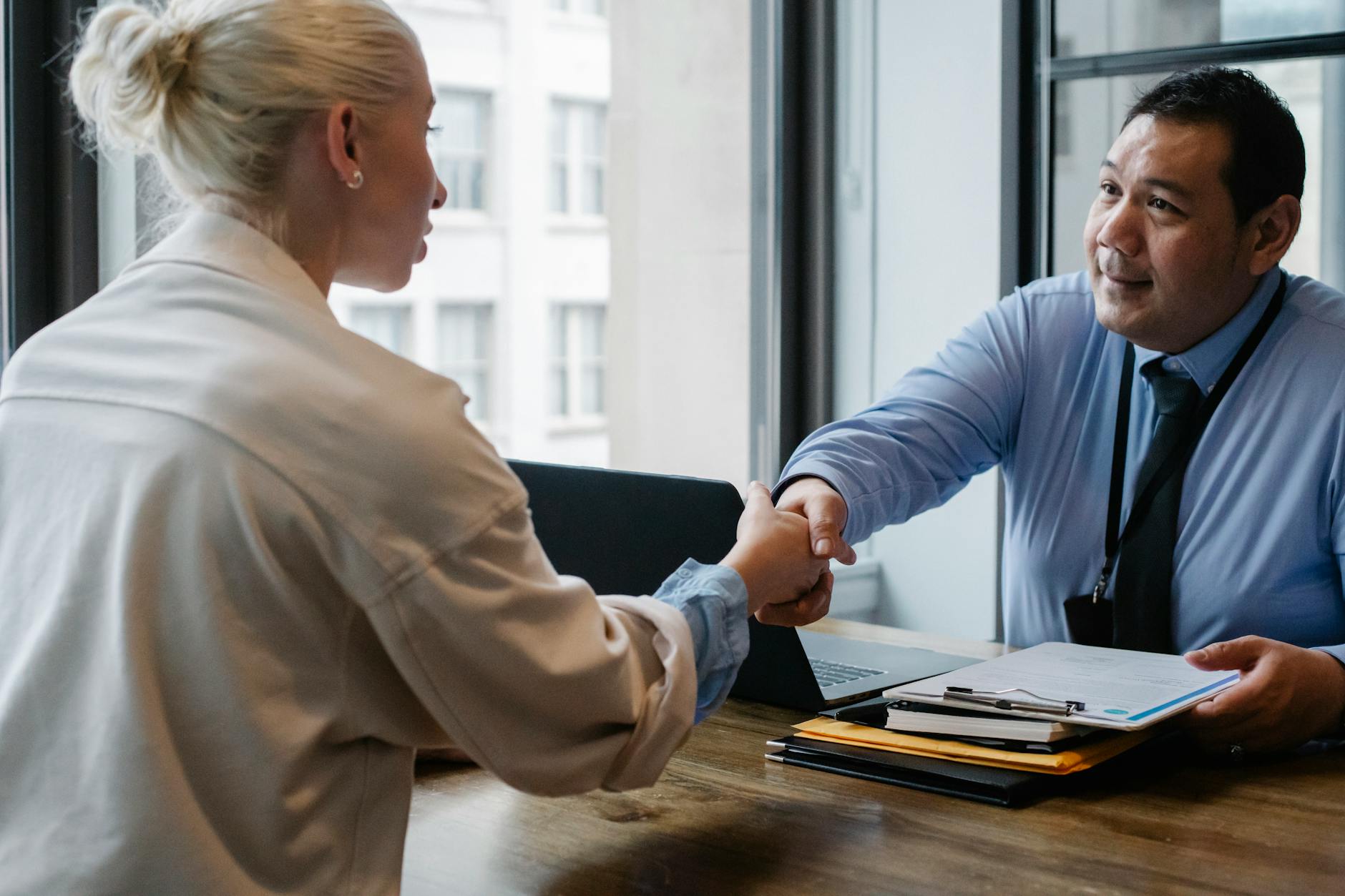
Safety Engineer: 100+ Safety Engineer Job Interview Questions with Sample Answers
Introduction to Safety Engineers
A Safety Engineer plays a critical role in ensuring workplace safety by identifying, assessing, and minimizing risks. They are responsible for designing and implementing safety procedures, ensuring compliance with safety regulations, and fostering a safety-conscious culture. Safety Engineers are employed across various industries, including construction, manufacturing, oil & gas, and healthcare.
Key Skills and Qualifications of a Safety Engineer
To excel as a Safety Engineer, specific skills and qualifications are necessary:
- Education Requirements: Most Safety Engineers hold at least a bachelor’s degree in industrial engineering, safety management, or a related field.
- Certifications and Training: Certifications like OSHA (Occupational Safety and Health Administration) or NEBOSH (National Examination Board in Occupational Safety and Health) can enhance credibility.
- Essential Skills: Knowledge of safety protocols, risk management, attention to detail, communication, and problem-solving are essential for a Safety Engineer’s success.
Preparing for a Safety Engineer Job Interview
When preparing for a Safety Engineer interview, focus on the following:
- Understanding the Role and Responsibilities: Review the job description and understand what is expected of you as a Safety Engineer.
- Researching the Company: Get to know the company’s safety standards, culture, and past safety incidents.
- Importance of Mock Interviews and Practice: Practicing with mock interviews will help you answer confidently and clearly.
Here’s a comprehensive list of 100+ Safety Engineer job interview questions along with sample answers to help you prepare for an interview:
1. Tell us about your experience as a Safety Engineer.
Answer: “I have over [X] years of experience working as a Safety Engineer in industries such as [mention industries]. I have a strong background in conducting risk assessments, implementing safety protocols, and ensuring compliance with local and international regulations. My role has involved monitoring safety standards, training staff, and developing emergency procedures.”
2. What safety standards are you familiar with?
Answer: “I am well-versed in OSHA, NFPA, ISO 45001, and other relevant safety standards. I also keep up to date with industry-specific regulations to ensure all safety protocols are in line with the latest guidelines.”
3. How do you approach risk assessments?
Answer: “I start with identifying potential hazards, assessing the risks associated with them, and determining their likelihood and impact. Then, I prioritize the risks and suggest controls to minimize or eliminate them. I often collaborate with teams to implement preventive measures and ensure continuous monitoring.”
4. How do you handle a safety violation at the workplace?
Answer: “First, I investigate the violation to understand its severity and root cause. Then, I take appropriate corrective action, which may include retraining, issuing warnings, or revising safety procedures. I also ensure that measures are put in place to prevent future violations.”
5. Can you explain the importance of PPE in the workplace?
Answer: “Personal Protective Equipment (PPE) is essential to protect employees from hazards that cannot be eliminated through engineering controls or administrative procedures. PPE is critical in ensuring the safety of workers, especially in high-risk environments like construction sites, chemical plants, or manufacturing facilities.”
6. How do you ensure compliance with safety regulations?
Answer: “I regularly conduct audits, inspections, and safety training sessions to ensure that all safety measures are being followed. Additionally, I collaborate with management to ensure that the company is staying up to date with any regulatory changes and that any non-compliance issues are addressed promptly.”
7. Describe a time you improved safety in your workplace.
Answer: “At my previous job, I noticed a high number of near-miss incidents related to improper machine operation. I initiated a safety training program that focused on machine handling, and we introduced a buddy system for new employees. As a result, we saw a significant reduction in near-misses and improved overall safety awareness.”
8. How would you conduct a safety audit?
Answer: “I would start by reviewing safety records and regulations relevant to the workplace. I would then conduct site inspections, interviewing employees to ensure they are aware of safety protocols. Finally, I would compile findings and make recommendations for improvements.”
9. What safety measures would you take for an industrial site?
Answer: “For an industrial site, I would assess potential hazards like chemical exposure, machinery accidents, fire risks, and fall hazards. I’d implement comprehensive safety protocols including PPE use, fire safety procedures, emergency evacuation plans, and regular training programs to ensure the team is prepared.”
10. How do you stay updated on safety regulations?
Answer: “I attend workshops, webinars, and conferences related to workplace safety. I also regularly read industry publications and keep in touch with safety professionals through networking groups to ensure I’m aware of any new regulations or best practices.”
11. What do you think is the most important aspect of a safety program?
Answer: “I believe the most important aspect is effective communication. Safety programs must be clear, easily understood, and regularly reinforced with training. It’s essential that employees feel confident reporting hazards and believe that their safety is a top priority.”
12. How do you handle emergencies at the workplace?
Answer: “In the event of an emergency, my first priority is ensuring the safety of all employees. I would follow the emergency response plan, assist in evacuations, provide first aid if necessary, and ensure that appropriate emergency services are contacted. After the incident, I would conduct a debrief to evaluate the response and improve future procedures.”
13. What do you consider the most challenging aspect of being a Safety Engineer?
Answer: “The most challenging aspect is ensuring consistent compliance across all levels of an organization. While most employees are receptive to safety guidelines, some may become complacent over time, which requires constant reinforcement and new strategies to maintain safety awareness.”
14. How do you conduct a root cause analysis?
Answer: “I use tools like the 5 Whys or Fishbone Diagram to identify the root cause of an incident or near miss. After identifying the underlying issue, I work with the team to develop corrective actions and prevent recurrence. I ensure to follow up on these actions to confirm they are effective.”
15. Explain the concept of “Hierarchy of Controls.”
Answer: “The Hierarchy of Controls is a system used to minimize or eliminate exposure to hazards. The levels, from most to least effective, are: Elimination, Substitution, Engineering Controls, Administrative Controls, and Personal Protective Equipment (PPE). The goal is to control hazards at their source, rather than relying solely on PPE.”
16. Have you ever faced resistance from employees regarding safety protocols? How did you handle it?
Answer: “Yes, I have faced resistance, especially when new protocols were introduced. In such cases, I take the time to explain the reasons behind the changes and engage with employees to address their concerns. I also provide training and support to help them feel more comfortable with the new procedures.”
17. What safety certifications do you hold?
Answer: “I hold certifications such as NEBOSH, OSHA 30-hour, and [mention other relevant certifications], which have equipped me with the knowledge to manage safety hazards and ensure compliance with regulatory standards effectively.”
18. Can you describe a situation where you had to deal with a safety-related crisis?
Answer: “In a previous role, we experienced a chemical spill that required immediate attention. I coordinated with emergency responders and ensured proper containment measures were in place. We successfully mitigated the risk to employees and the environment, and I conducted a thorough investigation afterward to update our safety protocols.”
19. What safety software are you familiar with?
Answer: “I have experience using software such as SAP EHS, Intelex, and Pro-Sapien, which help in tracking safety incidents, managing safety documentation, and ensuring compliance with safety regulations.”
20. Why do you think safety should be a top priority in any organization?
Answer: “Safety is a fundamental aspect of employee well-being and organizational efficiency. A safe workplace reduces injuries, boosts employee morale, and ensures compliance with legal requirements. It also contributes to the overall success of a company by preventing costly accidents and improving productivity.”
21. How would you manage safety in a multi-site operation?
Answer: “Managing safety across multiple sites requires a consistent approach while adapting to site-specific needs. I would standardize safety protocols across all locations, conduct regular audits, and ensure clear communication between site managers and safety officers. I’d also implement regular safety meetings and share best practices to ensure that all locations are aligned with company-wide safety standards.”
22. What is your experience with safety training programs?
Answer: “I have developed and implemented several safety training programs, including hazard identification, emergency response, and specific training for high-risk activities like confined space entry and working with hazardous materials. I ensure these programs are engaging and practical, allowing employees to demonstrate their knowledge and skills. I also track progress and provide refresher courses to keep the team updated.”
23. How do you handle accidents in the workplace?
Answer: “I follow a clear process after an accident, including immediate response to ensure the safety of those involved, providing first aid if needed, and notifying emergency services. Afterward, I conduct a thorough investigation to determine the root cause and implement corrective actions to prevent recurrence. I also ensure proper documentation for compliance and future training.”
24. What steps would you take if you observed unsafe practices on-site?
Answer: “First, I would intervene immediately to stop the unsafe practice and address the hazard to prevent accidents. Then, I would investigate the situation to understand why the unsafe behavior occurred and provide corrective action, whether it’s retraining, revising protocols, or reinforcing safety procedures with the team. I also emphasize fostering a culture of safety, where employees feel comfortable reporting concerns.”
25. Can you give an example of how you improved a safety process?
Answer: “In my previous role, I identified that our incident reporting process was cumbersome and led to delays in addressing hazards. I worked with the team to streamline the reporting process, integrating an easy-to-use software tool that allowed employees to report safety concerns instantly. As a result, we saw faster response times and more proactive hazard mitigation.”
26. How do you balance safety requirements with production goals?
Answer: “Safety is never negotiable, but I understand the importance of production goals. I work closely with production teams to identify risks in advance and design safety procedures that do not interfere with operational efficiency. My goal is to create a safety program that enhances productivity by reducing accidents and downtime while maintaining a safe working environment.”
27. How would you assess the safety culture within an organization?
Answer: “I would assess the safety culture through employee surveys, interviews, and observation of daily practices. I’d look at the frequency and quality of safety meetings, employee engagement in safety activities, and how quickly safety concerns are addressed. A strong safety culture is one where safety is prioritized, and employees are actively involved in identifying and mitigating risks.”
28. What steps would you take if an employee refuses to follow safety protocols?
Answer: “If an employee refuses to follow safety protocols, I would first have a private conversation to understand the reason behind their refusal. I’d address any concerns they may have and emphasize the importance of safety for their well-being and the team’s. If the behavior continues, I would follow the company’s disciplinary procedures, which may include warnings or further action, always ensuring the safety of the workplace is upheld.”
29. What is your experience with accident investigations?
Answer: “I have conducted several accident investigations, using methods such as root cause analysis and interviews to gather all relevant information. I focus on understanding the sequence of events that led to the accident and identifying systemic issues. After the investigation, I recommend corrective actions, and I ensure that lessons learned are shared with the broader team to prevent future incidents.”
30. What do you think is the most effective way to promote safety awareness?
Answer: “The most effective way to promote safety awareness is through continuous training, open communication, and leading by example. Encouraging employees to actively participate in safety programs, sharing real-life case studies, and recognizing safety achievements are all excellent ways to keep safety at the forefront of everyone’s mind. Regularly scheduled safety drills also help reinforce these lessons.”
31. How do you handle confidential safety-related information?
Answer: “I handle all safety-related information with the utmost confidentiality, adhering to company policies and regulations. I ensure that sensitive information is shared only with relevant personnel and securely stored to prevent unauthorized access. I also ensure compliance with any legal requirements related to the handling of accident reports and employee medical records.”
32. What is your approach to maintaining safety in high-risk industries like construction or chemicals?
Answer: “In high-risk industries, my approach involves rigorous planning, thorough risk assessments, and implementing detailed safety protocols. I prioritize regular safety inspections, hazard identification, and training specific to the risks of the industry. For example, in construction, I ensure fall protection systems are in place, and in chemical industries, I ensure proper handling and storage of hazardous materials, along with ensuring personal protective equipment (PPE) is used at all times.”
33. How do you handle the implementation of new safety technologies or equipment?
Answer: “When introducing new safety technologies or equipment, I ensure that all employees are properly trained on how to use it safely. I conduct training sessions, provide detailed manuals, and involve employees in hands-on demonstrations. I also monitor the integration of the new technology to ensure it improves safety without disrupting operations.”
34. How do you handle conflicts between safety and other departments?
Answer: “I approach conflicts with a collaborative mindset. I listen to the concerns of other departments, explain the rationale behind safety protocols, and work together to find solutions that maintain safety while also addressing the department’s needs. I believe in fostering open communication and ensuring that safety isn’t seen as an obstacle but as an integral part of the company’s success.”
35. How do you evaluate the effectiveness of a safety program?
Answer: “I evaluate safety programs through metrics such as the frequency of accidents, near misses, and the completion of safety audits. I also solicit feedback from employees to understand their perception of the program and identify areas for improvement. Regular review of safety data and ongoing training ensures that the program remains effective and relevant.”
36. Can you discuss any experience you have with environmental safety?
Answer: “I have experience managing environmental safety, including waste disposal, chemical spills, and air quality monitoring. I’ve worked closely with environmental teams to ensure compliance with regulations such as EPA guidelines and local environmental laws. I also help identify areas where sustainability and safety can go hand in hand, implementing greener alternatives where possible.”
37. What motivates you to pursue a career in safety engineering?
Answer: “I’m motivated by the ability to make a tangible difference in people’s lives. Ensuring the safety and well-being of employees while reducing workplace accidents is incredibly fulfilling. I enjoy problem-solving and identifying proactive solutions to prevent incidents, and I find it rewarding to contribute to a positive safety culture.”
38. How do you approach conducting a safety audit?
Answer: “I begin by reviewing the company’s safety records and policies to ensure they align with industry standards and legal requirements. I then conduct a physical site inspection, looking for hazards and areas of non-compliance. I interview employees to understand their safety awareness, and I review past incidents for patterns. Finally, I compile my findings into a detailed report with actionable recommendations.”
39. What is your experience with emergency response planning?
Answer: “I’ve developed and implemented emergency response plans for various situations, including fires, chemical spills, and natural disasters. I ensure these plans are well-communicated to employees through training drills and easy-to-understand protocols. Additionally, I review and update emergency procedures regularly to ensure they are effective in real-life situations.”
40. How do you handle the integration of safety procedures in a new project?
Answer: “When a new project starts, I collaborate with project managers and team leaders to assess potential risks. I ensure that safety procedures are integrated from the planning stage, including risk assessments, hazard identification, and equipment checks. I also make sure that all personnel receive the necessary safety training and that safety measures are consistently reviewed throughout the project’s lifecycle.”
41. How do you handle safety concerns from employees?
Answer: “When employees raise safety concerns, I make it a priority to listen and investigate the issue thoroughly. I encourage open communication and ensure that employees feel their concerns are taken seriously. After gathering the necessary information, I collaborate with relevant departments to address the issue, whether it’s through corrective actions, updated training, or changes to existing procedures.”
42. How would you ensure that contractors adhere to safety standards?
Answer: “Before allowing contractors to begin work, I ensure they are thoroughly briefed on the site’s safety standards and procedures. I conduct regular safety inspections and audits during their work to ensure compliance. I also require contractors to provide proof of their safety training, certifications, and safety records. Regular meetings with contractors help ensure ongoing alignment with safety requirements.”
43. How do you assess the risks associated with new equipment or machinery?
Answer: “When new equipment or machinery is introduced, I perform a risk assessment to identify potential hazards associated with its use. This includes evaluating potential mechanical failures, electrical risks, and ergonomic concerns. I collaborate with engineers and operators to ensure that safety protocols, such as lockout/tagout procedures, are implemented and that employees are properly trained in its use.”
44. What role does leadership play in workplace safety?
Answer: “Leadership plays a critical role in setting the tone for workplace safety. A strong leadership team ensures that safety is prioritized at all levels, models safe behaviors, and allocates the resources necessary for safety programs to succeed. Leaders should encourage open communication and foster a culture where safety is considered a shared responsibility.”
45. How do you track safety performance and improvements?
Answer: “I track safety performance by analyzing data such as incident reports, near misses, and audit results. I use tools like safety management software to monitor trends and identify areas for improvement. Key performance indicators (KPIs) such as accident rates, training completion rates, and hazard mitigation success are useful for measuring safety performance and ensuring continuous improvement.”
46. What strategies would you use to prevent workplace fatigue-related incidents?
Answer: “To prevent fatigue-related incidents, I would implement rotating shifts to prevent long hours of continuous work. I would encourage regular breaks and ensure that employees have access to sufficient rest periods. Additionally, I would educate employees on the importance of sleep and proper nutrition for maintaining high energy levels and focus during work hours.”
47. What is the most critical element of an emergency evacuation plan?
Answer: “The most critical element of an emergency evacuation plan is ensuring that all employees know their roles and the evacuation routes. The plan must be clearly communicated, regularly practiced through drills, and accessible to everyone. Regular updates should be made to the plan based on changes in the workplace layout, staffing, or potential hazards.”
48. What are some common causes of workplace accidents, and how can they be prevented?
Answer: “Common causes of workplace accidents include inadequate training, lack of proper safety equipment, unsafe work practices, and environmental factors like poor lighting or slippery surfaces. To prevent these, I ensure that proper training is provided, safety protocols are in place, and equipment is regularly maintained. I also conduct regular hazard assessments to identify and mitigate risks before they lead to accidents.”
49. How do you ensure that safety training is effective?
Answer: “I ensure safety training is effective by making it interactive and engaging. I use a mix of methods, including hands-on demonstrations, safety videos, and group discussions. I also provide opportunities for employees to ask questions and share experiences. Finally, I assess the effectiveness of training through tests, observations, and follow-up evaluations to ensure the knowledge is retained and applied on the job.”
50. Can you explain the concept of “Safety First” in the workplace?
Answer: “‘Safety First’ means making safety a top priority in all aspects of the workplace. It involves consistently assessing and addressing potential risks, ensuring that employees have the necessary tools and training to work safely, and fostering a culture where safety is everyone’s responsibility. By committing to safety first, organizations can reduce accidents and create a safer work environment for all employees.”
51. How do you manage multiple safety priorities at once?
Answer: “When faced with multiple safety priorities, I focus on assessing the severity and urgency of each issue. I prioritize high-risk areas that could lead to serious incidents and ensure those are addressed first. I use project management tools to track progress on various tasks and maintain regular communication with team members to ensure all priorities are being managed effectively.”
52. What is your approach to conducting safety inspections?
Answer: “I conduct safety inspections by starting with a review of previous inspection reports and any known issues. I then systematically inspect all areas of the facility, paying close attention to high-risk areas. I check that safety equipment is functioning properly, employees are using PPE, and that all safety procedures are being followed. After the inspection, I provide feedback and recommendations for improvements.”
53. How do you ensure that safety procedures are integrated into daily operations?
Answer: “To integrate safety procedures into daily operations, I make safety part of the company’s culture. I ensure safety protocols are included in job descriptions, daily briefings, and pre-shift meetings. I also encourage supervisors to hold regular safety checks and create a feedback loop where employees can report hazards and suggest improvements.”
54. Have you worked with any international safety regulations?
Answer: “Yes, I have experience working with international safety regulations such as ISO 45001 for Occupational Health and Safety, as well as specific regulations like the European Union’s REACH for chemicals. I understand the importance of compliance with local and international standards and have worked to ensure that safety procedures meet or exceed these guidelines.”
55. What do you think are the most critical safety concerns for the oil and gas industry?
Answer: “In the oil and gas industry, some of the most critical safety concerns include fire and explosion hazards, exposure to toxic chemicals, and the risk of equipment failures. I ensure that proper safety protocols are in place for working with hazardous materials, regular safety audits are conducted on equipment, and that employees are equipped with the necessary PPE and emergency response training.”
56. How do you handle safety concerns during construction projects?
Answer: “During construction projects, I focus on hazard identification and ensuring that proper safety protocols are in place for activities such as working at heights, operating heavy machinery, and handling hazardous materials. I ensure that all workers are properly trained, PPE is used, and that safety meetings are held regularly. I also monitor the project site continuously to address any potential safety issues before they escalate.”
57. How do you assess the safety of new processes or technologies?
Answer: “When new processes or technologies are introduced, I perform a thorough risk assessment to identify potential hazards. This involves evaluating the process or technology for safety concerns, considering historical data from similar industries or applications, and consulting with engineers and operators. I then recommend mitigation strategies and ensure that safety measures are in place before implementation.”
58. What is your experience with emergency response drills?
Answer: “I have organized and participated in several emergency response drills, including fire, chemical spill, and evacuation drills. I ensure that these drills are realistic, involve all employees, and are followed by a debrief to identify areas for improvement. Regular drills are crucial in ensuring that employees are prepared to respond effectively in an emergency.”
59. What role do safety committees play in maintaining a safe workplace?
Answer: “Safety committees are an essential part of maintaining a safe workplace. They provide a platform for employees to raise safety concerns, suggest improvements, and actively participate in safety initiatives. By involving employees at all levels, safety committees help build a culture of safety, improve safety awareness, and ensure that safety policies are relevant and effective.”
60. How do you stay motivated to maintain high safety standards?
Answer: “I stay motivated by knowing that my work directly contributes to the well-being of employees and the overall success of the organization. Seeing the positive impact of improved safety practices, such as reduced accidents and increased employee satisfaction, keeps me motivated. Additionally, I am driven by the challenge of continuously improving safety standards and keeping up with evolving regulations and best practices.”
61. How do you ensure that safety policies are compliant with industry standards and regulations?
Answer: “I stay up to date with the latest industry standards and regulatory changes by attending safety conferences, reading safety publications, and participating in professional organizations. I also conduct regular reviews of the safety policies and procedures to ensure they align with local, national, and international regulations. Additionally, I work closely with legal and compliance teams to ensure our practices meet all regulatory requirements.”
62. How do you handle situations where safety equipment is not available or is malfunctioning?
Answer: “If safety equipment is unavailable or malfunctioning, my first step is to ensure the equipment is repaired or replaced as soon as possible. I would communicate the issue to all relevant employees and ensure they understand the risks of continuing work without the necessary safety measures in place. In the meantime, I would implement interim safety controls to mitigate any immediate risks, such as alternative protective measures or halting high-risk activities until the equipment is fully functional.”
63. What steps would you take to improve safety in a high-risk environment?
Answer: “In a high-risk environment, I would start by conducting a thorough hazard analysis and risk assessment to identify all potential dangers. I would then ensure that safety protocols are clearly defined and enforced, provide specialized training for high-risk tasks, and ensure the availability of proper personal protective equipment (PPE). I would also establish a robust system for reporting hazards, conduct frequent safety audits, and ensure regular emergency response drills to prepare for any potential incidents.”
64. How do you ensure that employees remain engaged in safety programs?
Answer: “Employee engagement in safety programs is essential for their success. To keep employees engaged, I would make safety training interactive and relevant to their daily tasks. I would encourage participation by recognizing safety achievements, offering incentives for safety milestones, and creating an open environment where employees feel comfortable discussing safety issues. I also ensure that safety policies are regularly reviewed and updated to maintain relevance and effectiveness.”
65. How do you deal with resistance to safety changes or new procedures?
Answer: “Resistance to change is common, so I approach it by first understanding the concerns of employees and providing clear communication about the reasons behind the change. I would involve employees in the process, asking for their feedback and addressing any misconceptions. I ensure that the benefits of the new safety procedures are clear, and I provide necessary training and support to help everyone adjust to the changes.”
66. What methods do you use to assess the effectiveness of safety training programs?
Answer: “To assess the effectiveness of safety training programs, I use a combination of methods. This includes testing employees’ knowledge through quizzes or assessments, observing their behavior on-site, and conducting feedback sessions after training. Additionally, I monitor the number of incidents and near misses before and after training to see if there has been a reduction in accidents. Continuous evaluations help refine and improve future training sessions.”
67. What do you consider the most important aspect of a safety program?
Answer: “The most important aspect of a safety program is ensuring that it is proactive rather than reactive. A successful safety program anticipates potential risks, educates employees, and fosters a culture where safety is prioritized by everyone, from management to workers on the ground. This includes thorough risk assessments, clear safety protocols, ongoing training, and a system for reporting hazards or unsafe practices.”
68. How do you handle safety documentation and reporting?
Answer: “I ensure that all safety documentation is meticulously maintained and complies with relevant regulations. This includes keeping accurate records of safety inspections, training sessions, incident reports, and corrective actions taken. I make sure all reports are easily accessible and organized for quick reference in case of audits or investigations. I also ensure that reporting is timely and that management is kept informed of key safety metrics and any significant incidents.”
69. How do you evaluate and select personal protective equipment (PPE) for employees?
Answer: “When selecting PPE, I start by identifying the specific hazards employees may encounter, such as chemical exposure, high noise levels, or working at heights. I then evaluate the types of PPE that will offer the best protection for these risks while considering comfort and fit to ensure compliance. I also ensure that the PPE meets industry standards and regulations, and I provide training to employees on how to use it correctly.”
70. What is your experience with safety audits and inspections?
Answer: “I have extensive experience conducting safety audits and inspections to assess compliance with safety regulations and identify potential hazards. I ensure that all areas of the facility are inspected, focusing on high-risk areas like machinery, storage areas, and high-traffic zones. After each audit, I compile a detailed report with corrective actions and recommendations. I follow up on any findings to ensure that improvements are made in a timely manner.”
71. How would you handle a situation where safety standards are not being followed by management?
Answer: “If safety standards are not being followed by management, I would address the issue directly and professionally. I would first present the facts, explaining how not following safety standards can affect the well-being of employees and the company’s reputation. If necessary, I would provide data on past incidents or near misses to highlight the risk. I would also recommend solutions and stress the importance of leadership in setting a positive example for the rest of the team.”
72. What role do safety incentives and rewards play in a safety program?
Answer: “Safety incentives and rewards play an important role in reinforcing safe behaviors and promoting a safety-first culture. I believe that recognizing and rewarding employees for safe work practices motivates them to maintain those behaviors. Rewards can range from public recognition to more tangible rewards such as bonuses or extra time off. The key is to ensure that the rewards are fair and align with the overall safety goals of the organization.”
73. How do you ensure compliance with local and international safety regulations?
Answer: “I ensure compliance by staying current on both local and international safety regulations through continuous research, attending industry conferences, and participating in safety-focused groups. I regularly review company policies and safety protocols to make sure they align with the latest regulations and legal requirements. Additionally, I conduct regular audits to ensure that all practices are compliant and provide training to employees on any changes in the regulations.”
74. How would you address a situation where an employee is consistently unsafe?
Answer: “If an employee is consistently unsafe, I would first have a one-on-one conversation to understand the root cause of the behavior. I would explain the risks involved and the potential consequences for both the employee and the team. I would also provide additional training or resources if needed and set clear expectations for improvement. If the unsafe behavior continues, I would follow the company’s disciplinary procedures, which may involve warnings or further action.”
75. How do you ensure that safety is incorporated into the project planning phase?
Answer: “To incorporate safety into the project planning phase, I work closely with project managers and engineers to assess potential risks and design safety protocols tailored to the project’s specific requirements. I ensure that safety considerations are included in the project timeline and budget, such as allocating resources for PPE, safety training, and risk assessments. I also ensure that safety goals are part of the project’s overall objectives from the beginning.”
76. Can you give an example of how you’ve improved safety reporting systems?
Answer: “In my previous role, I noticed that the safety reporting system was slow and difficult for employees to use, leading to delays in reporting hazards. I worked with the IT department to implement a user-friendly, digital reporting tool that allowed employees to report safety concerns quickly and from their mobile devices. This improved response times, encouraged more employees to report hazards, and helped us address issues more proactively.”
77. How do you handle the documentation and management of chemical safety data sheets (SDS)?
Answer: “I ensure that all chemical safety data sheets (SDS) are properly organized and readily accessible to all employees who handle chemicals. I maintain an updated digital database of SDS, and I ensure that printed copies are available in key areas. I also ensure that employees are trained on how to read and interpret the SDS and that they understand the risks associated with the chemicals they are working with.”
78. What steps would you take to create a safety culture within a company?
Answer: “Creating a safety culture starts with leadership setting the example and prioritizing safety in all aspects of operations. I would implement comprehensive training, regular safety meetings, and open communication channels to encourage employees to actively participate in safety initiatives. I would also encourage employees to report hazards and unsafe behaviors, recognize and reward safe practices, and make safety an integral part of the company’s values.”
79. How do you handle multiple conflicting priorities in safety management?
Answer: “When handling multiple conflicting priorities, I assess the risks associated with each issue to determine which requires immediate attention. I prioritize actions based on severity and potential impact, ensuring that critical safety concerns are addressed first. I communicate with all stakeholders to ensure alignment and transparency about the rationale behind prioritizing certain tasks, and I delegate tasks to ensure that all priorities are managed efficiently.”
80. How do you stay current with the latest safety trends and technologies?
Answer: “I stay current with the latest safety trends and technologies by attending safety conferences, participating in webinars, reading industry journals, and networking with other safety professionals. I also follow regulatory bodies, such as OSHA and ISO, to stay informed about the latest standards and best practices. Additionally, I continually assess new technologies that can improve safety and efficiency within the workplace.”
81. What’s your approach to managing safety in high-risk industries, such as construction or manufacturing?
Answer: “In high-risk industries, my approach is to ensure that safety is embedded in every phase of the operation, from planning to execution. This involves conducting thorough risk assessments, ensuring all safety protocols are in place, and providing specific training for the hazards employees will face. I focus on clear communication of safety standards and maintaining regular audits and safety checks. I also emphasize the importance of a safety-first mindset, where every employee, from management to ground-level workers, is responsible for maintaining a safe environment.”
82. How do you manage the safety of subcontractors and third-party vendors?
Answer: “For subcontractors and third-party vendors, I ensure that they comply with our safety standards by reviewing their safety records and certifications before they begin work. I also conduct safety orientations for their teams and ensure they’re aware of the site-specific safety hazards. During the project, I monitor their work, conduct safety audits, and maintain an open line of communication to address any safety concerns promptly. I make it clear that any non-compliance will result in corrective actions or termination of their contract.”
83. What is your experience with implementing a Safety Management System (SMS)?
Answer: “I have experience implementing and managing a Safety Management System (SMS) in accordance with industry standards. The SMS helps streamline safety procedures, track performance, and ensure compliance with regulations. I typically start by conducting a thorough risk assessment, followed by designing a system that includes clear safety policies, training programs, incident reporting procedures, and audit systems. I also ensure that the system is continuously reviewed and updated based on feedback, incidents, and changing regulations.”
84. How would you address a situation where an employee refuses to follow safety protocols?
Answer: “If an employee refuses to follow safety protocols, I would first approach them calmly and privately to understand their reasons for non-compliance. I would remind them of the importance of the protocols for their safety and the safety of their colleagues. I would also provide further training if necessary to address any misunderstandings or gaps in knowledge. If the behavior continues, I would escalate the issue according to the company’s disciplinary procedures, which may involve formal warnings or other corrective actions.”
85. Can you explain your process for incident investigation and reporting?
Answer: “When an incident occurs, my first step is to ensure that the scene is safe and secure. Then, I begin the investigation by gathering facts, interviewing witnesses, and reviewing any available evidence, such as video footage or equipment logs. I look for root causes, whether they are related to equipment failure, human error, or procedural gaps. Once the investigation is complete, I compile a detailed report with corrective actions, recommendations for preventing similar incidents, and an analysis of any patterns. I then share this report with management and ensure the corrective actions are implemented.”
86. How do you handle situations where safety procedures conflict with production goals?
Answer: “I believe that safety should never be compromised, even in the pursuit of production goals. In situations where safety procedures conflict with production demands, I would engage in open dialogue with the production team to discuss the risks involved and seek alternatives that ensure safety is prioritized while still meeting production targets. If necessary, I would work with management to adjust timelines or procedures to minimize risk without sacrificing safety standards. The key is to strike a balance and ensure that safety is always the top priority.”
87. What would you do if you discovered unsafe working conditions in the workplace?
Answer: “If I discovered unsafe working conditions, I would immediately assess the severity of the hazard and take action to protect workers. If the situation presents an immediate danger, I would stop work and ensure that employees are moved to a safe area. I would then investigate the root cause of the unsafe condition, implement corrective actions, and ensure proper communication with all stakeholders. I would also document the findings and report the issue according to the company’s incident management protocol.”
88. How do you ensure that safety standards are communicated effectively across all levels of an organization?
Answer: “Effective communication of safety standards involves using a multi-faceted approach. I ensure that safety standards are included in new hire orientations, safety meetings, and daily briefings. I also post clear, visible safety signage throughout the workplace, and distribute written procedures or guidelines as needed. Additionally, I encourage open communication by creating a platform where employees can voice concerns or ask questions about safety standards. Regularly reviewing these standards with employees helps ensure they remain top of mind.”
89. What are your strategies for promoting mental health and well-being in the workplace?
Answer: “Mental health is an integral part of overall safety. To promote mental well-being, I advocate for creating a supportive work environment where employees feel comfortable discussing mental health challenges. I implement stress management programs, provide resources like Employee Assistance Programs (EAPs), and encourage regular breaks. I also ensure that employees are aware of any mental health resources available to them and work to reduce the stigma around seeking help. Ensuring a healthy work-life balance and providing clear channels for communication are also key strategies.”
90. Can you discuss a time when you had to make a difficult safety-related decision?
Answer: “In my previous role, I had to decide whether to shut down an area of the facility due to a potential safety hazard, even though it would halt production. After assessing the situation and consulting with the team, I made the decision to shut down the area to prevent any potential accidents. It was a tough decision because it impacted production, but ultimately, safety was the priority. The decision was well-received because it demonstrated a commitment to employee safety, and it led to improvements in our risk assessment procedures.”
91. What are some common misconceptions about safety management, and how do you address them?
Answer: “A common misconception is that safety is only about compliance with rules and regulations, when in fact, safety management is a comprehensive system that includes risk assessment, hazard mitigation, training, and continuous improvement. Another misconception is that safety slows down production, but in reality, a safe work environment improves productivity by preventing accidents and reducing downtime. I address these misconceptions by educating employees and management about the benefits of a strong safety culture, emphasizing that safety is an investment in the workforce and business success.”
92. How would you handle a situation where a supervisor or manager is not enforcing safety protocols?
Answer: “If a supervisor or manager is not enforcing safety protocols, I would first address the issue with them privately, to understand their perspective and determine if there’s a lack of understanding or resources. I would emphasize the importance of their role in ensuring the safety of their team and remind them of their responsibility in maintaining a safe work environment. If the issue persists, I would escalate it to higher management, as enforcing safety is critical for both the well-being of employees and the legal compliance of the organization.”
93. How do you ensure that safety is maintained during the commissioning and startup of new equipment or facilities?
Answer: “During the commissioning and startup phases of new equipment or facilities, I ensure that safety is a top priority by conducting detailed risk assessments before operations begin. I ensure that all necessary safety equipment, such as emergency shutoff systems, fire suppression systems, and alarms, are in place and fully functional. I work with the engineering and operations teams to ensure that all safety protocols are clearly defined and that personnel are trained on the new equipment. During the startup, I monitor operations closely for any potential safety hazards and address them promptly.”
94. What are your views on the role of technology in enhancing workplace safety?
Answer: “Technology plays a crucial role in enhancing workplace safety by improving monitoring, reporting, and risk assessment processes. For example, wearable technology can track employees’ movements and alert them to hazardous conditions, while safety management software can help track incidents and generate reports more efficiently. I also see a great deal of potential in using drones for site inspections and AI for predictive maintenance to identify equipment issues before they become safety hazards. Technology allows for quicker responses, better data collection, and proactive safety management.”
95. How do you approach safety for remote or isolated work environments?
Answer: “For remote or isolated work environments, my approach includes ensuring that workers have access to the appropriate safety equipment and emergency response resources. I implement clear communication protocols, such as regular check-ins via satellite or radio, to monitor their safety. I also ensure that employees are trained to handle emergencies independently and that they have access to first-aid kits, emergency plans, and communication devices. Additionally, I conduct thorough risk assessments to anticipate potential hazards specific to the remote location and take steps to mitigate those risks.”
96. What would you do if an employee sustains a minor injury at work?
Answer: “If an employee sustains a minor injury, I would ensure they receive immediate medical attention, either on-site or through a healthcare provider, depending on the severity. I would then complete an incident report, even if the injury is minor, to document the event and identify any contributing factors. Afterward, I would review the work process and safety protocols to ensure that such injuries can be prevented in the future. Additionally, I would encourage the employee to follow up on their recovery and ensure that they are fit to return to work.”
97. How do you balance the demands of safety with the need for operational efficiency?
Answer: “Balancing safety with operational efficiency involves finding ways to integrate safety measures into daily operations without causing unnecessary delays. I work closely with operational teams to streamline processes while maintaining safety standards. This might involve adjusting workflows, implementing new technologies to reduce risks, or conducting time-efficient safety training. By fostering a culture where safety is viewed as an enabler of productivity, employees are more likely to engage with safety protocols as part of their daily routines, ultimately benefiting both safety and efficiency.”
98. How do you manage safety when there are significant changes in operations or procedures?
Answer: “When there are significant changes in operations or procedures, I ensure that safety is prioritized by first conducting a thorough risk assessment to identify potential hazards associated with the changes. I then update safety protocols and procedures accordingly. It’s also critical to provide training to all affected employees to ensure they understand the new processes and how to perform their tasks safely. I communicate any changes clearly and monitor the transition to ensure that safety standards are maintained throughout the process.”
99. What experience do you have with emergency response planning and drills?
Answer: “I have extensive experience in developing and implementing emergency response plans tailored to different types of incidents, including fires, chemical spills, and natural disasters. I ensure that all employees are trained in emergency procedures and conduct regular drills to practice these scenarios. After each drill, I evaluate the response, gather feedback from participants, and identify areas for improvement. I also review and update emergency plans periodically to ensure that they remain effective and align with any changes in operations or regulations.”
100. How do you ensure that safety protocols are followed in environments with frequent personnel turnover?
Answer: “In environments with high turnover, I ensure that safety protocols are consistently followed by implementing a robust onboarding process that includes safety training. I also set up refresher courses for existing employees and create a system of continuous safety reminders, such as safety briefings or toolbox talks, to reinforce key safety practices. I also establish a mentoring or buddy system where experienced employees guide new hires on safety practices, ensuring that safety remains a top priority despite turnover.”
101. What is your experience with safety regulations specific to hazardous materials?
Answer: “I have experience managing safety regulations related to hazardous materials, including compliance with OSHA’s Hazard Communication Standard (HCS) and handling requirements set by local authorities. I ensure that all hazardous materials are clearly labeled, that safety data sheets (SDS) are readily accessible, and that employees are trained on safe handling, storage, and disposal methods. I also implement regular inspections to ensure that storage and handling procedures are in compliance with regulatory standards, and that safety equipment, such as spill containment kits, are available when needed.”
102. How do you approach the safety of employees working with machinery or heavy equipment?
Answer: “For employees working with machinery or heavy equipment, I ensure that proper safety training is provided on the specific equipment they will be using. I enforce the use of personal protective equipment (PPE) and implement lockout/tagout procedures to prevent accidental machine start-up during maintenance or repair work. Regular equipment inspections and maintenance are scheduled to ensure that machines are functioning properly and safely. I also perform risk assessments to identify potential hazards related to machinery and establish protocols for mitigating those risks.”
103. How do you ensure safety during offsite or remote work locations?
Answer: “Safety during offsite or remote work is a critical area, and my approach includes ensuring that workers have all the necessary safety training and equipment before they leave the main site. I ensure that risk assessments are conducted for the remote site, considering environmental factors, such as weather conditions or terrain, and that emergency response plans are in place. Communication tools like radios or satellite phones are provided to ensure workers can contact emergency services if needed. I also schedule regular check-ins to monitor progress and address any safety concerns.”
104. Can you describe a time when you had to implement a corrective action plan after a safety violation?
Answer: “In one instance, after a safety violation occurred where employees were not wearing required PPE in a high-risk area, I immediately conducted an investigation to understand the root cause of the violation. After gathering information, I identified that the lack of PPE enforcement was due to insufficient monitoring and awareness. I implemented a corrective action plan that included increased safety audits, a review of PPE policies with employees, and a reinforcement of safety expectations through meetings and written reminders. I also introduced a reward system for teams consistently adhering to safety practices, which led to improved compliance.”
105. How do you manage safety in highly regulated industries like pharmaceuticals or chemicals?
Answer: “In highly regulated industries such as pharmaceuticals or chemicals, I ensure that safety management systems align with strict industry regulations, including those from regulatory bodies like OSHA, EPA, and local authorities. I conduct regular compliance audits and ensure that all safety procedures are updated in accordance with changing regulations. I also ensure that employees are well-trained on handling hazardous materials, proper use of PPE, and emergency response procedures. Additionally, I maintain detailed documentation of all safety activities and ensure that all equipment meets the necessary safety standards to avoid regulatory penalties.”
106. How do you deal with safety challenges related to contractors working on-site?
Answer: “Managing safety with contractors is critical, as they must follow the same safety standards as permanent employees. I start by ensuring that contractors are fully briefed on the company’s safety protocols before they begin work. I also verify that they have the necessary certifications and that their safety records are in order. While on-site, I ensure that contractors undergo regular safety inspections and that any hazards or unsafe practices are immediately addressed. I encourage open communication between contractors and internal teams to ensure that any safety concerns are promptly reported and resolved.”
107. What steps do you take to handle and report near-miss incidents?
Answer: “Near-miss incidents are treated with the same seriousness as actual incidents. I immediately investigate any near-miss to understand the causes and identify any potential hazards that could lead to more serious incidents. I gather information from all involved parties and review relevant procedures or equipment that might have contributed. After the investigation, I document the incident and implement corrective actions to prevent future occurrences. I also ensure that the near-miss is communicated to all employees, reinforcing the importance of identifying and reporting hazards before they result in accidents.”
108. How do you ensure continuous improvement in workplace safety?
Answer: “Continuous improvement in workplace safety is achieved through regular evaluations and feedback loops. I conduct periodic safety audits, encourage employee participation in safety discussions, and review incident reports to identify patterns or areas of concern. Based on these findings, I implement updated safety procedures, provide additional training, and introduce new safety technologies or equipment. I also set clear safety goals and measure performance against these targets to drive continuous progress. Engaging employees and management in the process helps to create a safety culture where everyone is committed to improvement.”
109. What are the most important skills for a Safety Engineer to possess?
Answer: “A Safety Engineer must have strong analytical skills to identify risks and hazards, as well as the ability to develop effective solutions. Communication skills are crucial to effectively convey safety policies and procedures to employees at all levels. Problem-solving skills are necessary when addressing safety incidents and developing corrective actions. Attention to detail is essential for monitoring compliance and conducting safety inspections. Finally, leadership skills are important for motivating teams and creating a safety-first culture within the organization.”
110. How do you assess and manage risks in a new project or facility?
Answer: “When assessing and managing risks in a new project or facility, I start with a thorough risk assessment to identify potential hazards related to the site’s layout, equipment, and operations. I work with project managers and engineers to review the design and ensure that safety measures are built into the planning phase. I also evaluate the working conditions and potential environmental factors that could pose risks. Based on the findings, I implement appropriate safety controls, develop training plans for workers, and ensure that emergency response procedures are in place before operations begin.”
111. What’s your approach to managing worksite safety for temporary employees or seasonal workers?
Answer: “For temporary or seasonal workers, I ensure they receive the same level of training and safety orientation as full-time employees. I provide specific briefings on the hazards they may face, as well as clear instructions on the use of safety equipment. I also emphasize the importance of following all safety protocols, as their short-term nature does not exempt them from the responsibility of maintaining a safe working environment. I monitor their adherence to safety practices closely and ensure that they receive feedback and support as needed.”
112. How do you manage safety when working with new or untested materials or processes?
Answer: “When working with new or untested materials or processes, I conduct a thorough risk analysis and review any available safety data to identify potential hazards. I consult with experts or suppliers about any unknown risks and ensure that the team is fully trained on the correct handling, storage, and disposal methods. I also perform smaller-scale tests or pilot runs to evaluate the safety of the materials or processes before scaling up. During this time, I monitor all activities closely and make any necessary adjustments to mitigate risk.”
113. How do you manage the safety of employees during extreme weather conditions?
Answer: “During extreme weather conditions, I ensure that employees are kept safe by monitoring weather reports and adjusting work schedules if necessary. I implement specific procedures for working in extreme heat, cold, or storm conditions, such as providing adequate hydration, ensuring proper clothing, and adjusting work hours to avoid peak hazard times. I also set up emergency shelters or safe zones where employees can take breaks during extreme conditions. Communication with employees is key to ensuring they understand the risks and know how to protect themselves in these situations.”
Final Tips for Success in Safety Engineer Interviews
- Dress Appropriately: Dress professionally to make a good first impression.
- Show Enthusiasm and Passion for Safety: Demonstrate your commitment to the safety profession during the interview.
- Prepare Questions for the Interviewer: Asking insightful questions shows that you are truly engaged in the role and company.
Conclusion
Preparation is key to excelling in a Safety Engineer interview. By understanding the job role, practicing common interview questions, and showing your expertise in safety protocols and regulations, you can increase your chances of landing the job.
Safety Officer: 100+ Safety Officer Job Interview Questions with Sample Answers
NEBOSH Closing Interview Questions and Answers PDF Download
Top 50 HSE Officer Job Interview Questions and Sample Answers
NEBOSH Safety Officer Interview Questions and Answers
Construction Safety Officer Interview Questions and Answers
FAQs
- What qualifications do I need to become a Safety Engineer?
- A bachelor’s degree in a related field and certifications like OSHA or NEBOSH are essential.
- How should I prepare for a safety engineer interview?
- Research the company, review the job description, and practice common interview questions.
- What are the key responsibilities of a Safety Engineer?
- Safety Engineers are responsible for risk assessment, safety program implementation, and compliance with safety regulations.
- What are the most common safety protocols a Safety Engineer should know?
- Knowledge of OSHA, PPE usage, emergency procedures, and hazard communication is crucial.
- How do I improve my chances of landing a Safety Engineer job?
- Gain experience, earn relevant certifications, and prepare thoroughly for interviews.