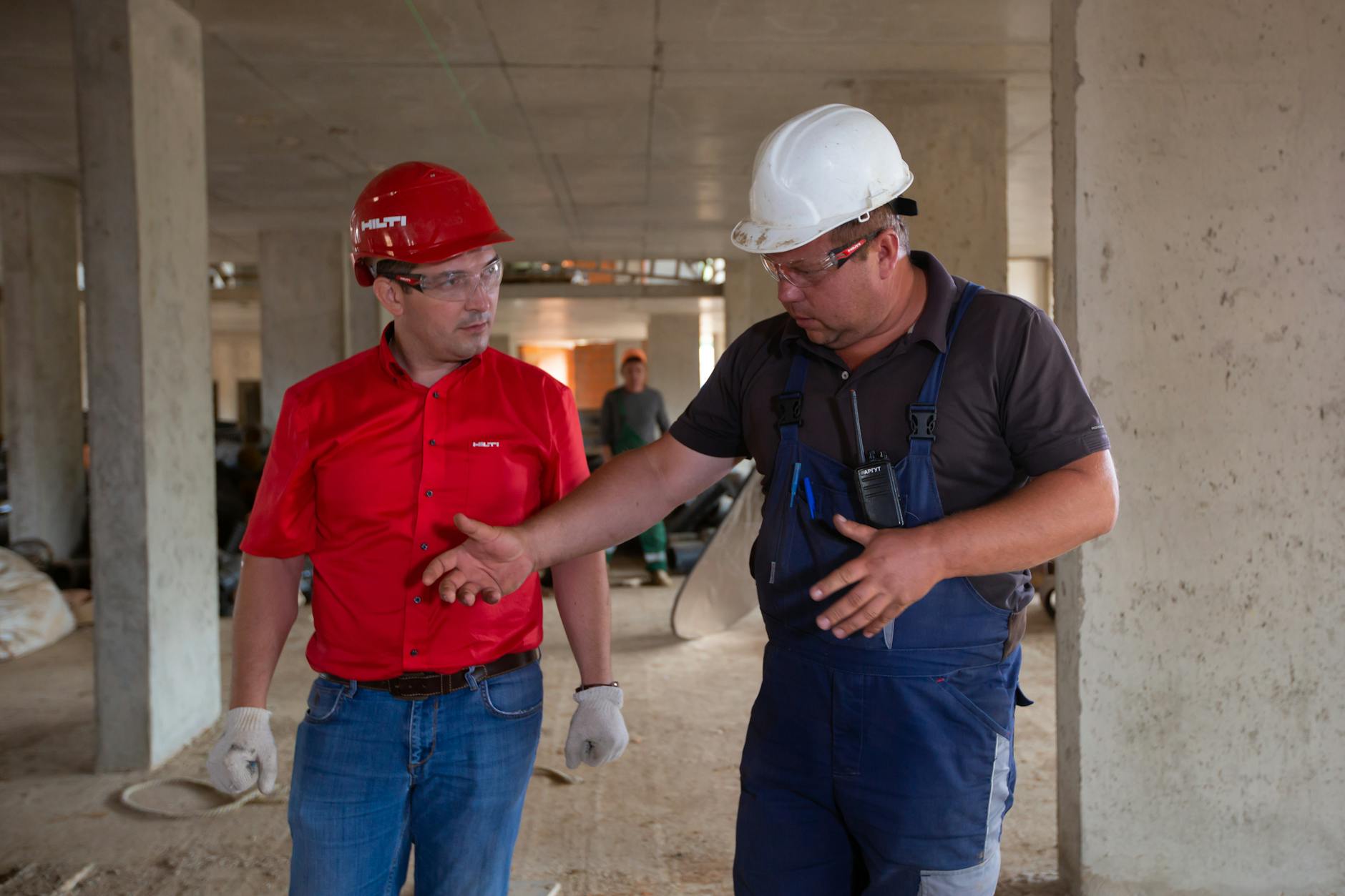
10 Mistakes to Avoid as a New Safety Officer
Introduction
Starting a career as a Safety Officer is a rewarding yet challenging journey. You’re responsible for protecting the health and safety of workers while ensuring compliance with regulatory standards. As a new Safety Officer, it’s natural to make a few missteps. However, some mistakes can compromise safety or lead to costly penalties. Here, we’ll guide you through 10 common pitfalls to avoid, helping you excel and keep everyone on site safe.
Understanding the Role of a Safety Officer
In every industry, from construction to manufacturing, the role of a Safety Officer is vital. Safety Officers are responsible for enforcing safety regulations, conducting inspections, and implementing safety training programs. Their main objective is to reduce workplace accidents, ensure compliance with local and federal laws, and foster a culture of safety.
Mistake #1: Lack of Knowledge on Safety Regulations
One of the biggest errors a new Safety Officer can make is not fully understanding safety regulations. Every industry has unique guidelines, and local laws may vary. Failing to stay informed can result in accidental non-compliance, fines, or increased safety risks. Familiarize yourself with OSHA regulations or any local safety regulations specific to your industry. Remember, knowledge is your first line of defense.
Mistake #2: Ignoring Proper Training
Training is critical for Safety Officers, not only at the start but continually throughout their career. Many new Safety Officers rush into their roles without adequate training or neglect to attend refresher courses. The industry evolves, and so do best practices and safety technology. Enroll in training programs, and encourage your team to do the same.
Mistake #3: Poor Communication Skills
Communication is at the heart of safety. If you’re not effectively communicating safety protocols to the team, misunderstandings and accidents can happen. Develop clear and concise communication skills, whether giving instructions, writing reports, or training workers. Remember, safety protocols should be easily understood by everyone on site.
Mistake #4: Overlooking Risk Assessment
Risk assessments are essential in identifying potential hazards before they cause harm. New Safety Officers may overlook regular assessments or fail to carry them out thoroughly. Conduct risk assessments regularly, focusing on areas prone to hazards. Document findings and take preventive measures based on your assessments.
Mistake #5: Failing to Keep Records
Effective record-keeping is a critical component of safety management. It’s not enough to just address incidents and safety checks; you need to document them properly. Keeping thorough records helps track trends, plan future safety improvements, and provides valuable information if an incident occurs. Make it a habit to maintain accurate and up-to-date records.
Mistake #6: Not Being Proactive
Safety Officers should always be proactive rather than reactive. Waiting for an accident to happen before implementing changes is a serious mistake. Regularly inspect the worksite, look for potential hazards, and address them immediately. Being proactive helps prevent accidents and maintains a safer work environment.
Mistake #7: Focusing Only on Compliance
While compliance is necessary, safety goes beyond ticking boxes. Relying solely on regulatory compliance without fostering a genuine safety culture can lead to a disengaged workforce and potentially unsafe practices. Encourage employees to prioritize safety, and lead by example. Remember, safety is a shared responsibility.
Mistake #8: Underestimating the Importance of PPE
Personal Protective Equipment (PPE) is the last line of defense for workers. As a Safety Officer, you should ensure that employees understand the importance of PPE and wear it correctly. Conduct regular checks to make sure everyone is equipped with the proper PPE for their tasks. A simple reminder can make a big difference in overall safety.
Mistake #9: Ignoring Employee Feedback
Safety Officers are often so focused on inspections and audits that they overlook valuable input from employees. Workers can provide insight into potential hazards they encounter daily. Create a welcoming environment where employees feel comfortable sharing their concerns. Listen to their feedback and use it to enhance your safety strategy.
Mistake #10: Neglecting Emergency Preparedness
Being unprepared for emergencies is a common and costly mistake. Emergency drills, evacuation routes, and equipment checks should be part of your safety plan. Ensure everyone is aware of emergency procedures, and conduct regular drills to keep skills sharp. Emergency preparedness can save lives, so it’s a responsibility no Safety Officer should take lightly.
10 Mistakes to Avoid as a New Safety Officer
Starting as a safety officer in the construction, oil & gas, or any other high-risk industry can be both exciting and challenging. With responsibilities like ensuring the safety and compliance of all employees, avoiding mistakes is essential to ensure a safe working environment. Here are the top 10 mistakes that new safety officers should avoid to build a successful career and maintain workplace safety.
1. Neglecting Proper Risk Assessment
One of the first responsibilities of a safety officer is to assess potential risks. Failing to do a thorough risk assessment can leave employees vulnerable to hazards. Always take time to evaluate the working environment, identify risks, and implement measures to mitigate them. Use safety checklists and consult with team members to identify overlooked risks.
2. Not Establishing Strong Communication Channels
A safety officer’s role is not just about enforcing rules but also about clear communication. Many new safety officers struggle with bridging communication gaps with workers and management. Ensure open lines of communication, encouraging workers to report hazards without fear of retaliation. This transparency fosters a safer work culture.
3. Overlooking the Importance of Regular Training
Training employees regularly on safety protocols is essential. New safety officers may skip training sessions or think it’s enough to train workers once. However, regular refreshers are crucial, especially with changing safety standards and equipment updates. Schedule and document training sessions for all team members.
4. Failing to Document Incidents Properly
Accurate documentation is vital in safety management. Neglecting to document incidents can lead to misunderstandings, legal issues, and missed opportunities for improving safety protocols. Keep a detailed record of any accidents, near-misses, and hazard reports to analyze trends and implement better preventive measures.
5. Ignoring the Value of Personal Protective Equipment (PPE)
Some new safety officers may underestimate the significance of PPE. Ensuring that employees use PPE correctly and consistently is fundamental. Conduct periodic checks to confirm that PPE is in good condition, and make sure that workers understand how to use it effectively.
6. Underestimating the Importance of Inspections
Routine inspections help identify potential hazards before they become serious issues. A common mistake is to overlook regular site inspections or perform them superficially. Dedicate time to thoroughly inspect the work area, machinery, and safety equipment to address any issues proactively.
7. Not Staying Updated on Safety Regulations
Safety standards and regulations are constantly evolving. New safety officers often miss updates on regulations, which can lead to non-compliance and fines. Regularly review safety guidelines, attend industry seminars, and stay informed on any changes to OSHA or local safety regulations.
8. Being Reactive Instead of Proactive
Waiting for incidents to happen before taking action is a big mistake. Proactive safety officers anticipate risks and address them before they become problems. Implement preventive measures and conduct hazard assessments regularly to ensure the workplace remains as safe as possible.
9. Failing to Engage and Motivate Employees
A successful safety program involves everyone, not just the safety officer. New safety officers often fail to motivate employees to actively participate in safety practices. Engage workers through training, meetings, and encouraging their feedback on safety protocols to create a culture where everyone takes responsibility for safety.
10. Neglecting Emergency Preparedness
Emergencies can happen anytime, and being unprepared can lead to serious consequences. New safety officers might overlook the importance of emergency response plans and drills. Ensure you have an updated emergency plan, and conduct regular drills so that everyone knows their role in an emergency.
Avoiding these mistakes can help new safety officers create a safer working environment and establish themselves as effective leaders in safety. By focusing on proactive risk management, clear communication, and continuous learning, you can build a strong foundation for a successful career in safety.
Tips for Success as a New Safety Officer
To excel in this role, focus on building strong relationships, both with your team and other departments. Stay updated on industry trends and prioritize ongoing education. Most importantly, be adaptable; safety management is an evolving field, and success depends on your ability to adjust and improve.
Conclusion
Becoming a successful Safety Officer requires more than just regulatory knowledge—it demands excellent communication, proactive management, and a commitment to fostering a safety-first culture. By avoiding these common mistakes, you’ll not only safeguard the workforce but also contribute positively to the organization’s safety record.
Becoming a Safety Officer in 2024: Education, Skills, and Career Path
Safety Officer Salary Trends in the U.S.: A 2024 Guide
What is the Salary of a US Safety Officer?
How to Become a Safety Officer in the USA?
FAQs
1. How can I improve my communication skills as a Safety Officer?
Focus on clarity and simplicity. Practice delivering safety messages in a way that everyone on your team can understand. Regular training sessions can also help refine your communication skills.
2. What is the best way to stay updated on industry safety regulations?
Regularly review OSHA guidelines or relevant industry standards, attend workshops, and consider joining professional safety organizations to stay informed.
3. How often should I conduct risk assessments?
It depends on your workplace and industry, but generally, quarterly assessments are advisable, with additional checks after any significant changes.
4. Why is record-keeping so important in safety management?
Good records help track patterns, provide evidence of compliance, and can be invaluable during audits or investigations. They’re essential for long-term safety planning.
5. How do I encourage employees to wear PPE consistently?
Lead by example, conduct PPE checks, and educate employees on the reasons PPE is necessary. Reinforce the importance regularly, and address any concerns about comfort or accessibility.