre-task briefings to address potential hazards. I also emphasize that safety protocols should never be compromised for speed and regularly monitor compliance throughout the project.” - What actions would you take if you identified a new hazard on-site?
Detailed Answer:
“I would immediately address the hazard by isolating the area if necessary, conduct a risk assessment, and implement appropriate controls. I would then update the hazard log and communicate the findings to the team during a toolbox talk.” - How do you handle resistance to new safety measures?
Detailed Answer:
“I address resistance by explaining the rationale behind the changes, providing training, and engaging employees in the decision-making process. When workers understand how safety measures benefit them, they are more likely to comply.” - How do you ensure contractors comply with safety standards?
Detailed Answer:
“I review contractor qualifications and safety records during pre-qualification. On-site, I ensure they are trained on our safety policies, conduct regular inspections, and enforce compliance through penalties or corrective actions if necessary.”
Technical Knowledge Questions
- What is an SDS, and why is it important?
Detailed Answer:
“An SDS, or Safety Data Sheet, provides detailed information about a chemical, including its hazards, handling procedures, and emergency measures. It is essential for ensuring safe storage, use, and disposal of chemicals.” - What are the key elements of an emergency response plan?
Detailed Answer:
“Key elements include:
- Clear roles and responsibilities
- Evacuation routes and assembly points
- Emergency contact information
- Communication protocols
- Training and drills for employees.”
- What is the importance of conducting accident investigations?
Detailed Answer:
“Accident investigations identify the root cause of incidents, allowing the implementation of corrective actions to prevent recurrence. They also help in improving safety policies and fostering a culture of accountability.” - How do you control electrical hazards?
Detailed Answer:
“Electrical hazards are controlled by ensuring proper grounding, using insulated tools, labeling circuits, conducting regular inspections, and training workers on electrical safety procedures.” - What is the difference between proactive and reactive safety management?
Detailed Answer:
“Proactive safety management focuses on preventing incidents through risk assessments, training, and audits. Reactive safety management involves responding to incidents after they occur, such as conducting investigations and implementing corrective actions.”
Leadership and Training Questions
- How do you tailor safety training to different audiences?
Detailed Answer:
“I adapt training based on the audience’s roles, language proficiency, and prior knowledge. For instance, I use hands-on demonstrations for workers and data-driven presentations for management.” - How do you handle employees who do not take safety training seriously?
Detailed Answer:
“I emphasize the importance of training by explaining real-world consequences of non-compliance and engaging them with interactive sessions. If the behavior persists, I escalate the matter as per company policy.” - What is your approach to mentoring junior Safety Officers?
Detailed Answer:
“I provide regular guidance through one-on-one meetings, involve them in audits and investigations, and encourage continuous learning by recommending relevant courses and certifications.” - How do you develop a safety culture in an organization?
Detailed Answer:
“I promote a safety-first mindset by leading by example, recognizing safe behaviors, involving employees in safety planning, and ensuring transparency in addressing safety concerns.”
Scenario-Based Questions
- What would you do if you discovered a worker fainted due to heat stress?
Detailed Answer:
“I would immediately move the worker to a cooler area, provide water, and call for medical assistance if needed. I would then review the site’s heat stress management protocols, such as hydration breaks and cooling measures.” - How would you handle an employee reporting a near-miss incident?
Detailed Answer:
“I would thank the employee for reporting the incident, investigate it thoroughly, and implement preventive measures. Near-miss reporting is vital for identifying potential hazards before they lead to accidents.” - How would you respond to an emergency where multiple injuries occurred?
Detailed Answer:
“I would prioritize care based on the severity of injuries using first aid, call emergency services, and coordinate with the emergency response team to manage the situation effectively.” - How do you ensure safety compliance during night shifts?
Detailed Answer:
“I ensure compliance through adequate lighting, regular supervisor inspections, and providing proper training for night shift-specific risks, such as fatigue management and emergency preparedness.”
Industry-Specific Questions
- What are the common safety challenges in the construction industry?
Detailed Answer:
“Challenges include fall hazards, equipment misuse, and working in confined spaces. Addressing these involves proper PPE, training, and ensuring compliance with standards like OSHA’s Fall Protection Standard.” - How do you ensure safety in the oil and gas industry?
Detailed Answer:
“I focus on managing fire and explosion risks, ensuring proper storage of hazardous chemicals, conducting regular drills, and adhering to API and OSHA standards specific to the industry.” - What are the key safety measures in confined spaces?
Detailed Answer:
“Measures include conducting atmospheric testing, issuing confined space permits, providing appropriate PPE, and having a trained rescue team on standby.”
General Safety Knowledge Questions
- What is your experience with safety certifications?
Detailed Answer:
“I hold certifications such as NEBOSH and OSHA 30-hour training. These have equipped me with the knowledge to identify hazards, assess risks, and implement effective safety controls.” - What are safe lifting techniques?
Detailed Answer:
“Safe lifting techniques include keeping the back straight, bending at the knees, holding the load close to the body, and avoiding twisting movements. Training workers on these practices is essential.” - How do you address workplace violence?
Detailed Answer:
“I implement policies to prevent workplace violence, provide training on conflict resolution, and establish reporting mechanisms. Regular risk assessments help in identifying and mitigating potential triggers.”
Technical and Advanced Knowledge Questions
- What are the types of fire extinguishers, and when should they be used?
Detailed Answer:
“Fire extinguishers are categorized based on the type of fire they extinguish:
- Class A: For ordinary combustibles like wood and paper.
- Class B: For flammable liquids like oil and gasoline.
- Class C: For electrical fires.
- Class D: For combustible metals.
- Class K: For cooking oils and fats.
Understanding the type of fire and ensuring the right extinguisher is available and operable is critical for effective response.”
- How do you ensure the safe handling of hazardous chemicals?
Detailed Answer:
“I ensure safe handling through proper labeling and storage, using SDSs for guidance, providing appropriate PPE, training employees on safe practices, and implementing spill response plans.” - What are the common hazards of working at heights, and how do you mitigate them?
Detailed Answer:
“Common hazards include falls, dropped objects, and structural instability. Mitigation involves fall protection systems like harnesses, guardrails, securing tools, and conducting regular inspections of equipment and platforms.” - How do you implement an energy control program (LOTO) effectively?
Detailed Answer:
“I ensure an effective LOTO program by training workers, providing standardized lockout devices, conducting periodic audits, and ensuring proper documentation of procedures for controlling hazardous energy.” - What is the role of safety signage, and how do you determine its placement?
Detailed Answer:
“Safety signage communicates hazards, warnings, or required actions. Placement is determined by conducting risk assessments and ensuring signs are visible, legible, and located where the risk is present.”
Behavioral and Management-Oriented Questions
- Describe a time you had to mediate a safety dispute between workers.
Detailed Answer:
“In one instance, workers disagreed over the proper use of a lifting device. I listened to both parties, reviewed the manufacturer’s guidelines, and clarified the correct procedure during a toolbox talk. This resolved the conflict and reinforced safe practices.” - How do you ensure employee buy-in for safety initiatives?
Detailed Answer:
“I involve employees in the development of safety programs, seek their feedback, recognize and reward safe behaviors, and consistently communicate the importance of safety for their well-being.” - What steps do you take to prepare for a safety drill?
Detailed Answer:
“I start by defining objectives, preparing realistic scenarios, training participants on their roles, ensuring all required resources are available, and conducting a debrief afterward to assess performance and areas for improvement.” - How do you manage a multicultural workforce to maintain safety?
Detailed Answer:
“I provide safety training in multiple languages, use universal safety symbols and visuals, and encourage open communication to address cultural differences that may affect safety practices.” - How do you handle safety during adverse weather conditions?
Detailed Answer:
“I implement weather-specific safety plans, such as ensuring proper clothing for extreme temperatures, halting work during severe weather, and communicating emergency protocols to all employees.”
Regulatory and Compliance Questions
- What is the importance of OSHA regulations in workplace safety?
Detailed Answer:
“OSHA regulations set minimum safety standards to protect workers. They guide employers in identifying hazards, implementing controls, and maintaining compliance to prevent injuries and penalties.” - How do you conduct a compliance gap analysis?
Detailed Answer:
“I review current practices against regulatory requirements, identify areas of non-compliance, document findings, and develop a corrective action plan to address the gaps.” - What are the key components of a health and safety policy?
Detailed Answer:
“Key components include a statement of commitment, roles and responsibilities, procedures for hazard identification and risk control, emergency response protocols, and mechanisms for monitoring and review.” - How do you ensure compliance with PPE requirements?
Detailed Answer:
“I conduct regular inspections, provide training on the proper use and maintenance of PPE, and enforce policies requiring its use in designated areas.” - What is the difference between a leading and lagging indicator in safety?
Detailed Answer:
“Leading indicators predict future safety performance, such as safety training hours or the number of safety observations. Lagging indicators measure past performance, like incident rates or lost workdays.”
Scenario-Based Questions
- What steps would you take if there was a chemical spill in the workplace?
Detailed Answer:
“I would first evacuate the area and restrict access. Then, I’d assess the spill using the SDS, deploy spill control measures, and ensure the proper cleanup team handles the situation. Afterward, I’d review the incident and update spill response protocols if needed.” - How would you handle a worker reporting symptoms of an occupational illness?
Detailed Answer:
“I would ensure the worker receives immediate medical attention, investigate the potential causes, review workplace exposures, and implement measures to prevent similar cases.” - How would you manage safety during a machinery breakdown?
Detailed Answer:
“I would lock out and tag out the equipment, investigate the cause of the breakdown, ensure repairs are done safely, and inspect the machine thoroughly before resuming operations.”
Industry-Specific Questions
- What are common safety hazards in warehouses?
Detailed Answer:
“Hazards include slips and trips, manual handling injuries, forklift accidents, and falling objects. Controls include clear walkways, proper lifting techniques, forklift training, and secure storage practices.” - How do you ensure safety during transportation of hazardous materials?
Detailed Answer:
“I ensure proper labeling and documentation, train drivers on handling emergencies, inspect vehicles regularly, and comply with transportation regulations like the DOT Hazardous Materials Regulations.”
Personal Development and Closing Questions
- What steps do you take to stay updated on safety regulations?
Detailed Answer:
“I regularly attend seminars, subscribe to industry newsletters, participate in professional networks, and complete relevant certifications to keep my knowledge current.” - What is your proudest achievement as a Safety Officer?
Detailed Answer:
“In my previous role, I implemented a behavior-based safety program that reduced incident rates by 40% within a year. Seeing the tangible impact of my efforts on employee safety was incredibly rewarding.” - Why do you want to work with our company as a Safety Officer?
Detailed Answer:
“Your company’s commitment to innovation and prioritizing employee safety aligns with my professional values. I am eager to contribute to your safety culture and help achieve your organizational goals.” - What safety certifications are you planning to pursue next?
Detailed Answer:
“I plan to pursue the Certified Safety Professional (CSP) certification to enhance my expertise and bring more value to my role.” - What do you believe makes a great Safety Officer?
Detailed Answer:
“A great Safety Officer is proactive, detail-oriented, a strong communicator, and passionate about protecting people and the environment. They must also be adaptable and continuously seek improvement.” - How do you handle feedback about your safety policies?
Detailed Answer:
“I view feedback as an opportunity to improve. I actively listen, evaluate the suggestions objectively, and incorporate them when they align with safety goals.” - What are your key takeaways from your previous roles?
Detailed Answer:
“I’ve learned the importance of building trust, being proactive in identifying hazards, and the critical role of training in fostering a safety culture.” - How do you plan to contribute to our team if hired?
Detailed Answer:
“I plan to bring my expertise in risk management, enhance safety training programs, and collaborate with the team to continuously improve our safety standards.” - What motivates you in a career as a Safety Officer?
Detailed Answer:
“Knowing that my work helps create a safer environment and prevents harm motivates me every day. I am passionate about making a difference in people’s lives through effective safety practices.”
Conclusion
Wrapping Up Your Interview Preparation
Thorough preparation can make a significant difference in your performance during a safety officer interview. Understanding the company’s specific safety needs, aligning your responses with their culture, and confidently showcasing your expertise will set you apart from other candidates.
50 Process Safety Interview Questions and Answers | Free Download
50 Industrial Safety Interview Questions and Answers | Free Download
Safety Professional Interview Questions
40 Aramco Safety Engineer Interview Questions and Sample Answers | Free Download PDF
FAQs
How Do I Prepare for a Safety Officer Interview?
Research the company, review safety regulations, and practice answering common questions. Mock interviews can help boost your confidence.
What Are the Most Common Questions Asked in Safety Interviews?
Expect questions about your technical knowledge, regulatory expertise, and ability to handle real-life scenarios.
How Can I Prove My Expertise in Safety?
Highlight certifications, share measurable achievements, and demonstrate knowledge of industry-specific safety challenges.
Do I Need Certification to Be a Safety Officer?
Certifications like OSHA, NEBOSH, or CSP are often required and can enhance your credibility.
What Should I Avoid During the Interview?
Avoid vague answers, overconfidence, or lack of preparation. Stay professional and focus on showcasing your skills and experience.
Very help full your chennal
I’m very interested to learn and upgrade my knowledge and to develop my skills as well.